How to Calculate the Reorder Point For Small Businesses
Businesses should monitor their inventory levels closely to avoid stockouts and late shipments, which can lead to declining sales and unsatisfied customers.
Companies can accurately pinpoint when to replenish their stock using a set reorder point by balancing daily product usage and order fulfillment time.
Replenishing inventory on hand using a calculated reorder point and maintaining the economic order quantity ensures there is an adequate amount of raw material to meet daily usage and customer demand, without the risk of overproducing.
What is a Reorder Point?
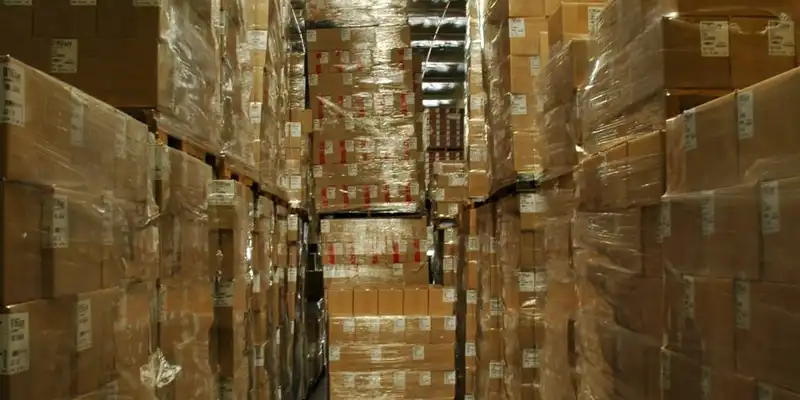
Maintaining optimal stock levels is a balancing act for any company, but formulating a reorder point can prevent the stress of stockouts and overproduction.
A reorder point establishes the lowest amount of stock a company should have in the warehouse at any given time. Once levels reach the reorder point, it is time to replenish inventory.
Establishing a reorder point prevents expenditures on holding fees from ordering too much stock and missing sales from stockouts. Many businesses also carry safety stock, an additional quantity of inventory reserved in case of stockouts, as a precaution.
A study conducted by the IHL group showed that retailers had lost nearly $1 trillion in sales worldwide due to stockouts. Missed sales opportunities from not ordering a sufficient amount of materials can cause a great dent in revenue. On the other hand, Retail Wire found overstocking has been costing retailers over $123 billion annually, taking away from businesses' bottom line.
Calculating the Reorder Point
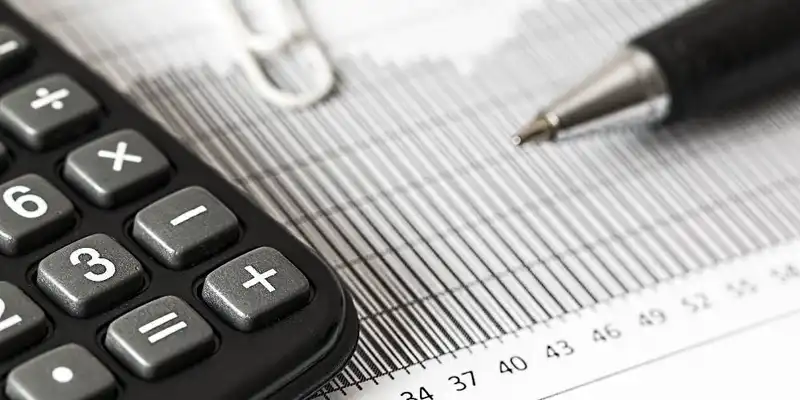
To calculate the reorder point, the safety stock quantity and lead time demand need to be established first.
Lead Time
Lead time refers to the amount of time it takes for a customer to receive their item, starting from when they place the order to when the order is delivered. This metric allows the distributors to assess the consumer's wait time and determine how to increase their production efficiency to improve customer satisfaction.
Lead time is easily calculated by adding up the days it takes the supplier to produce and deliver the ordered item. For example, if an order is placed on Monday, and the customer receives the items on the following Monday, the lead time was seven days.
However, finding the lead time demand requires multiplying the lead time by the daily demand average to discover how many units production must create to fulfill the demand for a specific period.
The lead time demand formula is-
Lead time demand = Avg. daily sales x Lead time
For example, if a company has a lead time of 7 days and gets an average of 10 sales a day, their lead time demand equation setup would be-
70 items = 7 days x 10 sales / day
This calculation shows that according to daily sales, the company would need to order 70 items to be able to adequately fulfill orders.
Safety Stock
Safety stock comes in handy when there is a sudden surge in customer demand, or when local suppliers cannot fulfill their standard orders. This inventory acts as a buffer to prevent stockouts and total material depletion, so production can continue operations.
To calculate the appropriate safety stock quantity, companies must understand their maximum lead time and average daily usage rate. Then, the safety stock can be calculated using the following formula-
Safety Stock = (Max. daily usage x Max. daily lead time) (Avg. daily usage x Avg. daily lead time)
Using the previous example, if the company's average daily sales are 10 items, but a seasonal spike has increased this to 17 and their lead times are usually between seven to 10 days, their equation would look like-
100 units = (17 items x 10 days) (10 items x 7 days)
This calculation shows that the company from the example should maintain 100 units of safety stock.
Reorder Point
With the lead time demand and safety stock determined, the reorder point can be calculated by adding the two together-
Reorder point = Lead time demand + Safety stock
Continuing the same example, the company can calculate its reorder point with the following equation-
170 units = 70 units + 100 units
According to the formula, once the company's stock levels deplete to 170 units, another order needs to be placed.
Businesses should recalculate their reorder points when there are changes in vendors, daily sales, delivery times, or demand forecasting. However, it is common practice to calculate this figure quarterly for quality assurance.
Monitoring reorder points can also be automated using replenishment systems. Management will get an alert when the reorder point has been reached, allowing them to place orders automatically. Replenishment software can also analyze purchase history, seasonal sales changes, and usage rates to formulate an optimal reorder rate.
To calculate reorder points, businesses must first have an understanding of their safety stock, varying lead times, and demand rates. By determining an accurate reorder point, businesses can increase their bottom line by saving on expenses pertaining to storage and expedited shipments, while ensuring daily unit sales are met.