How to Calculate Inventory Levels and Keep Them Low
Inventory control affects a business's production efficiency, customer satisfaction, and ultimately, their bottom line.
Ordering inventory refers to the replenishment of raw materials necessary for a company to produce a specific item. While businesses aim for high production that meets customer demand to increase profits, inventory levels should remain relatively low to reduce holding costs, conserve space, and maintain organization.
However, each business is responsible for determining their own economic order quantity or optimal inventory level required to meet demand while avoiding excessive storage costs or wasted materials. Discovering the ideal inventory level improves productivity, customer service, and reduces inventory-related costs by ensuring there are enough materials for production and customer demand.
This article will discuss the different types of stock levels and how to make maintaining low inventory easier with automated inventory management systems.
The Four Types of Stock Levels
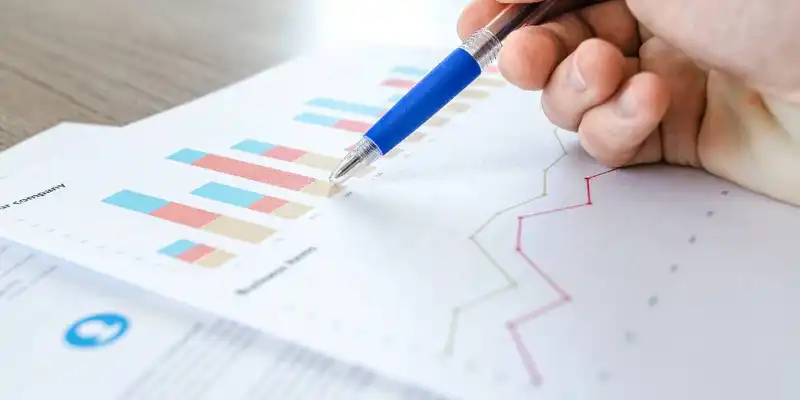
Businesses should have different levels of stock on hand that keeps the amount of inventory in check. While it is ideal to have just enough stock to meet customer demand, implementing different levels creates safety precautions to prevent under and overstocking.
1. Minimum Level - Minimum stock levels must be maintained to guarantee enough materials to continue production. Failure to meet the minimum level could result in stopping operations due to stockouts. Minimum levels are unique to each business and should consider the following supply chain elements-
- Lead time - The amount of time it takes for a customer to receive the product, from the moment they place the order to when the product is delivered.
- Consumption rate - The average trend of material consumption in the industry based on past production experience.
- Nature of Material - If a limited, special order requires a specific material, said material does not need to meet the minimum stock requirement. For example, if a canvas distributor receives a one-time order for a canvas with specific dimensions that are not typically offered, materials ordered for this purchase do not need to meet the minimum level as they must only satisfy one order.
- Reordering level - When materials are depleting, before they reach minimum stock levels, another purchase order should be placed to avoid stockouts. Reordering levels are fixed at a reorder point between the minimum and maximum levels and can be calculated using the following formula-
Once the production time, demand and consumption rates are determined, the minimum stock level can be calculated using the formula-
Min. level of stock = Reorder level (Avg. usage x Avg. lead time)
2. Maximum Level - On the other end of the spectrum, a company should not exceed the maximum level to avoid overstocking. Excess inventory can lead to disorganization, high holding costs, and increased probability of stock discrepancies. Determining a maximum stock level depends on-
- Capital available for material orders
- The maximum requirement of materials
- Space availability in storage
- The fastest rate of consumption
- Cost of store maintenance
- Possible material price changes
- The shelf life of materials
- Availability of materials
- Government restrictions
- Possible change in consumer demand
The maximum stock level can be calculated using Wheldon's formula-
Max. Stock Level = Reordering level + Reordering quantity (Min. consumption x Min. reordering period)
3. Danger Level - A company should never reach the danger stock level, as it indicates the inventory supply is nearing stockout. If the danger level is reached, the company should consider expediting more materials, even if it means extra fees.
Calculating the danger level is simple-
Danger level = Avg. consumption x Max. reorder period for emergency purchases
4. Average Level - As it sounds, the average stock level is the average quantity of stock found in the warehouse at any given time. Average stock level is calculated by-
Average stock level = Min. stock level + of Reorder quantity
How to Maintain Low Inventory Levels
Maintaining low inventory levels that can still meet the demand but do not result in excess product is every business' goal. Minimum inventory levels have many benefits, including-
- Reduced holding/storage costs
- Easier organization
- More space
- More available capital
- Reduced risk of discrepancies
- Improve supply chain management
There are several ways to keep inventory low to promote efficiency and save on unnecessary fees associated with overproduction-
1. Reduce supplier lead time - Supplier lead times can be negotiated for faster material delivery and lower shipping costs. If the vendor is unable to meet the business's desired lead time, other suppliers capable of meeting the replenishment demand can be contacted.
Slower lead times require distributors to order what is known as safety stock, an extra quantity of materials ordered to prevent stockouts. Faster lead times will give businesses flexibility in their reorder levels, reducing carrying costs and the risk of spoilage.
2. Eliminate obsolete stock - Items that are no longer in demand are known as obsolete stock and can damper a business's profitability. Financial reporting should be monitored continuously to see each product's life cycle and sale rate. When a product becomes obsolete, it racks up storage costs and space that could be used for high-profit items. These obsolete products can be sold at a discounted price or disposed of to optimize stock levels and space.
3. Optimize order size and frequency - Demand forecasting and accurate inventory system tracking can support management's decision on how much material to order to meet customer demand without overproducing. By placing smaller, more frequent orders, distribution centers can limit physical inventory on-site, allowing more order flexibility.
Implementing Automated Ordering Systems
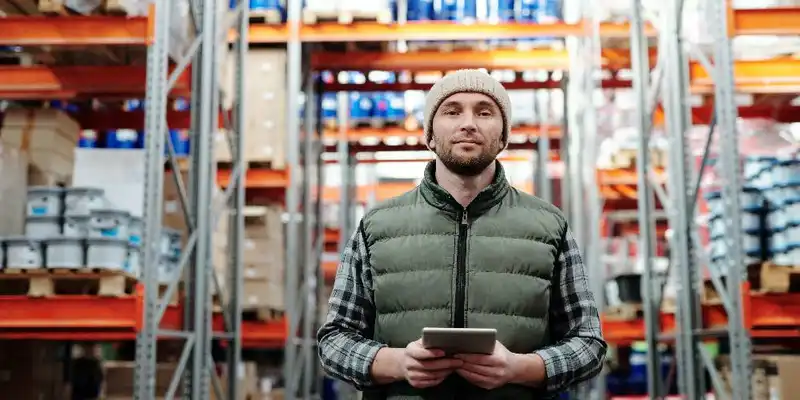
Inventory replenishment can become overwhelming especially when dealing with large quantities of stock across multiple locations. However, automated software can make managing inventory volumes efficient and stress-free.
Stock replenishment software integrates with point-of-sale (POS) systems and barcode scanners to continually monitor stock levels and alert management when stock is nearing danger levels. These systems can be programmed to automatically submit reorders when stock has depleted to a certain level.
Implementing an automated replenishment system helps companies-
- Reduce process costs
- Maintain minimum stock levels
- Increase turnover rates
- Reduce waste
- Improve space availability
Management must continuously crunch numbers from inventory and financial reports to determine exactly how much physical stock is appropriate to keep in-store. This process can be simplified by integrating an automated replenishment system that monitors sales, demand, and product levels without the worry of human error.
By maintaining minimum stock levels, businesses can prevent wasted expenditures on under and overstocking and instead, focus on customer satisfaction and business expansion.