What Is Supply Chain Management? Process, Best Practices & More
The concept of supply chain management has been around for decades. But in recent years, supply chains have come under the spotlight for their potential to make or break companies.
In 2014, a Deloitte survey revealed that 79% of companies with effective supply chains achieve above-industry revenue growth. Fast forward to 2019, and the same holds true. According to an Accenture report, 46% of companies that integrated digital business intelligence into their supply chains met or exceeded their return on investment. On the other hand, failing to optimize the supply chain can lead to inefficient operations, poor vendor relationships, and decreased visibility of inventory movement.
But what is supply chain management and how does it work?
In a nutshell, supply chain management (SCM) is the process of managing the movement of a company's supplies, products, and services in the most efficient and economical way possible. And in today's global and omnichannel marketplace, supply chain management has emerged as a vital tool to stay competitive.
Understanding Supply Chains

A supply chain is an umbrella term that refers to the series of steps required to build and sell products and services. This includes-
- The sourcing of raw materials from suppliers
- The manufacturing of goods or development of services
- The movement of finished products from the warehouse/distribution center to the dealer or retailer
- The sale of final products to the customer
Benefits of Supply Chain Management
As previously mentioned, companies with effective supply chain management practices tend to see more revenue growth. But the benefits of supply chain management are more far-reaching than you might think. These include-
- Improved Collaboration - According to an Oracle report, half of the companies with fragmented supply chains suffer lost sales opportunities due to the inefficient sharing of supply chain information.
- Risk Management - Getting both a full and granular view of the supply chain can reveal risks such as potential quality control problems and disruptions. In turn, understanding these risks opens up opportunities for efficiency; Oracle found that 87% of companies could reduce their inventory by 22% simply by having better supply chain visibility.
- Lower Overhead Costs - Managing supply chain activities, such as warehousing and demand predictions, allow companies to reduce overhead costs associated with stocking and slow-moving inventory.
- Increased Efficiency - Things like managing the movement of raw materials and preventing manufacturing delays allow companies to increase productivity and reduce inefficiency.
Supply Chain Management vs. Logistics
The terms supply chain management and logistics tend to be conflated, as both involve the movement of commercial products and materials. However, logistics is just one component of supply chain management. It specifically refers to the movement and storage of goods both inside and outside the company at the right place and at the right time.
Supply chain management is far more expansive, involving activities such as product development, procurement of raw materials, distribution of final products, finance, and customer relationship management.
6 Components of Supply Chain Management
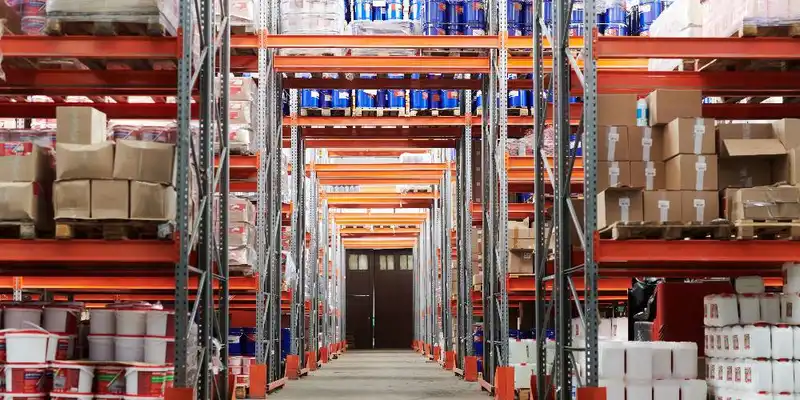
To better understand how the supply chain works, it helps to get familiar with the usual processes involved in supply chain management. One way to do this is by understanding the components of the Supply Chain Operations Reference (SCOR) model.
Originally developed by management consulting firm, PRTM (a PwC subsidiary), and later endorsed by the Supply Chain Council, the SCOR model provides a framework of best practices spread out across six basic supply chain components.
1. Planning
Planning involves determining the requirements, resources, and communication of any supply chain process. This can include analyzing the demand for a product, checking regulatory compliance, running cost analyses, and planning current and future labor needs among many others.
2. Sourcing
The Sourcing component involves the procurement of raw materials, supplies, and services needed to build your offering. The priority is to get the best possible price without sacrificing quality. Once suppliers are under contract, the next challenge will be monitoring and managing your supplier relationships to maintain the quality and optimal flow of supplies.
3. Manufacturing
Making (or Manufacturing) is where assembly, testing, and packing activities take place. This also includes the measurement of product quality, manufacturing output, and worker productivity and efficiency to ensure that quality standards are being met.
4. Delivery
Also known as logistics, the Delivery component covers-
- Processing customer orders
- Distributing orders to warehouses
- Transporting orders from warehouse to dealer or distributor
As you may have guessed, this component also includes inventory and warehousing, regardless of whether the business contracts a third-party provider to handle these processes.
5. Returns
All businesses need a system that ensures customers can smoothly and quickly return defective items. This system must also account for handling end of life goods - usually products that are phased out or removed from the inventory due to low demand.
For defective goods, the Returns component must outline rules for tracking the performance, costs, and inventory of returned goods. Such rules can include-
- The condition of the item
- Requirements for returning items
- Refunds
- Lead times for replacement product shipments
6. Enabling
The Enabling component involves the creation of processes that support information flow throughout the supply chain as well as its ability to comply with regulations. These supporting processes include human resources, IT, product design, marketing, sales, and quality assurance among others.
4 Stages of the Supply Chain Management Process
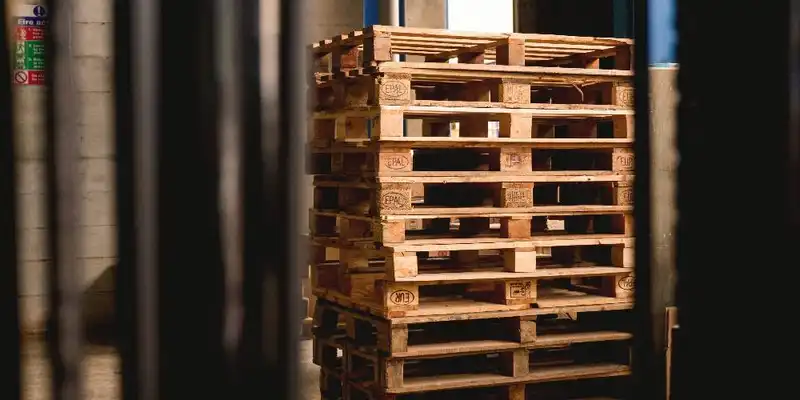
While different companies manage a myriad of activities in their supply chains, most will fall under these primary processes - demand management, product portfolio management, sales and operations, and supply management.
1. Demand Management
Demand management is composed of-
- Demand Planning - This is the process of predicting customer demand, ensuring that a sufficient quantity and variety of products can be delivered to meet your customers' future needs without having a surplus.
- Merchandise Planning - This involves planning, purchasing, and selling merchandise. The goal is to maximize return on investment and make sure that customers can purchase your products at the right place, time, and price.
- Trade Promotion Planning - Trade promotions are a marketing tactic designed for general retail sales through time-sensitive offers, special pricing, value-added bonuses, product bundles, and no-obligation deals among others.
2. Product Portfolio Management
Product portfolio management covers activities involving the design, development, manufacturing, and market introduction of products. It also involves creating an exit strategy for products that are no longer profitable or need to be replaced by a superior product.
Examples of product portfolio management activities include-
- New Product Introduction (NPI)
- End-of-Life Strategy
- Cannibalization Prevention
- Brand Planning
- Portfolio
- Platform Planning
3. Supply Management
Supply management is focused on coordinating assets to ensure the efficient, smooth, and on-time delivery of products, services, and information from the business to the customer. A supply management suite includes activities such as-
- Supply Planning - This involves identifying the strategies necessary to meet the requirements outlined by the demand plan. The goal is to balance supply and demand to meet business goals while minimizing surplus.
- Production/Supply Planning - This addresses the production/manufacturing activities of the business and includes labor management, materials allocation, and production capacity.
- Inventory Planning - These activities regulate optimal inventory levels based on sales needs and production capacity.
- Capacity Planning - These activities involve the allocation of equipment and employees to meet production demand.
- Distribution and Network Planning - This involves overseeing the transport of goods from supplier to manufacturer, and then to the point of sale. Common activities in distribution and network planning include warehousing, logistics, and packaging.
4. Sales and Operations Planning
Sales and operations planning is a recurring business process that covers a broad range of supply chain factors, including marketing, sales, demand forecasting, production, and inventory management, among others. The primary objective of most sales and operations planning sessions is to equip business leaders with the information to make decisions that determine how the business will be run.
Best Practices for Supply Chain Optimization
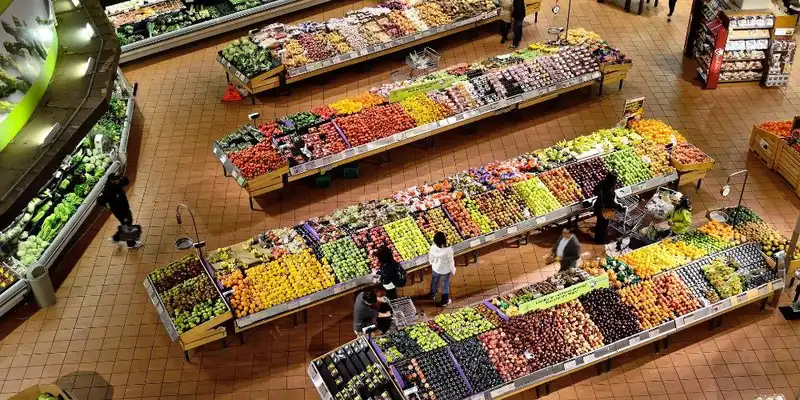
If supply chain management is the balancing act of keeping goods and services flowing throughout the supply chain network, then supply chain optimization has a much narrower focus.
Supply chain optimization involves a series of steps designed to reduce the costs of manufacturing, storing, and moving goods. In fact, businesses with optimized supply chains were revealed to have 15% lower supply chain costs and cash conversion cycles at least three times faster than companies with unoptimized supply chains.
Below are a few best practices for optimizing your supply chain.
- Use Technology to Streamline Processes - According to a Zurich report, organizations are increasingly using technology to improve the efficiency of their supply chains. By 2030, 59.6% of companies predict that big data analytics will be used widely in their organizations.
- Manage Supplier Relationships - Maintaining healthy long-term relationships with your suppliers allows for a free and constant exchange of feedback and information. Over time, these ideas can help create a more streamlined and effective supply chain that ensures the satisfaction of both parties.
- Think Total Costs - When choosing suppliers and deciding between offers, always think of the total cost of the procurement rather than the price in the purchase order. Remember that acquisition only makes up 25% to 40% of the total cost of ownership (TCO) of a product or system. The remaining percentage goes to warehousing, transportation, and operating costs.
- Choose Suppliers with Care - Expand your company's relationship with suppliers beyond the purchasing department. Nurture a collaborative relationship to get their feedback on how best to use their products or services to achieve your business goals.
- Put Contract Management Under the Supply Chain - While procurement agents will try their best to get the lowest possible price on supplies and services, further savings can be realized by moving contract management under the supply chain. This allows supply chain managers to leverage spend on areas where there are opportunities to reduce costs and manage risks with supplier services.
- Optimize Inventory - Inventory holding costs can eat up 60 percent of the cost of an item held in inventory for 12 months. To reduce surplus inventory, consider using forecasting and demand planning strategies to predict seasonal demand.
Now is the Time to Automate Supply Chain Management
Automation is poised to be the game-changer of supply chain management, and it's already here. In fact, 84% of respondents in the 2018 Supply Chain Management Priorities and Challenges survey believe that digitalization will have the most significant impact on the supply chain by 2021.
For example, supply chain software can keep an accurate record of orders businesses receive in real-time so they know how much inventory is available on hand. The software can also automatically alert supply chain managers when inventory is low or when there's a surplus of certain supplies, helping prevent stockouts and reduce inventory costs.
Automation through inventory ordering software eliminates the need for people to perform tedious and repetitive tasks manually, potentially saving thousands of worker hours in a year -hours that can be spent on strategic work that delivers more value to the business.