Stock Control Methods & Tips to Maximize Profits
Stock control is the practice of monitoring inventory levels and balancing the right amount of items to prevent overspending. This process includes all inventory items, ranging from raw materials to finished goods.
Effectively implementing a stock control system can help maximize productivity and profitability.
Methods for Stock Control Management
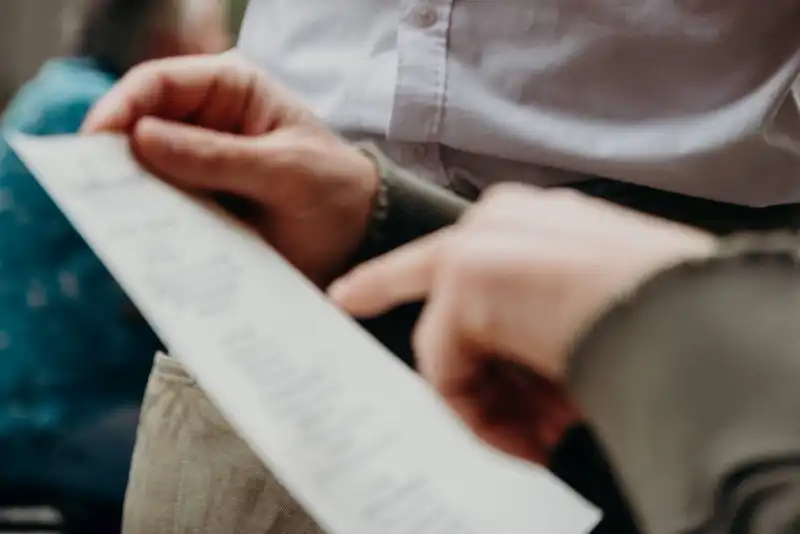
There are various methods for inventory control depending on variables such as average output and demand. Common techniques include-
- Stock Reviews
- Fixed-Time or Fixed-Level Ordering
Businesses that have a stable demand for their products or pre-established fulfillment contracts may prefer to use this stock control system because it ensures that the appropriate amount of stock is available at an expected time.
- Just in Time (JIT)
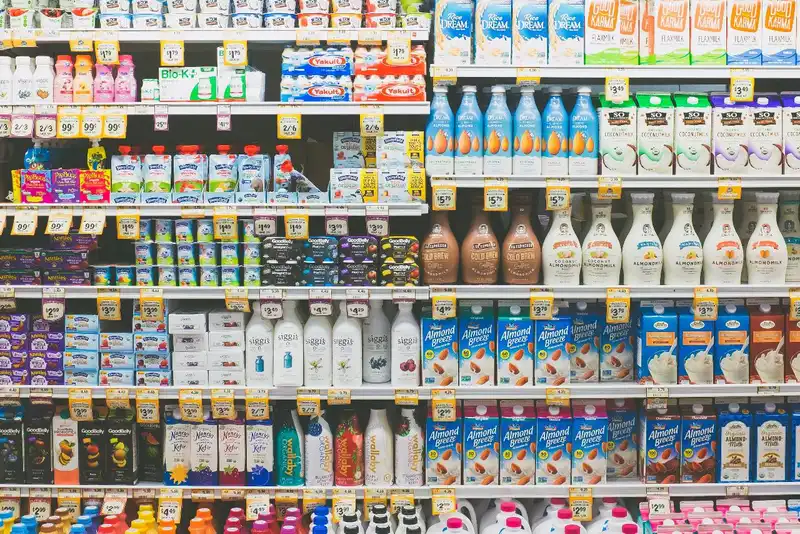
- Economic Order Quantity (EOQ) Formula
EOQ = Square root of ( ( 2 x Demand in Units x Order Cost ) / Holding costs ) )
It is recommended to use inventory management software because it can streamline and automate this calculation process. Software tools can determine optimal inventory levels by providing data-driven ordering suggestions in real-time.
- First In, First Out
- Batch Control
- Vendor-Managed Inventory (VMI)
Tips to Maximize Profits
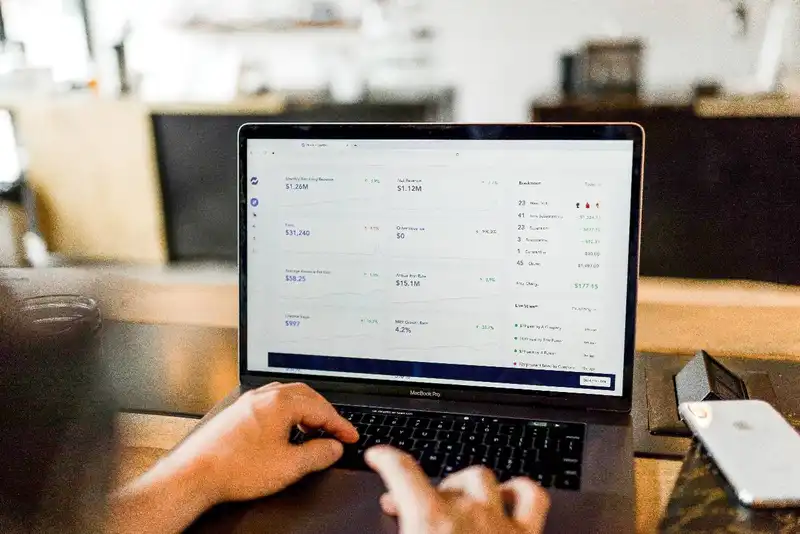
It is possible to properly manage inventory while preventing over and under spending by following these tips-
1. Define Processes and Types of Stock
It is important to outline production processes, different types of inventory items, and when they are used. The most common forms of stock include raw materials, unfinished products, finished goods, and consumables.
With this information, it will be easier to maintain the minimum stock levels at the right time. For instance, if the production process for a shipment of clothing takes one month and there is an order due in two months, the inventory of finished and unfinished clothes should be recorded.
If the quantity of finished clothes is low for the order, raw materials and consumables need to be checked and replenished to begin the production process. Doing this will ensure that only the necessary amount of goods is ordered, preventing overspending and waste.
2. Implement Inventory Management Software and Integrated Technology
An inventory management system makes controlling stock easier and more accessible. Users have more independence in managing their inventory supplies and will be provided with real time data concerning their inventory counts to make informed decisions about expenses and products.
Some of the best inventory control software has integrated technology that provides barcode scanning capabilities, mobile ordering, and POS system integration.
3. Track Sales
It is crucial to accumulate all revenue earned each day and record which products were purchased and the quantity that was sold.
These metrics should be analyzed with consideration of the shopping season. Additionally, determining the specific days that merchandise typically sells the most and other items that are bought with the product can help with analysis.
Utilizing sales data to review performance will make it easier to identify what items are selling faster than others and how to keep inventory at the optimal level to leverage sales.
4. Have Proper Stock Security
Inventory should be kept in a secure warehouse or storage facility where only authorized personnel can enter and handle stock items. Damaged or stolen products can quickly cause stock levels to drop and impact net profits due to products being unmarketable.
Not only should a security system be integrated into warehouse management, but personnel should also be thoroughly trained on how to protect the quality of items and identify suspicious activity. It is also beneficial to review how suppliers protect against theft or damages to their products.
By implementing stock control methods, organizations can effectively understand their customers' demands and make sure their inventory is at a level that can maximize profits and minimize expenses.