How to Calculate and Lower the Total Inventory Cost
When a business optimizes their inventory, they lower stock related expenses, such as carrying and holding costs. By maintaining target stock levels and meeting consumer demand, businesses can increase their stock turnover rate and profits.
However, to achieve inventory optimization, companies must first determine their total inventory cost, from purchasing to holding fees. Calculating capital spent on inventory allows businesses to pinpoint and adjust any excessive inventory-based fees to lower total expenditures.
Calculating capital spent on inventory can also help determine a company's economic order quantity (EOQ), ensuring healthy stock levels and limiting order spending.
Calculating Total Inventory Cost
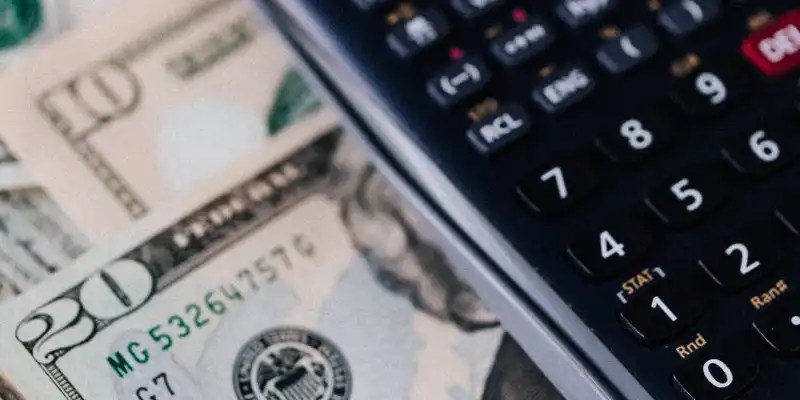
A business's total inventory cost combines all fees associated with handling stock to determine how much capital is in inventory versus how much profit products bring in per unit or per year.
The variables in the inventory cost formula include-
- Ordering costs - Any expenses incurred from placing stock orders
- Shortage costs - All extra fees that are required to counteract a stock shortage
- Carrying/Holding costs - Capital invested in warehousing stock or holding stock in-store
Once these values are determined, they are added together to find the total inventory cost.
Total Cost = Order costs + Holding costs + Shortage costs
Businesses can also use the extended total cost formula to calculate their annual inventory cost and ordering and holding fees-
Total Cost = DC + (Q/2) H + (D/Q) S
D = Annual Demand for an item
C = Cost per Unit
H = Annual holding cost per unit
S = Cost to place one order
Q = Quantity size
In this formula, (Q/2) H represents the annual holding cost, while (D/Q) S refers to the yearly ordering cost. The extended total cost formula breaks down the simple addition of total inventory cost so businesses can understand exactly where the expenses lie. By showing how ordering and holding expenditures are calculated, the formula allows the user to control the quantity size.
Determining inventory expenditures through total cost and EOQ calculations can save businesses capital tied up in unnecessary spending.
Order Costs
This includes all expenses required for ordering inventory, including fees for order placement, vendors, labor, and inspection of goods. Order costs are usually fixed, so they do not change significantly with varying quantities but can add up depending on how many orders are placed. Therefore, companies can save money by consolidating purchases into one order and paying a flat rate rather than paying multiple fees.
Shortage Costs
Shortage, or stockout costs, are more unpredictable as they can vary in value. When companies experience stock shortages, they react in different ways. Some may expedite shipping while others find new vendors or material substitutions. These various measures taken to bring stock levels back up quickly can result in increased inventory costs.
Implementing inventory control measures, such as safety stock and automated replenishment systems, can help in preventing expenses associated with stockouts.
Carrying Costs
Also known as holding costs, these expenses usually make up the most substantial portion of the total cost. Carrying costs include any payments to warehouses, labor, insurance, and the price of any damaged or spoiled goods. Ideally, holding costs should make up 20-30% of the inventory value. These costs can also vary depending on the order quantity.
How to Reduce Inventory Costs
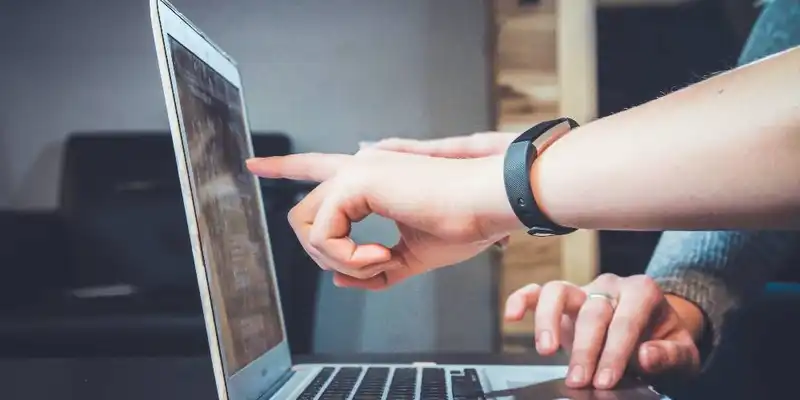
Optimizing inventory by decreasing stock levels can reduce costs relating to discrepancies, production, ordering, and holding by consolidating and limiting excess material.
Other tips on how businesses can use inventory control to minimize total stock costs include-
1. Always keep inventory levels updated - Implementing an inventory software keeps all stock information updated at all times. Software integrates with barcode scanners and point-of-sale (POS) systems to track every shipment, scan, and transaction. With perpetual stock tracking, businesses can determine if more products should be ordered to maintain healthy levels. This practice saves businesses unnecessary ordering and handling fees, lowering their total costs.
2. Review the SKUs - Stock-keeping unit (SKU) refers to the alpha-numeric code uniquely assigned to each product by a business. Understanding the assignments of these codes can help management better analyze consumer demand. By increasing the usage of SKUs across all items, customer demand is more defined for each product.
For example, some businesses have low SKU intensity, meaning they have one SKU code for all units of an item. On the other hand, another company may generate multiple SKUs for the same product that is offered in different colors. This breakdown of products by specific physical attributes and higher intensity of SKU codes give management new insight on what products consumers are buying.
3. Determine the reorder point and implement automated replenishment - Reordering stock should not occur when a business runs out of the product, as waiting for incoming shipments can cause stockouts and increased ordering costs. Determining a reorder point creates a threshold that signals when inventory is running low and more orders should be placed. This can assist businesses in maintaining healthy stock levels and preventing expenses associated with shortages.
Reorder points can be inputted into replenishment software that alerts management when product levels are low and place new orders automatically. By constantly tracking inventory volumes and replenishing stock before it's too late, businesses can avoid the risks and expenses involved with under and overstocking.
Costs incurred by the ordering and handling of inventory can significantly affect a business' bottom line. Monitoring the company's financial statement and lowering the total inventory cost by reducing purchases on excess stock can help companies increase their profits.