How to Calculate Inventoriable Costs
Introduction to Inventory Cost
Any company that handles merchandise incurs expenses necessary to produce, acquire, store, maintain, or sell products. These costs tend to vary between organizations, even if they handle the same items because they have different operations.
Manufacturers have inventoriable costs to supplement the labor, supplies, and equipment necessary to produce goods from scratch. However, retailers also experience these expenses by acquiring the finished product.
What are Inventoriable Costs?
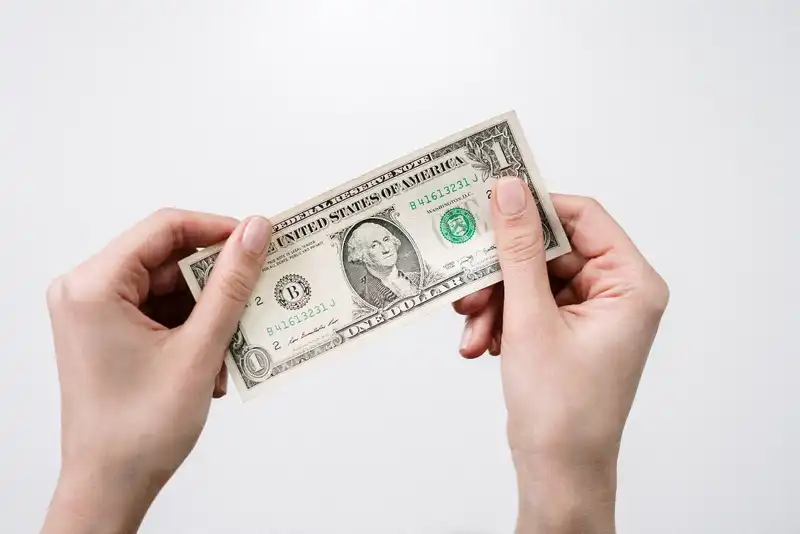
Inventoriable costs, also referred to as product costs, are the direct expenses necessary to manufacture and provide an item. These costs can include various elements depending on the business.
For example, a manufacturer has to supplement
- Raw materials
- Direct labor
- Freight
- Manufacturing costs or production overhead (machine depreciation, rent, utilities, management salaries, maintenance)
On the other hand, distribution centers and retailers have different direct and indirect costs.
- Purchase costs
- Transportation
- Storage
These costs may increase if businesses transfer products between different sites. Otherwise, the fee of inventory is charged to the company's expense account once it is sold or disposed of and is reported as the cost of goods sold (COGS) on the income statement. However, prior to the sale, the goods are recorded as an asset on the balance sheet.
It is important to remember that product costs tend to vary as they travel down the supply chain, as each business has their own definition of what is considered an inventoriable expense.
How to Calculate Prime Cost Per Unit
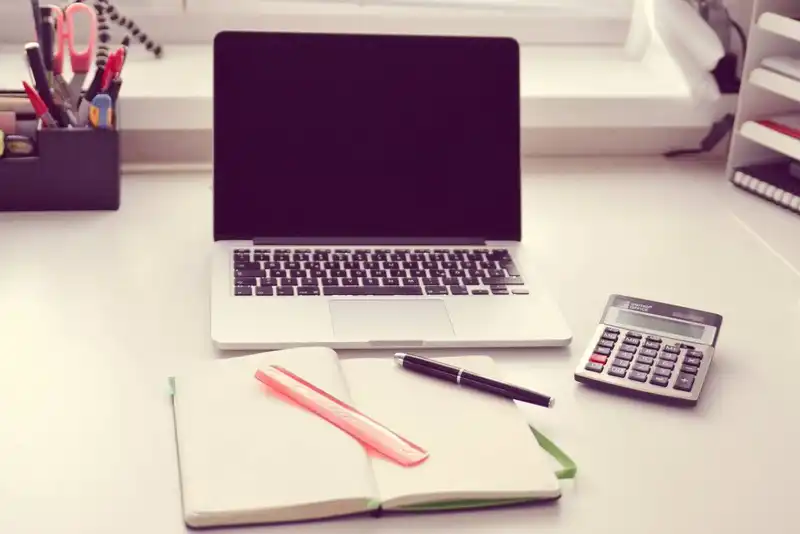
Assigning each unit's production cost requires managers to define all inventoriable expenses that are applicable to the batch at hand. By totaling all of the costs and dividing it by the number of units in the group, businesses can accurately determine the cost of each product.
Inventoriable Costs / Total Number of Units = Product Unit Costs
or
(Total Direct Labor + Total Materials + Consumable Supplies + Freight-in
+ Total Overhead) / Total Number of Units = Product Unit Cost
By calculating the product unit cost, companies can develop a pricing model to generate their ideal profit margin. It also enables managers to determine the minimum and maximum number of units they need to sell within any given financial accounting period to break even. This information is critical as it provides insight into an item's profitability and ability to supplement costs.
For example, a company manufactures televisions and records all of their inventoriable costs and finished units within the accounting period.
- Manual labor = $35,000
- Components = $65,000
- Consumable supplies = $3,000
- Freight-in = $5,000
- Overhead = $20,000
- Total number of units produced= 800 units
($35,000 + $65,000 + $3,000 + $5,000 + $20,000) / 900 units = $142.22
Based on the inventoriable costs, the company spends $142.22 to produce each television, meaning they need to charge at least $142.22 to break even.
If businesses are unable to sell products at their strategized price or sell enough units, they operate at a deficit and must supplement the loss from another product's profits. In response, many companies increase their retail prices, decrease production, or even close the product line.
Inventoriable Cost Terms
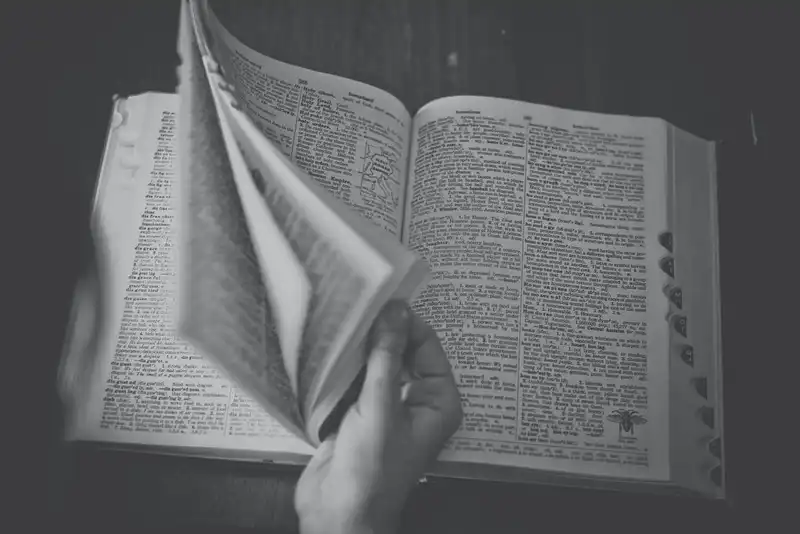
Management needs to familiarize themselves with common inventoriable cost terms to ensure they fill out financial statements correctly.
Direct Materials
Direct materials refer to all raw materials, components, and sub-assemblies that are required to build the finished goods.
Direct Labor
Direct labor is the expense of paying workers directly involved in the manufacturing process, including specific product assembly, the cost center, or a work order. For example, employees in the assembly line, supervisors, and technicians are all considered part of direct labor.
Freight-In
Freight-in refers to the cost of transporting goods and raw materials from the supplier to the manufacturer. This charge isn't finalized until the supplies are delivered to their destination.
Manufacturing Overheads
Manufacturing overheads, also known as production costs, refer to the expenses, other than fixed variable costs, that production companies incur during a specific manufacturing period. These fixed costs directly impact production, such as labor, raw materials, machinery, and utilities.
Period Costs vs. Inventoriable Costs
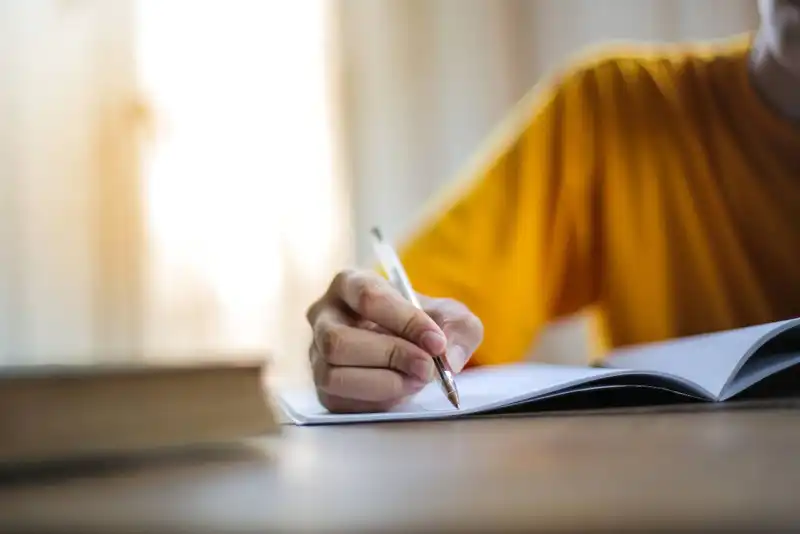
Business costs are categorized into inventoriable and period costs, based on if the expense is recorded as COGS.
As previously discussed, inventoriable costs are incurred during the manufacturing process and product acquisition. This means the cost is originally recorded as an asset and is not included in the balance sheet until the items are sold. After the final sale, inventoriable costs are charged to the expense account so companies can match their COGS with incoming revenue.
On the other hand, period costs refer to all expenses incurred outside of the inventoriable costs. Instead, period costs cover sales, marketing, administrative, and any additional general expense related to selling products. These fees are strictly recorded as expenses on all financial forms and are recorded within the year that they are incurred.
Therefore, businesses that do not handle production or product acquisition will have period costs rather than inventoriable costs.