Managing Supply Chain Disruptions- 6 Tips and What to Expect
Managing supply chain disruptions requires businesses to assess the potential threats in each phase of their operations and develop plans to mitigate these risks. A strategic emergency plan ensures that operations can continue amidst challenging times to maintain order fulfillment and healthy cash flow.
To minimize the damage of disruptions and limit exposure to risks, organizations must first identify the threats they are likely to face, then analyze the impact on the supply chain and the appropriate counteractions.
What is Supply Chain Disruption?
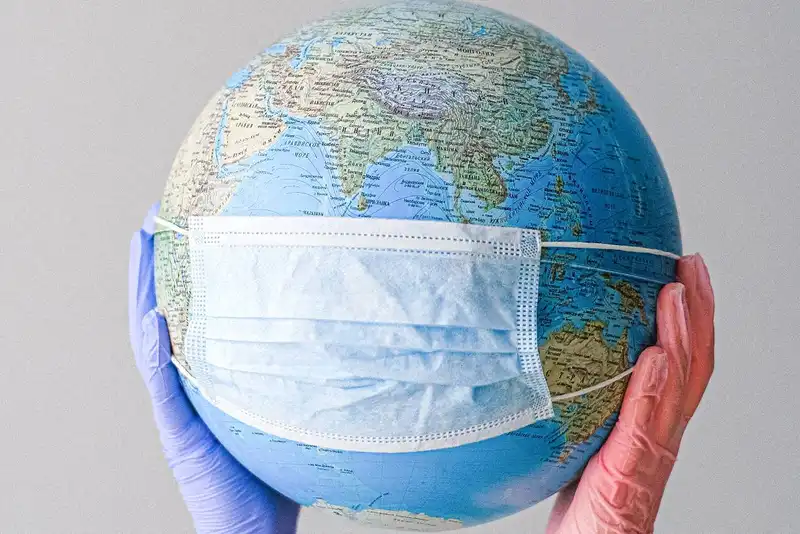
The supply chain is the network of businesses, operations, and employees necessary to transport a product from a vendor to a consumer. This includes every step from gathering the raw materials and manufacturing products to distributing the goods for final sale. While each step in the supply chain has its own duty, processes depend on each other. Therefore, if one operation experiences a delay, the following processes fall behind schedule as well.
A supply chain disruption refers to any event or sudden change that negatively impacts workflow, whether it occurs internally or externally. Disruptions can happen on a small or large scale, ranging from minor issues within a phase to complete shutdowns. The 6 most relevant types of supply chain disruptions include-
- Pandemics - This past year, supply chains have experienced the impact of the COVID-19 outbreak on the health of their employees and the supply chain. Some companies were forced to close, while others had to rebuild their business plans.
- Natural Disasters - Natural disasters, such as tornadoes and hurricanes, require companies to shut down during inclement weather to prevent extreme damage and injuries. For example, in 2011 an earthquake occurred off Japan's coast, triggering a tsunami, which demolished several businesses, including a nuclear power plant. This destruction stunted the local economy and supply chains.
- Transportation Delays - Increased trade has made international suppliers more common, increasing the focus on transport networks and shipment schedules. While shipping delays can occur even in ideal situations, clerical issues, natural disasters, and poor management can affect trade routes.
- Product Issues - A significant element to supply chain management is quality assurance. If there are issues in manufacturing certain parts, the final product can be delayed or faulty. As no business wants to send sub-standard products to consumers, the following supply chain stages would be stalled to create better quality products.
- Price Changes - As suppliers fluctuate their prices, businesses must consider whether to find alternate vendors with lower rates. This requires additional research, putting the supply chain in a holding pattern until a final decision is made.
- Security Breaches - When organizations do not adequately protect themselves, they are exposed to various security breaches, especially cyber-attacks. If a phase does not have a firewall implemented, hackers can access sensitive data.
6 Tips to Prepare for Supply Chain Disruptions
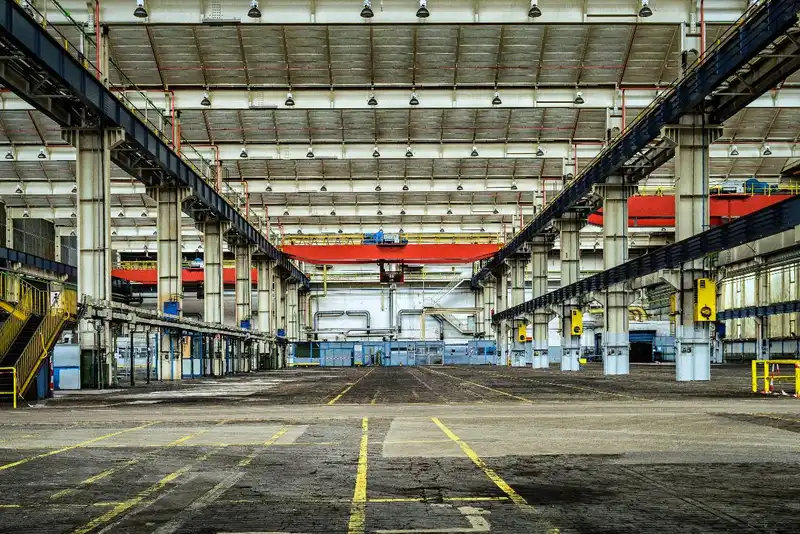
Managing supply chain disruptions is essential for keeping processes and all involved parties on schedule. Therefore, companies should take a proactive approach to operations management to mitigate risks and ensure continuity.
There are various supply chain management tips that businesses can employ, including-
1. Develop a Supply Chain Emergency Plan
Businesses should have a contingency plan in place for every phase to ensure operations can continue without delay. When developing an emergency plan, management should consider building an additional budget and establish alternative storage locations for products.
2. Stockpile Inventory
Setting aside extra inventory ensures companies can continue operations for several months, even during unexpected events. This could entail storing raw materials, components, or finalized goods in separate locations in case of demand surges or product shortages.
3. Assess Supply Chain Vulnerability
Management needs to designate time to assess risks in the supply chain and determine vulnerable phases. Risks could include potential political, economic, and environmental threats, such as new regulations that may affect how operations are conducted. This allows organizations to find alternative methods ahead of time to avoid delays.
4. Line up Alternative Vendors
Businesses should never rely on just one vendor, as any of their disruptions could negatively affect the company's entire supply chain. Therefore, organizations should find local backup suppliers to step in during emergencies.
5. Diversify Supply Base
Companies should also identify suppliers in different locations to expand their supply base and avoid disruptions. By establishing relationships with vendors outside of the local economy, businesses can ensure they have access to essential goods if suppliers fall through due to local disruptions.
6. Implement Risk Evaluation Tools
Modern supply chain technology enables companies to evaluate and mitigate emerging risks. Advanced analytics automatically monitor trends and alert users of unusual activity, allowing management to respond quickly. Software tools can also detect environmental, geopolitical, and cyber threats.
The Future of Supply Chain Technology
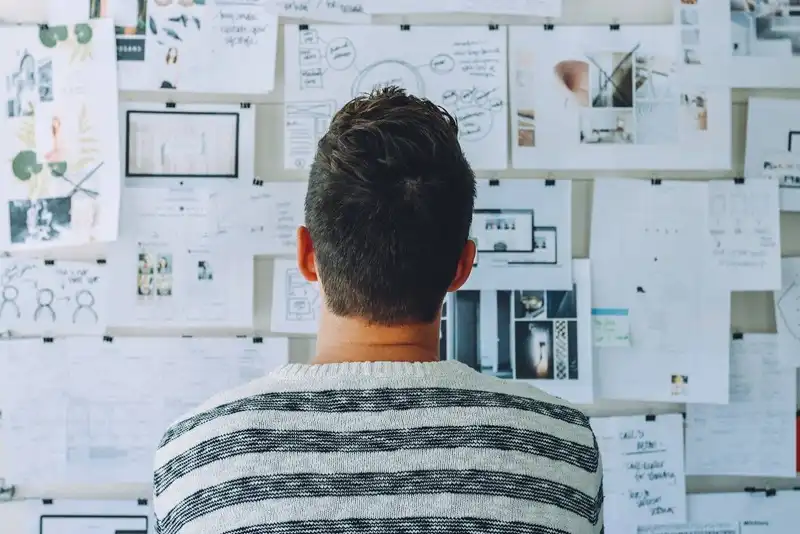
New technology has made it simple to streamline supply chain operations, reduce inventory expenses, and improve the visibility of each phase. By integrating inventory, replenishing, and forecasting software, businesses can automate analytics and standard stock procedures.
Companies can program ordering solutions to trigger reorder points when metrics show depleted stock, avoiding potential stockouts. These features also optimize inventory levels by monitoring the company budget and reducing unnecessary expenses such as holding and shipping costs.
Advanced ordering systems also show local vendors, catalogs, and alert management whenever prices change, allowing them to find new suppliers. Forecasting solutions can consider these insights when tracking trends and monitoring upcoming fluctuations in customer demand, so management can determine how to change optimal stock levels.
With proper supply chain management techniques, coupled with advanced technology, businesses can limit their exposure to damaging risks that can disrupt processes. While not all threats can be mitigated, preparing for emergency situations ensures companies can remain in business during adverse conditions.