Complete Guide to Supply Chain Risk Management Strategies
Introduction to Supply Chain Risk Management
When operations within the supply chain face disruptions, dependent processes are delayed. This causes a domino effect that can negatively impact efficiency and profits due to lost opportunities and sales.
However, by mitigating internal and external risks, businesses can reduce the impact hazards have on their supply chain. This ensures procedures can always run according to schedule.
With strategic supply chain risk management guidelines, retailers can anticipate financial, environmental, geographical, and business threats that could jeopardize their longevity. Therefore, organizations should continuously identify potential threats, update responses, and develop plans to prevent damages.
Types of Supply Chain Risks
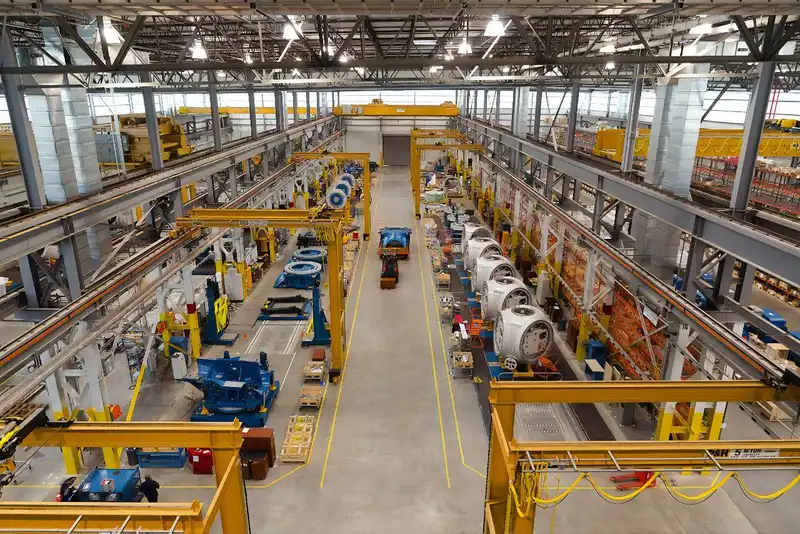
The supply chain is exposed to numerous types of risks as it performs a wide variety of processes. These threats can potentially delay systems and create additional expenses for the businesses involved. The main types of risks companies may face include-
Internal Risks
The internal risks of the supply chain refer to the issues that are under a business's control and, therefore, can be anticipated and mitigated. Companies can monitor possible risks through software and analytics that generate trends and insights, such as key performance indicators (KPIs). The various types of internal threats are-
- Manufacturing - Manufacturing risks refer to the likelihood of a crucial element or procedure being disrupted, delaying the production schedule.
- Business - Internal business risks are a result of errors that occur within the supply chain management, reporting, or other processes.
- Planning - Planning risks are a product of inaccurate predictions, estimates, and poor control strategies.
- Contingency - Contingency risks occur if a company does not have a proper contingency plan to mitigate possible issues throughout the supply chain.
External Risks
The global supply chain involves several external organizations and vendors, which can present new opportunities for disruptions. This makes it challenging to anticipate and prepare resources to mitigate possible hazards. The most significant external supply chain risks include-
- Demand - Demand risks refer to miscalculating the rate of demand due to the lack of insight or inaccurate historical purchase trends. This can lead to under or overstocking products, which can negatively impact profits and expenses.
- Supply - Supply risks occur when the delivery of vital raw materials is delayed or canceled, halting the proceeding production process. This consequently slows the following supply chain operations, such as order fulfillment and distribution.
- Environment - Environmental risks that affect the supply chain are often caused by socioeconomic, political, governmental, or weather issues. This can include inclement weather that requires freight shipping to wait days until climates are safe enough to resume deliveries.
- Business - Business risks include any unexpected alterations made by a dependent third-party that requires the supply chain to stall until further clarification. This can occur when a vendor company is sold and under new management.
Types of Supply Chain Risk Management Strategies
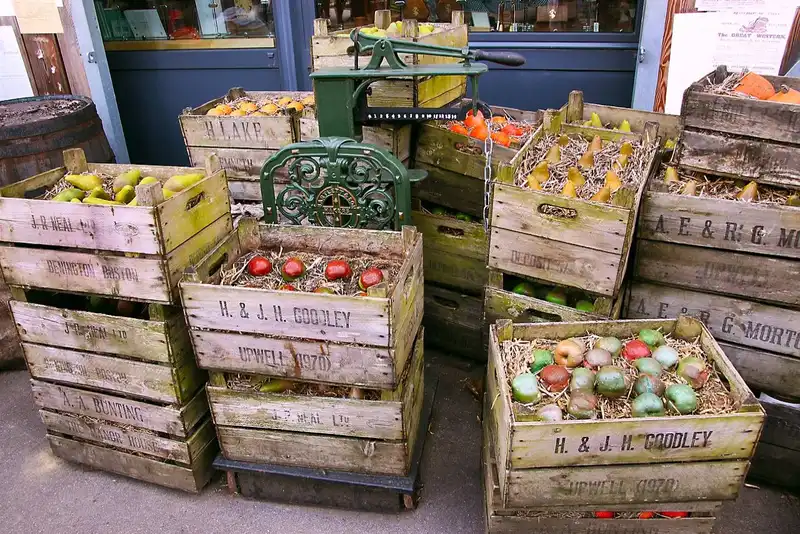
Once businesses are aware of the different supply chain risks, it is time to implement an effective risk management strategy. There are several approaches companies can take, such as-
1. PPRR Risk Management Model
Global supply chains, especially retailers, typically use the PPRR strategy. PPRR stands for-
- Prevention - Implement precautionary measures to mitigate supply chain risks.
- Preparedness - Create and regulate a contingency plan for dire situations.
- Response - Use the contingency response to counteract risks and minimize its impact on the supply chain.
- Recovery - Once processes are analyzed and recovered, operations can resume to routine procedures.
2. Manage Environmental Risks
Now more than ever, businesses need to understand how to manage environmental risks. Retailers around the world have been preparing and recovering their supply chain operations from the effects of the COVID-19 pandemic. With a disrupted supply chain, businesses struggled to fulfill contracts, keep operations running, and launch shipments on time.
This emergency has caused many organizations to switch from single sourcing to multi-sourcing, as an effort to mitigate the risks of losing a supplier. Other organizations have decided to rework their business models to adapt to new customer demands. For example, American breweries started producing hand sanitizer as a response to the major stockouts.
While it is not possible to completely eliminate environmental risks, businesses can develop response plans to prepare for different scenarios. With software and analytics, companies can better understand their supply chain's strengths and weaknesses. This allows management to create an effective contingency plan for each process in the chain.
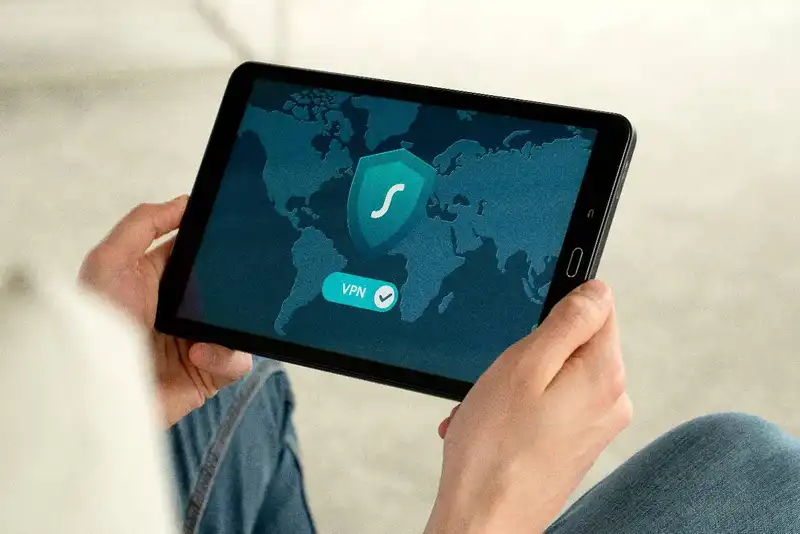
3. Mitigate Cyber Supply Chain Risks
Software and other digital technologies that use the internet to streamline supply chain processes can be useful. However, they also introduce cyber threats, such as viruses, hackers, phishing, and malware. These risks can expose sensitive information on clients, vendors, and funds. Therefore, businesses should implement robust cybersecurity defenses, such as-
- Standardize compliance rules for all external parties, including manufacturers, vendors, and distributors.
- Implement security measures to authorize only certain users, restricting access to classified information.
- Perform a risk assessment on suppliers before finalizing contracts.
- Assign ownership to each dataset to clearly define what party can access the information.
- Train all employees on cybersecurity protocols.
- Implement software that monitors every supply chain process and alerts users of unusual activity and metrics.
- Partner with suppliers to create a disaster recovery plan.
- Implement backup hard drives to store separate copies of data in case of a malfunction or security breach.
- Regularly update the software's firewall, anti-virus, and anti-spyware processes to ensure digital fronts are safe.
4. Analyze Suppliers' Financial Stability
Before an organization commits to a supplier relationship, they should first use a credit rating agency to generate predictive stability reports based on the potential vendor's financial reputation.
The analysis will use the supplier's financial history to estimate the risks they introduce to the company. This ensures that businesses are building secure partnerships while reducing supply chain vulnerability.
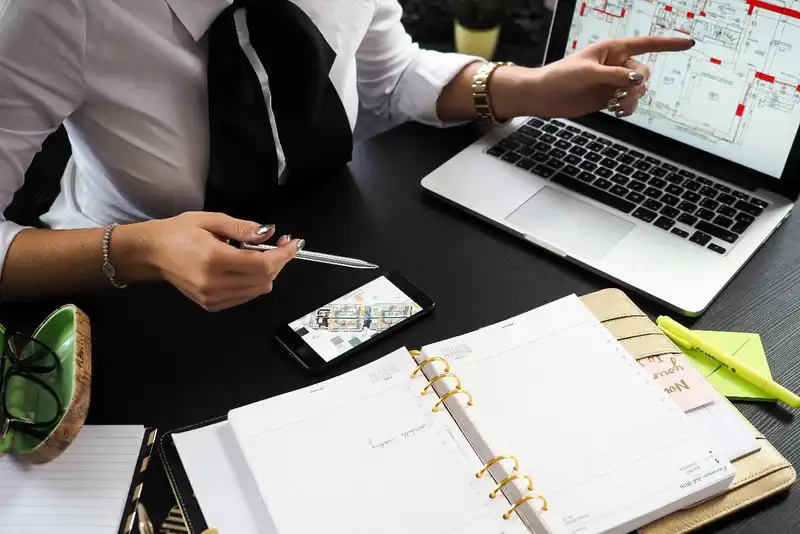
5. Monitor Freight Carrier Metrics
Retailers must ensure that their product shipments arrive on time to meet deadlines and keep the remaining supply chain processes on schedule. Just one late delivery can delay hundreds of order shipments.
By partnering with freight carriers that offer real-time metrics and tracking, companies can continuously monitor deliveries. Management should assess new and existing carriers by using key metrics-
- Transit Time - This metric is the number of hours or days a shipment takes to reach the customer.
- Number of Stops & Stop Time - Carriers have to stop to rest and eat, and every stop in a delivery route elongates the transit time. Adding just one additional stop can result in late delivery and unsatisfied customers. Therefore, knowing the average stops and stop time allows companies to calculate when a shipment will arrive.
- Loading Time - The average loading time is the time it takes to load a carrier and fill out documentation once it arrives at the dock.
- Route Optimization - Companies should understand how their carriers optimize their route to conserve fuel and reduce travel time. These metrics determine expenses and arrival time, directly affecting supply chain efficiency.
- Maintenance Routine - Freight carriers should maintain a routine maintenance schedule to prevent breakdowns and delayed deliveries.
6. Implement a Comprehensive Logistic Plan
Retailers need to develop a logistics contingency plan to ensure that operations can continue seamlessly if there is an unexpected disruption in the supply chain. Management should consider several elements during the planning phase, including-
- Outline supply chain processes to identify which operations are the most vulnerable.
- Assess suppliers and third parties to determine political, geographic, and economic risks.
- Expand the supplier network to introduce alternatives.
- Audit providers through assessing their disaster plans.
- Develop a response team to make final decisions in the event of a crisis.
- Establish dependable communication lines between employees and partners to ensure every party understands their responsibilities.
- Document all operations and establish a universal platform that all employees can access for reference.
- Adapt contingency plans according to updates and current events.
- Create backups plans.
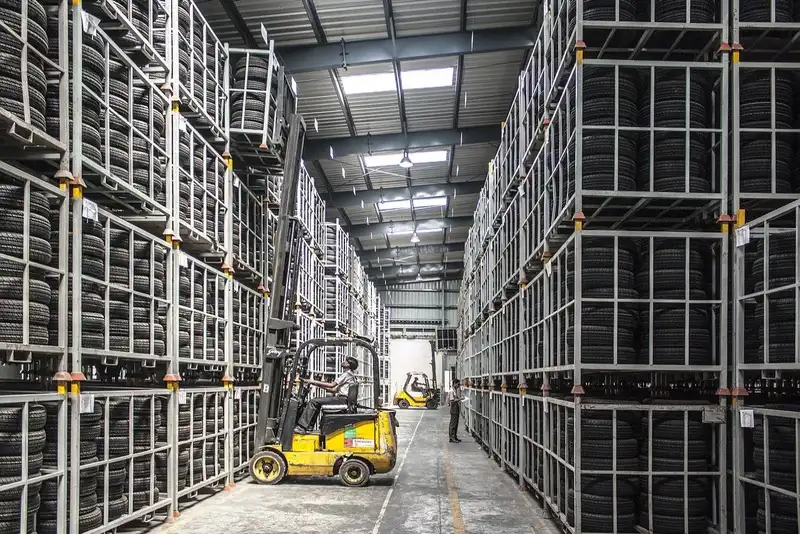
7. Train Employees to Anticipate Risks
Management should not be the only group of staff that can identify and prepare for risks. Companies should hold training sessions for employees that teach them how to define and anticipate hazards in the workplace. Risk awareness curriculum should include-
- Common internal and external supply chain risks
- The best risk management practices
- Software best practices to improve cybersecurity
- How to assess the supply chain
8. Continuously Monitor Risks
Once the supply chain management strategy has been implemented, management must continue to monitor operations to ensure its long-term effectiveness. Often, companies forget this remaining step, leaving errors and discrepancies unnoticed.
By carefully tracking each step of the supply chain, businesses can detect and immediately respond to potential risks. With advanced software, these processes are automated, generating updated reports and insights.
9. Model Data to Define Risks Scenarios
By equipping the supply chain with predictive analytics and data modeling, businesses can forecast potential risks. With big data, the software pulls internal and external information on each process to model different scenarios and suggest ways for the company to respond.
This allows management to develop contingency plans in advance to anticipate the worst-case scenario.
Steps for Managing Known Supply Chain Risks
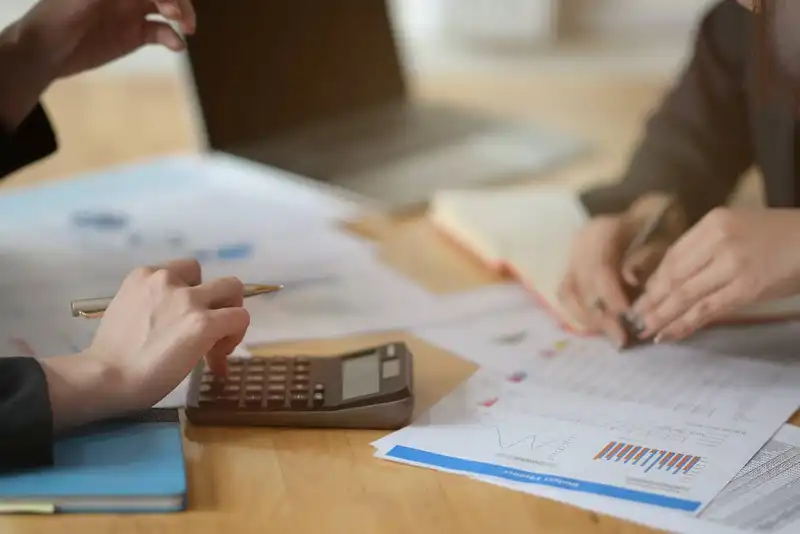
With access to historical and real-time data, retailers can measure and anticipate known risks within their supply chains. Known risks are related to internal operations, in which the business can control.
For example, the risk of a supplier losing funding can be assessed and managed by evaluating historical and current financial stability to project the likelihood of bankruptcy.
Companies can follow four steps to structure a known risk management strategy-
1. Identify and Report Risks
Management must first identify and define the risks present at each level of the supply chain. This outline should include each participant, from the suppliers to the carriers. Then the threats should be documented for future reference.
2. Develop a Supply Chain Risk Management Plan
Outlined risks should then be ranked according to three factors - impact on the organization, likelihood of occurrence, and the company's preparedness. Based on this rubric, management can score each risk and set a tolerance threshold representing the business's vulnerability and ability to handle each hazard.
3. Monitor Risks
After the risk management plan is complete, designated employees should closely monitor processes to pinpoint risks and assess their damage. Successful tracking allows staff to respond promptly and reconcile any issues caused by the threat to ensure the supply chain can continue to operate.
4. Perform Regular Reviews
Finally, organizations should develop a governance procedure where managers assess the risks that are reported and determine better ways to identify and anticipate them.
Typically, an additional board of experts can help managers adapt their risk management plans by using metrics to improve response time and reduce the level of damage. By continuously updating strategies, businesses can efficiently counteract evolving threats.
How to Manage Unknown Supply Chain Risks
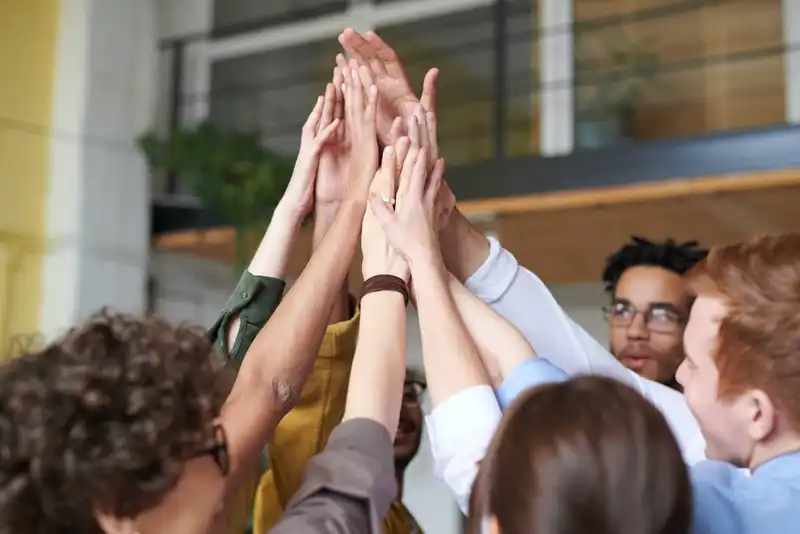
Unknown risks are more difficult to manage, as businesses cannot predict or prepare for them. However, companies can build strong defenses and foster a risk-aware work environment to limit their exposure to unwanted disruptions.
1. Build a Robust Defense
From employee training to implementing firewalls, businesses can create a proactive risk management approach to counteract emerging threats and avoid supply chain repercussions. With each risk encounter, management should evaluate how well the strategy fended off damage, its weaknesses, and how to build a better defense mechanism.
2. Create a Risk-Aware Work Environment
Companies should foster risk-awareness in their work environments to maintain durable defense layers. Businesses can do this by focusing on-
- Awareness - Management is responsible for identifying past mistakes and new approaches to better manage risk in the future. By acknowledging shortcomings instead of passing the blame onto different parties, members of an organization can work in unison to improve operations.
- Response Time - Taking the time to train employees equips staff members with the skills to quickly react to emerging risks and take ownership of outcomes.
- Transparency - Managers should thoroughly outline the company's risk tolerance so employees understand exactly when to request help. Excessive risks can require significant expenses to reconcile damages. Therefore, it is vital to minimize risk exposure.
Supply chain risk management is an essential tool that organizations should use to minimize their exposure and vulnerability to risks. By successfully implementing a defense strategy, businesses can ensure their processes are able to continue through interruptions without sacrificing operational efficiency.