5 Key Tips for Warehouse Optimization
Prioritizing warehouse optimization is essential to supply chain efficiency. With productive methods, companies can complete order fulfillment promptly and minimize operational costs.
Not only does warehouse optimization assist with the business's financial growth, but it will also help managers to effectively organize the facility's space to keep their employees safe.
What is Warehouse Optimization?
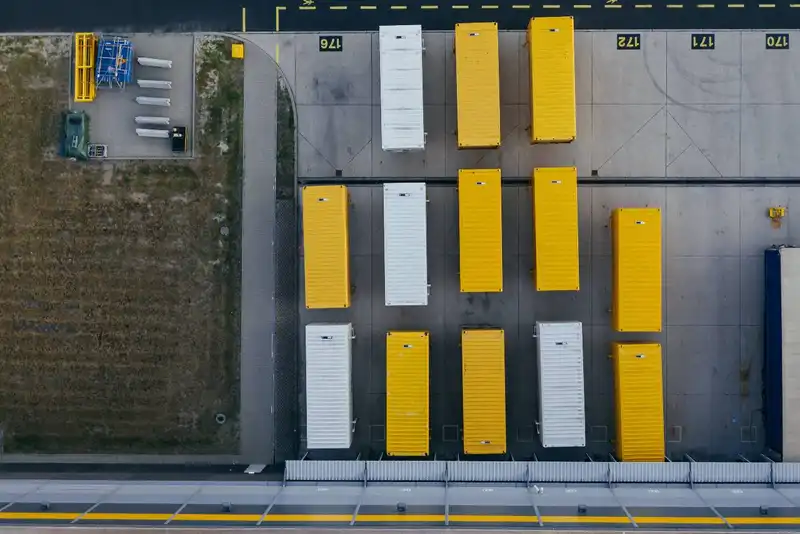
Warehouse optimization is the system of carefully organizing the use of space, resources, and time to improve the efficiency of the warehouse. This process also includes the use of automation and comprehensive planning to optimize internal procedures such as workflow, customer service, and warehouse storage.
Automation is a popular method of optimization among warehouses. The 2 types that management commonly uses are process automation and physical automation. The former typically refers to software and the use of data collection and analysis. This is helpful for assessing inventory and maintaining optimal levels of stock. Physical automation is the use of tangible tools, such as using drones to move goods.
Incorporating optimization methods that best align with the company will provide many benefits, such as-
- Minimized Workload - Automation helps streamlines laborious processes, therefore, reducing employee workload and fatigue. Managers will also be less likely to have to pay staff overtime since tasks can be done easily or quickly.
- Accurate Forecasting - Warehouses managers that use inventory management software can access data that enables them to accurately forecast their sales and demand. This helps managers make better buying decisions that target their customer's needs.
- Better Customer Service - Since warehouse optimization ensures that inventory is kept at opportune levels, a company can promptly fulfill orders and provide positive customer service.
5 Best Practices for Optimizing the Warehouse
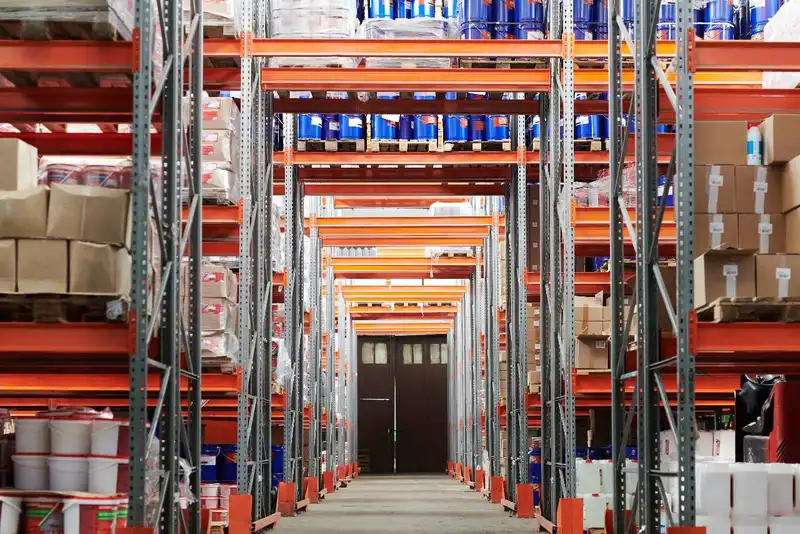
Businesses that want to improve their warehouse operation or implement new optimization strategies can incorporate these best practices.
1. Identify Product Velocity
Product velocity is the rate at which inventory items sell in a given period. Every company has certain products that have more demand and move through the supply chain quicker than others. Therefore, managers need to monitor the velocity of their inventory closely and identify their most popular products.
Management should then organize their warehouse and place their highly demanded products in areas where they are accessible for staff members.
For example, these items can be placed on lower shelves or at a storage space closer to the packing area to minimize travel time within the warehouse. This makes it easier for staff to pack orders and prevents delays to the operation.
2. Minimize Errors
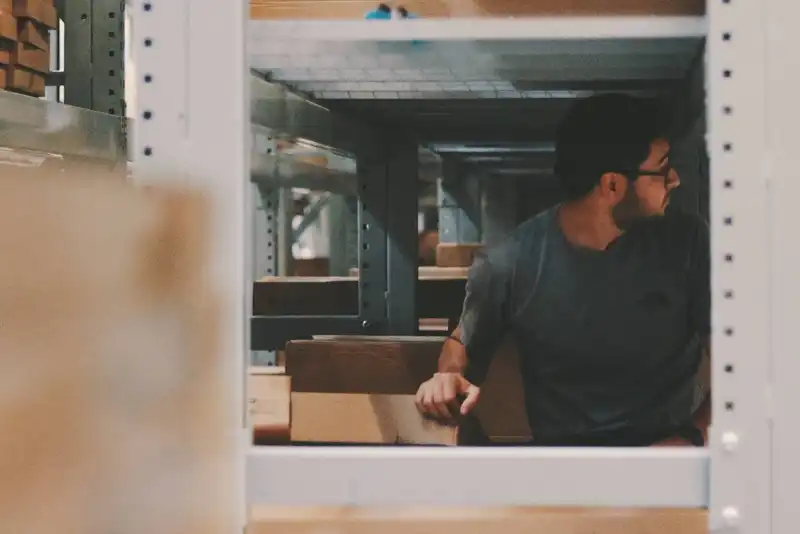
Human errors can oftentimes cause warehouse productivity to decrease. Businesses can safeguard their efficiency by automating repetitive or laborious processes. Warehouse managers, for instance, can integrate an inventory management system that optimizes ordering.
This feature provides suggested ordering, essentially eliminating errors in the purchase order process and preventing chances of over-ordering.
3. Implement Inventory Management Software
By implementing inventory management software, warehouse staff can spend more of their time on other tasks, such as packaging, labeling, and fulfilling customer orders, rather than conduct repetitive inventory counts.
With cloud-based inventory management solutions, warehouse management can simplify inventory tracking, as well as gain visibility into their spending.
The software also provides real-time data reports regarding the waste, costs of goods, profitability, and inventory levels. These insights allow managers to optimize warehouse operations and make data-driven decisions. Many systems have features that streamline the ordering process to ensure optimal levels of inventory are maintained.
4. Automate Shipping
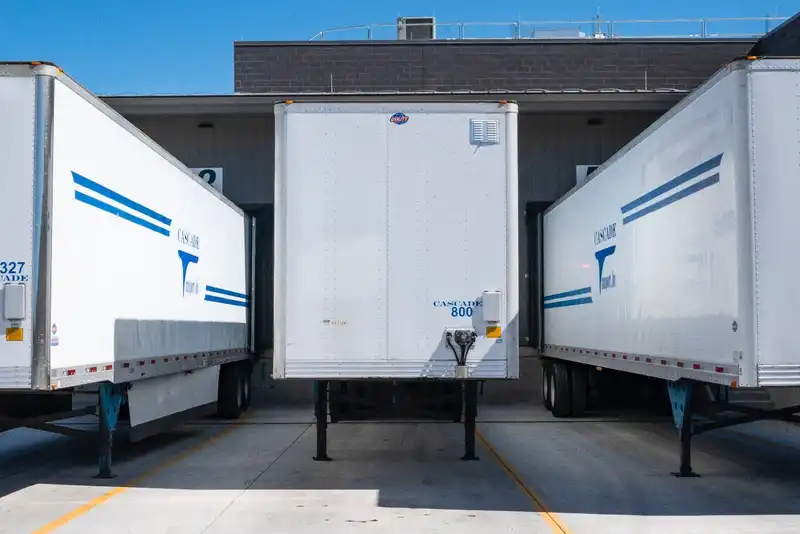
For the fulfillment process to be successful, packages must be delivered to the correct destination.
Companies can ensure their goods are properly shipped by using order routing automation. This will prevent any human errors, such as mislabeling or misspelling addresses.
Automating shipping helps businesses guarantee their products reach their customers and that satisfaction is maintained.
5. Use Robotic Technology
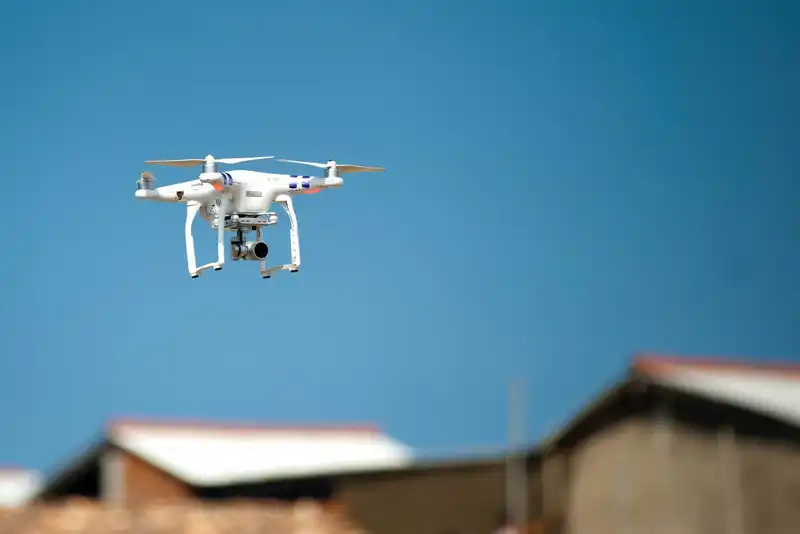
Companies that use robotic technology in their warehouses have been able to cut expenses and boost their workflow efficiency. While these tangible tools used to be limited to human-controlled robots that can move or carry heavy products, modern technology has upgraded these machines.
The latest robotic technologies warehouses often use are-
- Automatic Guided Vehicle - A portable robot that can transport large volumes of items. They can move throughout the warehouse space without the need of an operator or driver.
- Autonomous Robots - These are used to enhance the speed and accuracy of routine warehouse procedures. Managers often use these machines to move inventory around the facility.
- Drones - Management can fly a drone in their warehouse to conduct inventory counts. These small aircraft systems can also pick up items from shelves and place them into delivery boxes.
- Automated Storage and Retrieval Systems - These robotic systems can retrieve inventory items and store them in their respective locations.
Warehouse optimization practices are key to streamlining internal operations, such as order fulfillment and supply chain management. By integrating these tips into a warehouse strategy, business owners can improve efficiency and productivity.