Everything to Know About Warehouse Management
Warehouse management greatly contributes to customer satisfaction. In fact, research by PwC shows that while most consumers view free delivery as a standard feature in online shopping, 77% of consumers are generally willing to pay for same-day or next-day delivery.
Any business that handles large volumes of stock needs somewhere to store these items. In most cases, this is a distribution center, fulfillment center, or warehouse - a place to keep stock before they are moved to their final destinations.
Effective warehouse management ensures that these supply chain and logistics processes work as smoothly as possible. This efficiency is the key to offering quick delivery times and ensuring customers get the items they ordered without delays.
What Is Warehouse Management?
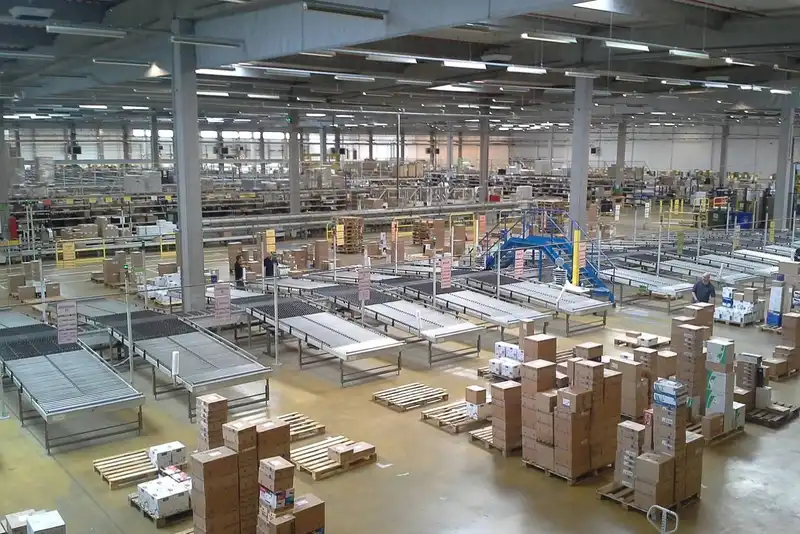
Warehouse management is the process of managing operations in a warehouse. As an aspect of supply chain management, it covers a wide range of tasks and processes that occur in a warehouse. These activities include-
- Warehouse inventory control and management, which includes receiving and storing stock in the facility
- Arranging the layout of the warehouse
- Order management, packing, and shipping orders
- Acquiring and maintaining warehouse equipment
- Transportation management
- Monitoring and improving warehouse performance
The idea is that the more efficient a business's warehouse operations are, the more likely it is to ship goods quickly and at the lowest cost possible.
According to research by McKinsey, companies worldwide spend around $350 billion a year on warehousing alone. And that number continues to grow each year, putting pressure on profit margins and service levels. That same report also found that companies that invest in warehouse improvements can cut their costs by up to 15% to 20%.
Primary Warehouse Management Processes
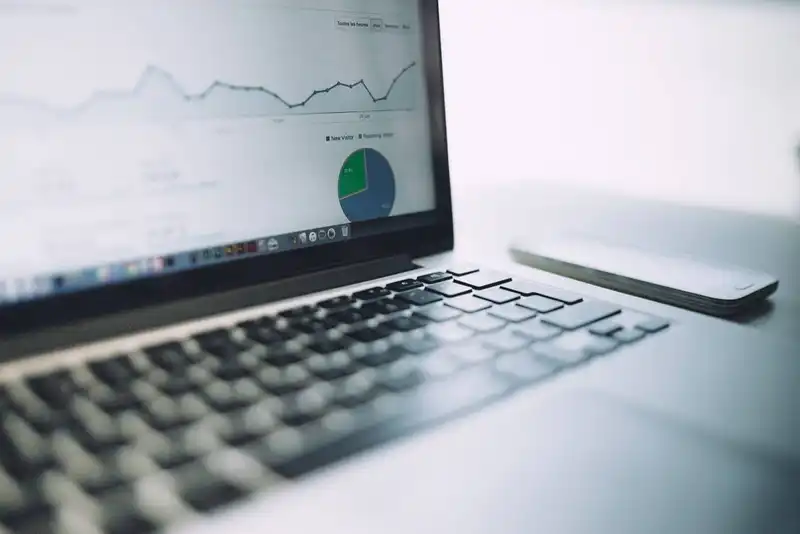
A company's approach to warehouse management is ultimately based on its objectives. For example, a large retailer will naturally prioritize shipping and last-mile delivery. A food and beverage company, on the other hand, may focus on proper storage to protect perishable and temperature-sensitive food and beverage products.
All that being said, most companies will have these warehouse management processes happening in their facilities.
- Inventory Tracking
It sounds simple enough, but inventory control and management is the third leading supply chain challenge. This is a task that only gets more complicated as the business grows and turns inventory over faster, expands to new locations, and diversifies its product lines.
- Receiving and Storage
The new box will then be moved to its short-term or long-term storage location, where it will be scanned once again. This creates a real-time record of each SKU's location in the warehouse and overall supply chain.
- Picking and Packing
Packing, on the other hand, is the process of placing items into the proper box for shipping. When a customer orders an item, the WMS provides a pack list of all orders for a corresponding shipping batch.
- Shipping
Once the parcel leaves the warehouse, the WMS will automatically send the customer an update of their order fulfillment status and tracking number via the eCommerce site, email, and/or SMS.
- Reporting
Reports can also be integrated with the organization's enterprise resource planning (ERP) system to leverage functions such as inventory forecasting. This helps warehouse managers plan for future inventory holding costs and staffing needs.
The Basics of Arranging a Warehouse
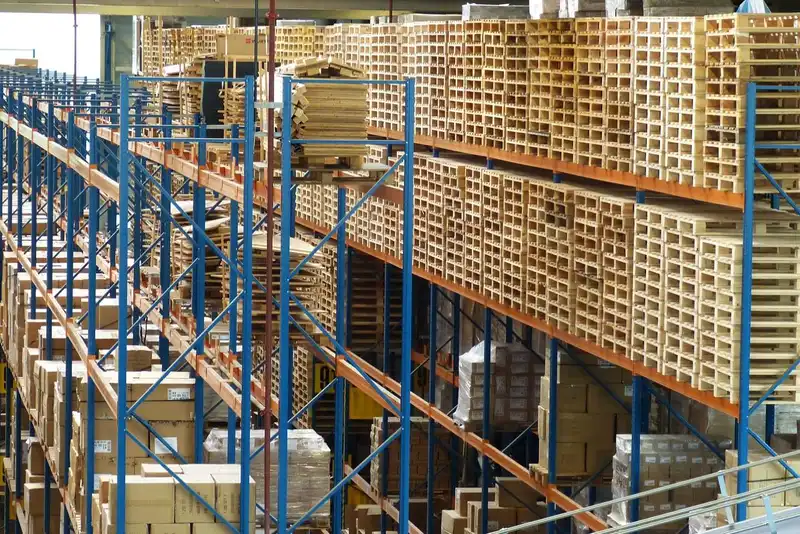
While the ideal layout, order, or organization of a warehouse is subjective, there are some best practices worth following when arranging a warehouse for optimal operations.
1. Plan the Layout on Paper
When planning a warehouse's layout, there are two crucial factors to consider-
- Providing sufficient shelves for inventory storage
- Providing sufficient working space for staff to walk around
This means that a warehouse should ideally have dedicated spaces designed for these areas and activities-
- Receiving new stock from trucks
- Unpacking and booking new stock (i.e., material handling)
- Packing station
- Shipping area
- Warehouse office for administrative staff
- Primary storage area
- Storage area for dead stock, excess stock, and obsolete goods
Admittedly, having separate areas for all of these things can be challenging, especially when warehouse space is limited. The trick is to sketch the warehouse layout to scale and arrange things on paper first. Try to strike a balance between space for inventory and maneuverability for staff.
2. Label Warehouse Spaces
Before stock can be labeled and sent to storage, the warehouse must already have set location names. Properly labeling different areas in the warehouse ensures that teams can efficiently locate and retrieve any product at any time.
The key is to keep the warehouse's labeling system simple and practical. Short alphanumeric combinations are ideal as they are easy to read and decipher for pickers. For example, warehouse managers can label storage areas by-
- Aisle - The walking space between racks
- Rack - The section of shelving units.
- Bin - This is a storage type, such as a box, within a location that houses spaces or slots for goods.
- Shelf/row - This is the horizontal space spanning the length of the rack
For example, by using this system, pickers will know that boxes of a particular item will be in Aisle 03, Rack C, Bin 4, Shelf 03. This can be shortened to A03-RC-B4-S01.
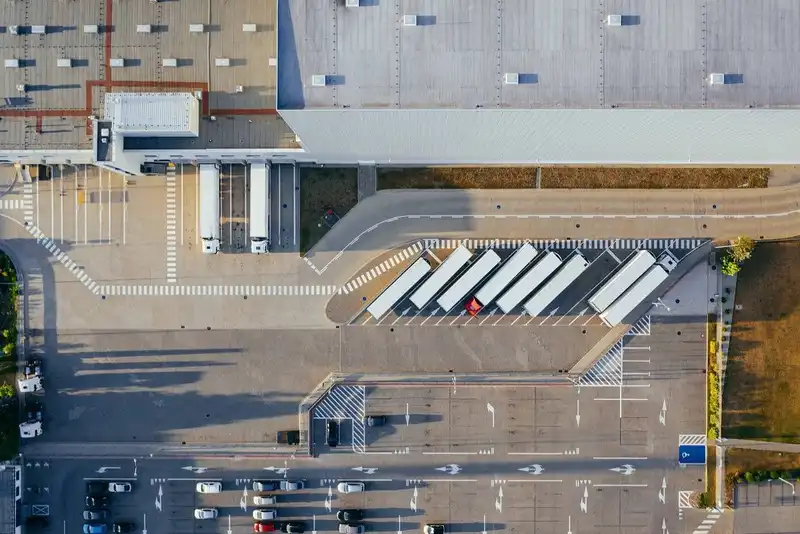
3. Arrange Inventory
With the warehouse laid out and locations labeled, the next step is to arrange the inventory. Again, different companies will have their own ways of doing things. But a good rule of thumb is to place the more popular items closer to the packing stations for speed and efficiency.
To organize inventory by sales volume or popularity, warehouse managers can use the ABC method-
- A-goods - These are the best selling items that very briefly occupy warehouse space and don't incur high holding costs.
- B-goods - These items regularly sell well but cost more to keep in stock than A-goods.
- C-goods - These items account for most of the company's inventory holding costs and generate the least amount of revenue.
The idea is to make it easy for pickers to quickly find and bring goods to packers. It's even possible to keep small and lightweight items that are sold frequently on shelves near the packing desks themselves.
4. Rearrange the Warehouse When Necessary
Warehouse managers can make the mistake of not wanting to rearrange their warehouse. While changing the layout and system of arranging inventory can take time and resources, the increased efficiency can significantly reduce the company's overall supply chain management costs.
It is also worth noting that inefficiencies requiring warehouse adjustments can happen at any time. For example, a retailer's best selling products last year may no longer be as popular this year. Best Selling items in the summer may become the worst-selling in the winter due to seasonal demand.
5. Acquire the Right Equipment
The right equipment is essential to achieving warehouse operations efficiency. Consider acquiring the following-
- Shelves and rack units
- Bins
- Picking carts
- Packing desks
- Packing materials, including boxes, tape, bubble wrap, and air pillows among others
- Printers (for labels and invoices)
- Shipping computers
- Barcode scanning tools
- Shipping scales
- CCTV cameras (to deter theft)
How to Receive and Manage New Inventory
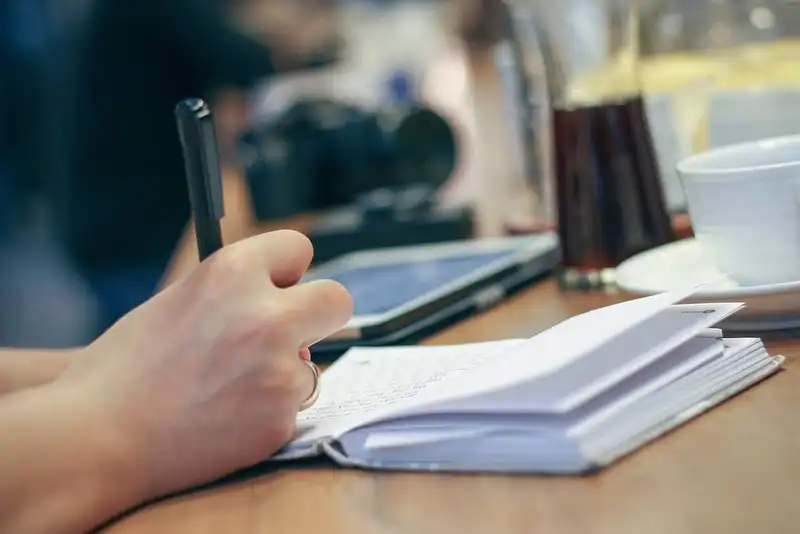
Warehouse processes must have efficient systems for receiving, unpacking, putting away, and booking in new inventory. The faster this process is, the sooner the items become available to customers. The basic elements and steps for receiving new inventory include-
- Identifying a workspace for receiving and processing newly delivered stock
- Assigning a team of warehouse workers
- Recording all information about newly received inventory
- Unpacking and inspecting delivered goods carefully
- Putting away inventory after they have been labeled accordingly
- Updating inventory records to reflect the latest stock levels
Generally speaking, there are two ways to execute these steps-
1. Pen and Paper
The traditional way of receiving and recording new inventory is with a pen and paper. This means checking the paper purchase order (PO), counting the delivered inventory, and verifying if the quantities are consistent with the PO.
However, there are many downsides to this approach. For starters, manually checking inventory and reading POs is slow and creates time lags between receiving stock and making it available for sale. It also leaves warehouse operations susceptible to human error.
2. Automated Warehouse Management System
A WMS system automates many of the manual and repetitive steps involved when receiving new inventory. For example, the WMS can contain a list of all active POs. On the day of delivery, simply pull up the matching PO for the shipment to receive new items into inventory. If the delivered items match the PO, the user can verify the new inventory and the WMS automatically updates the warehouse's stock levels and/or assigns items to any open backorders.
A barcode scanner device further improves the functionality of a WMS. Employees can use it to quickly scan purchase orders and labels on products, automatically adding them to the inventory management system.
What to Look for in a Warehouse Management System
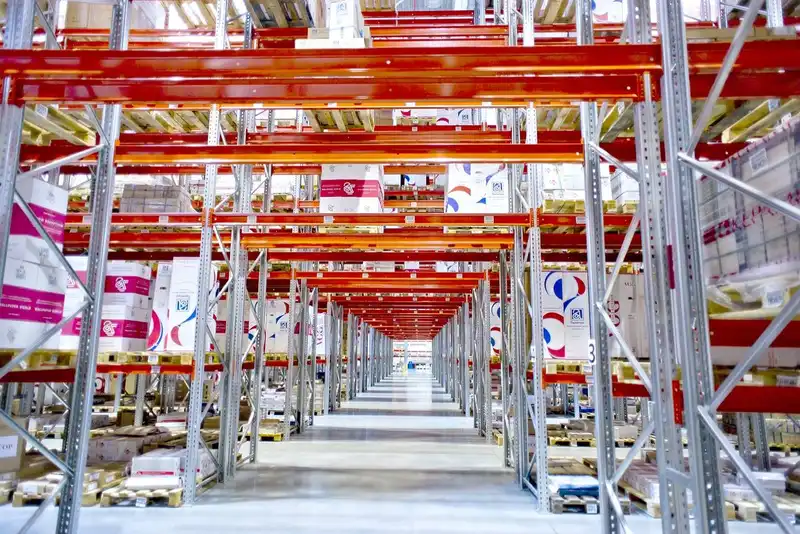
The wide range of warehouse management software on the market can make it difficult to settle on one WMS. When shopping for these software products, consider these factors-
- eCommerce Integration - A WMS that integrates with the business's online store makes it easy to send order status updates and tracking information to customers. Warehouse operators can also monitor sales trends in real-time to support demand.
- Compatibility With Existing Equipment - Consider looking for a WMS that is compatible with the inventory scanners, terminals, printers, scales, and wearable devices already present in the warehouse.
- Measurable Returns - A WMS must have a robust built-in analytics system that can track key metrics such as parcels fulfilled and the total number of on-time orders.
With the right WMS, warehouse managers can eliminate guesswork from their processes, leverage business intelligence to streamline their operations, and save both time and money.