Returns Management- Definition & The 3 Pillars
Processing returns is more complex than simply shelving items back into their original locations for customers to purchase. Returns management is a comprehensive process that includes quality control and inventory tracking.
Implementing returns management will enhance warehouse inventory and supply chain administration, as well as optimize overall profitability by efficiently recovering the value of returned goods.
What is Returns Management?
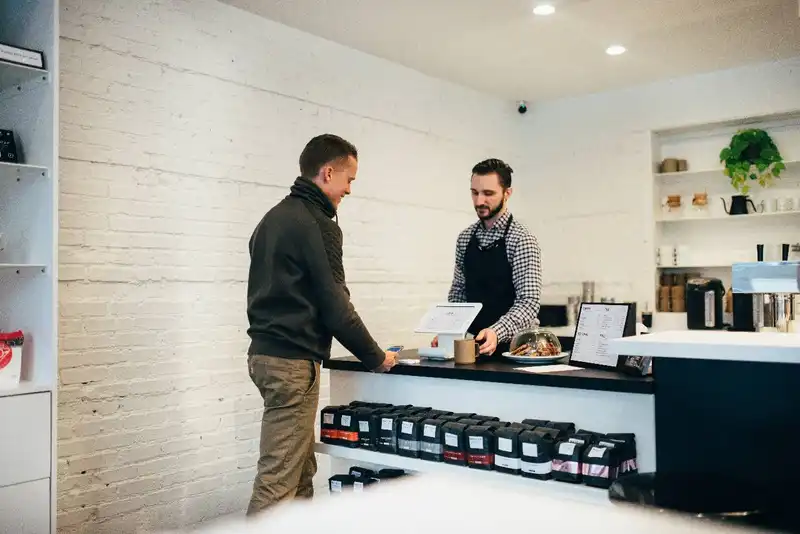
Returns management, also known as reverse logistics, is the process of overseeing products that are returned to an organization. Quality control is a key factor when dealing with returns, as defects in the item should be identified to enable adjustments in production processes, raw materials, or suppliers.
Returned products affect the supply chain by increasing holding costs as additional storage space and labor is required to store these items. Not only will returned goods take up space, but its value may also depreciate and its marketability will decrease.
It is necessary to implement an efficient returns management procedure to address these issues. This process can include creating strategies to quickly recover value from refunded products either through resale or secondary marketplaces.
In addition, reverse logistics will ensure compliance with waste management regulations. These are standards for the disposal or recycling of scrapped products. Complying with these rules will minimize fees associated with improper waste management.
Effective procedures will also allow organizations to provide better customer service, as consumers will have their returns processed quickly and replacements delivered promptly.
The 3 Pillars
A productive returns management system requires a thorough understanding of product information and its movement within the supply chain. There are 3 key elements that enable effective reverse logistics and by adhering to them, inbound returns can be processed swiftly.
1. Speed
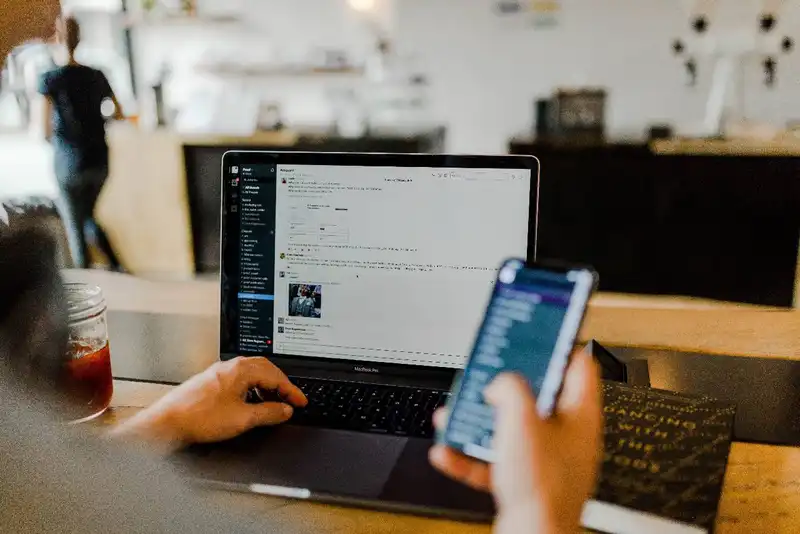
To ensure fast returns, businesses can automate return material authorizations (RMAs), which is the process of approving inbound items for refunds, exchanges, or repair. Some common tools that are used to speed up the returns procedures are-
- Workflow Automation
- Labels and Attachments
With inventory tracking software, labels and shipping documentation will be accurately printed and pre-addressed, allowing for real time shipment management. These tools ensure that labels are correct and compliant with carrier standards, effectively minimizing delays in delivery.
- User Profiles
Profiles within inventory management systems will simplify user maintenance using accessible interfaces. This enables management teams to track stock and waste, and hold employees accountable.
2. Visibility
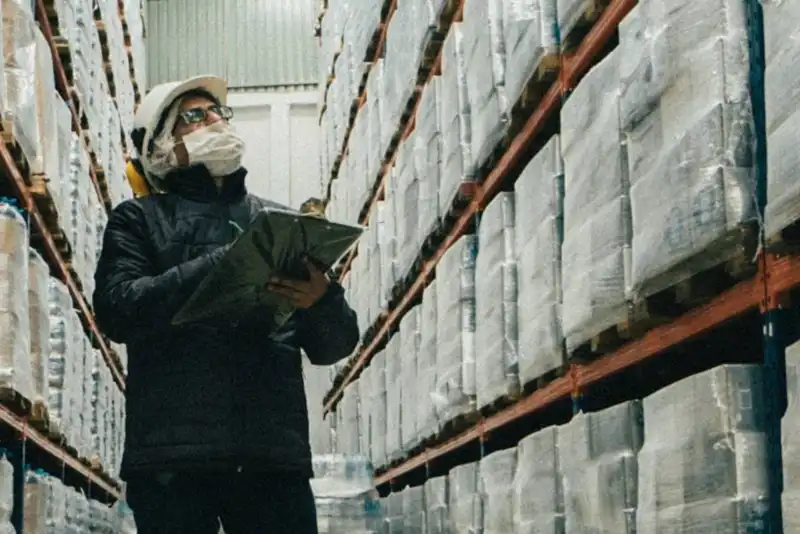
Product information should be obtained first before a return is received and processed by a company. The best ways to effectively and easily gather information include-
- Cloud-Based Portals
With online solutions, users from any time zone or location can log on and carry out the necessary actions. Integrating software systems, such as inventory management tools, will make it easier for users to access real-time data about products and expenses, which can be relayed between manufacturing facilities, different departments, and third-party entities.
- Carrier Integration
Connecting RMAs with carrier tracking information will clarify the movement of the shipment. This can be done through software programs that can send automated notifications regarding real-time delivery and reception updates.
- Barcode Identifiers
Integrating barcode identifiers will provide more visibility and accuracy into inbound shipment data. With a quick scan, information about raw materials, conditions, and current stock levels will appear, allowing shipment receivers to prepare staff and supplies.
3. Control
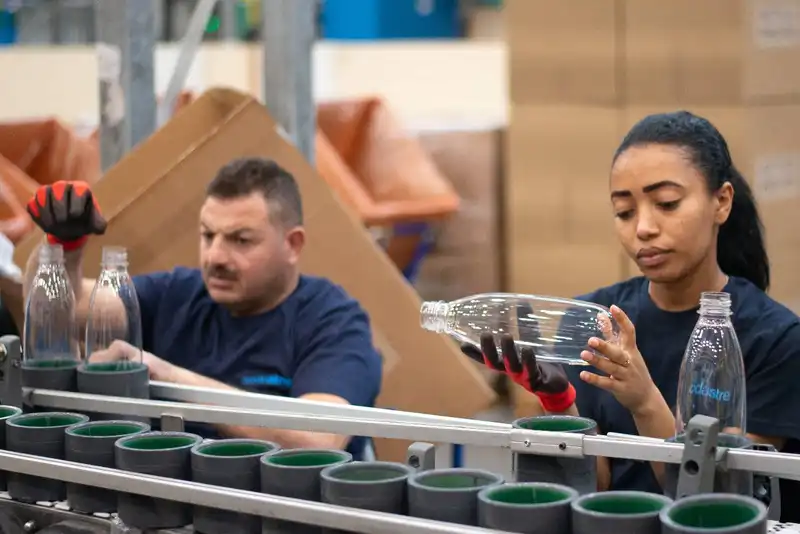
The flow of inbound and outbound movements within the supply chain can be difficult to manage. Therefore, businesses should proactively oversee the process by recording receipts and letting stakeholders know about discrepancies in product quality.
To enable more control of the supply chain process, management can also carry out product reconciliation, which refers to the process of updating stock levels and addressing errors.
Other procedures that can be implemented to provide better control within the returns management process include-
- Regulatory Compliance
By complying with national and local shipping regulations, corporate liability can be controlled and minimized. There are also standards for specific industries, such as food safety, that must be considered when managing returns. Compliance will ensure that products are properly shipped out and returned items are handled appropriately.
- Reconciliation and Final Disposition
Utilizing labels and data collection will make information about RMAs, shipments, and product values more accessible. This will streamline the inventory updating process.
- Quality Assurance
By conducting regular quality control checks, product issues can be identified before it negatively affects the brand image. In turn, adjustments to the production process can be made to minimize future instances of returns.
Distribution facilities should take extra precautions and ensure that products are labeled and shipped accurately. Having platforms that allow authorized entities to communicate and share data about the supply chain can also improve product quality.
Managing returns can be effective and proactive when using proper methods that ensure speed, visibility, and control. By quickly handling inbound returns and effectively recovering its value, organizations will be able to enhance their profitability, boost customer satisfaction, and minimize extra inventory costs.