What are the Most Popular Supply Chain Models?
An incredible 57% of companies gain a competitive advantage through efficient supply chain management strategies, yet 69% of companies confess they don't have complete visibility of their supply chain network.
Additional and extensive surveys have further revealed that supply chain disruptions can cause significant losses in terms of finances, logistics, and reputation, which gives companies a clear indication of just how important supply chain optimization and inventory management are.
The Fundamentals of Supply Chain Structure

At its very essence, a supply chain boils down to the process that helps a product or commodity move from the manufacturing stage to the market. This factors in the people, equipment, transportation, and technology involved in the processes that make up that sequence of events.
While the word chain may imply a straight line that simply runs from raw materials, to the supplier, to the manufacturer, and then the consumer, in today's fast-paced and tech-infused global supply economy, a supply chain is more akin to an intricate web with the manufacturer at the heart.
These webs are referred to as supply chain modeling and they can vary, morph, and change depending on a businesses' unique supply chain requirements. Some supply chain models require flexibility and adaptability to frequent change, while others need outstanding levels of efficiency - especially in fiercely competitive markets or industries.
No matter the form, supply chain modeling is used to empower a company to make the correct supply chain decisions and adopt the best practices to bring order into the supply chain while ensuring it aligns with the operational objectives. These objectives can range from timely delivery to the ability to cope with threats or disruptions.
Benefits of Supply Chain Modeling
Supply chain modeling at its best allows a company to manage its supply lines in the most effective means possible while delivering a wealth of benefits such as effective problem resolution and increased visibility across all facets of the chain.
Some key benefits of supply chain planning and modeling include-
- Expect the Unexpected - Supply chain modeling that incorporates simulation models can help companies anticipate disruptions and effectively prepare for them.
- Greater Inventory Control - A supply chain strategy that is reliable and completely in sync with all inventory needs and potential issues means greater control over the stock flow.
- Greater Efficiency and Reduced Costs - A model that contains transparent supply chain costs at all stages allows a company to not only compare costs to key metrics but also make ongoing adjustments when required.
- Ensuring Greater Accuracy in Supply Chain Logistics - A good supply model will plate up hard data that includes logistics, service coverage, times, and facilities to reduce the need for estimates and enhances the decision-making process.
Most Common Supply Chain Models
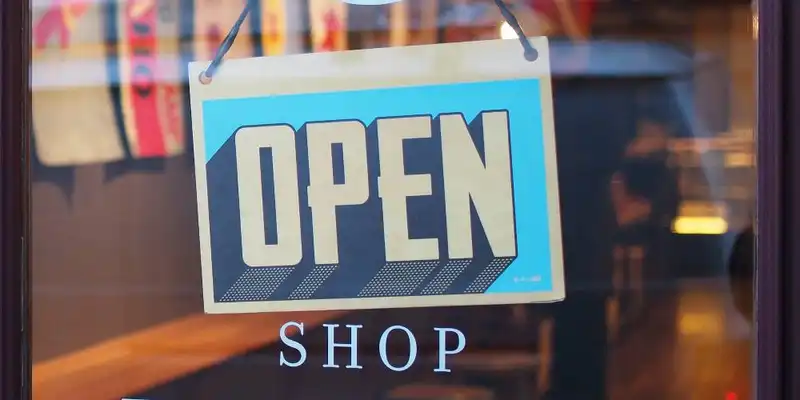
Supply chain models can be broken down into two primary categories - efficiency and responsiveness.
The efficient models tend to work best in highly competitive industries or markets that are schedule-based with an aim to maximize efficiency across the supply chain and utilize all assets at a lower cost. A responsive supply chain model, on the other hand, is used primarily in industries or markets with high levels of uncertainty or when mediation costs are the highest priority.
The following 3 supply chain models are categorized under the efficiency category-
1. The Efficient Supply Chain Model
With a focus on high-level efficiency from raw material production right through to the delivery of the end-product to consumers, this model works well with commoditized businesses where the rate of production is not only scheduled but in sync with predicted sales.
This model further complements industries where competition is largely based on the price, such as the steel industry, or where market competition is rife. Accurate forecasting and the use of machinery to reduce costs and maintain efficiency is key to the success of this model.
2. The Fast Supply Chain Model
In industries subject to fast-changing fashions, such as clothing or furniture, the fast supply chain model is highly recommended as it allows companies to utilize a system that treats time as a commodity. By reducing the time from idea to market and incorporating highly accurate forecasts, the fast supply chain model empowers companies to efficiently deliver products with reduced lifecycles based on changing fashions or trends, and thus lowering market mediation costs. It also allows for greater end-to-end efficiency to reduce expenses.
3. The Continuous-Flow Model
Companies in mature industries that require high demand stability frequently adopt the continuous flow model as it enables them to create an ongoing and reliable flow of products and information. Industries with little movement in the customer demand profile also benefit from this format.
The following 3 supply chain models fall under the responsiveness category-
4. The Agile Supply Chain Model
For companies operating in an industry that has unpredictable demand, the agile supply chain model is beneficial as it is based on a make-to-order decoupling point. This essentially means that a product is made after the customer order is placed. This system also works well for companies that deal in small batches as it enables managers to keep a tight rein on those stock levels.
5. The Custom-Configured Model
This model is incredibly effective in industries where product configurations are regularly required, such as motor vehicle companies. This model incorporates a strong correlation between the asset and total cost while combining elements from both the continuous flow model and the agile model.
6. The Flexible Supply Chain Model
Industries that are impacted by high peak seasons work best with a flexible supply chain model as this highly flexible and adaptable system allows management to rapidly reconfigure manufacturing processes to meet last minute and specific customer requirements. Flexibility is crucial in this system, alongside fast responses.