Supply Chain Optimization - Techniques and Best Practices to Know
As global supply chains continue to undergo changes, it has never been more important to take the necessary steps to ensure that supply chain processes and activities are as efficient as possible. While the old metrics of productivity, service, and quality still apply, the rise of digital transformation adds a new dimension to supply chain optimization.
According to researchers, a third of all manufacturing supply chains will use analytics-driven cognitive functions by the end of 2020. These developments are expected to increase cost efficiency by 10% and service performance by 5%.
However, to effectively use transformative technologies, managers first need to understand supply chain optimization.
What Is Supply Chain Optimization?
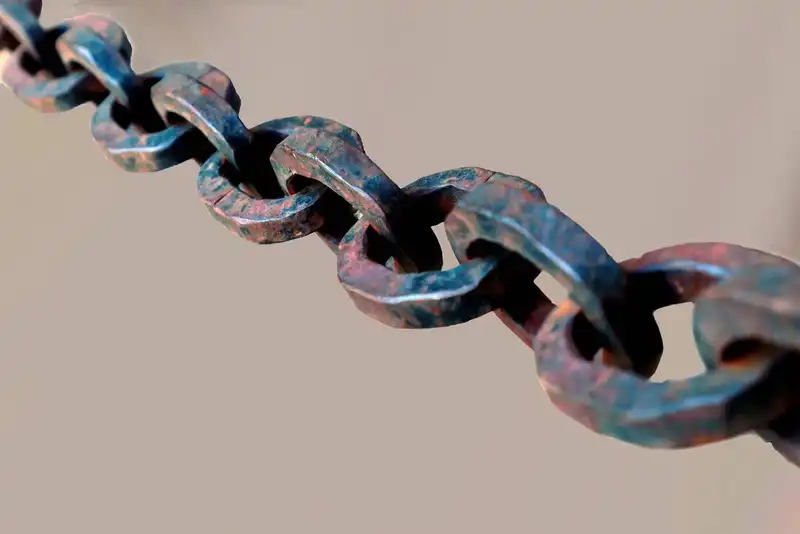
Supply chain optimization is the process of maximizing the use of emerging technologies such as artificial intelligence (AI), machine learning, the Internet of Things (IoT), and blockchain to improve the efficiency of a supply chain network.
For organizations that manufacture and sell products, the supply chain is a critical business process that ensures customers get the products they want, when and where they want them. While a high-performing supply chain is essential to creating positive customer experiences, it also ensures the organization's profitability and sustainability of its supply chain processes.
While there are different methodologies regarding supply chain optimization, most approaches will involve the following steps-
- Design - This step describes the supply network's design, such as the layout of warehouse facilities and the flow of manufacturing processes between these facilities. The design process also touches on strategic objectives, such as establishing connections with suppliers, demand planning, and planning of production operations.
- Planning - Planning includes creating a comprehensive supply chain plan, inventory planning, and the careful coordination of supply network assets to optimize the delivery of raw materials from suppliers and finished goods to customers.
- Execution - The final step is focused on functions and systems that involve the execution of supply chain processes, such as warehouse, inventory, and transportation management among others.
Issues Addressed by Supply Chain Optimization
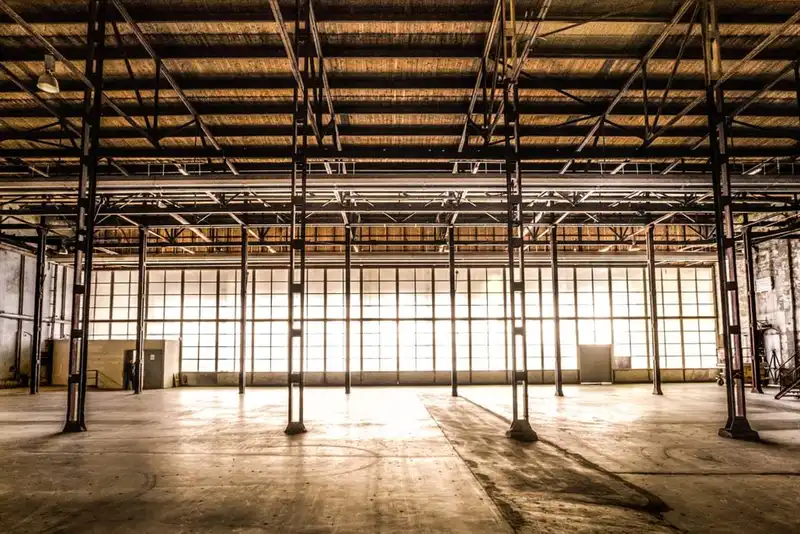
By leveraging AI, IoT, and blockchain technology, managers can optimize their supply chains and address these common issues.
Data Silos
Many companies often have inefficient supply chains because data isn't shared between different teams and departments, such as logistics, procurement, inventory control, and quality management.
With a cloud-based supply chain management platform, teams have end-to-end visibility of their data, resulting in better cooperation.
Evolving Customer Needs
Rising customer expectations are encouraging companies to optimize their supply chains to keep up with demands for better product quality and faster service.
For instance, optimizing the supply chain makes it possible for organizations to provide same-day or next-day delivery.
Gaining a Competitive Edge
Supply chain optimization can be an organization's best tool for creating a competitive edge over other companies. The right technology can enable decision-making based on real-time data and make execution-oriented processes more efficient.
Agile Operations
Access to real-time supply chain data allows an organization to quickly respond and adapt to changes, whether it's customer expectations, a competitor's sales and marketing promotions, or supply disruptions.
Sustainability
Research shows the typical company's supply chain has an enormous impact on the environment, accounting for over 80% of greenhouse-gas emissions and over 90% of the impact on natural resources.
Optimizing the supply chain allows companies to partner with sustainable suppliers and reduce or eliminate wasteful activity from their processes.
Methods for Optimizing a Supply Chain
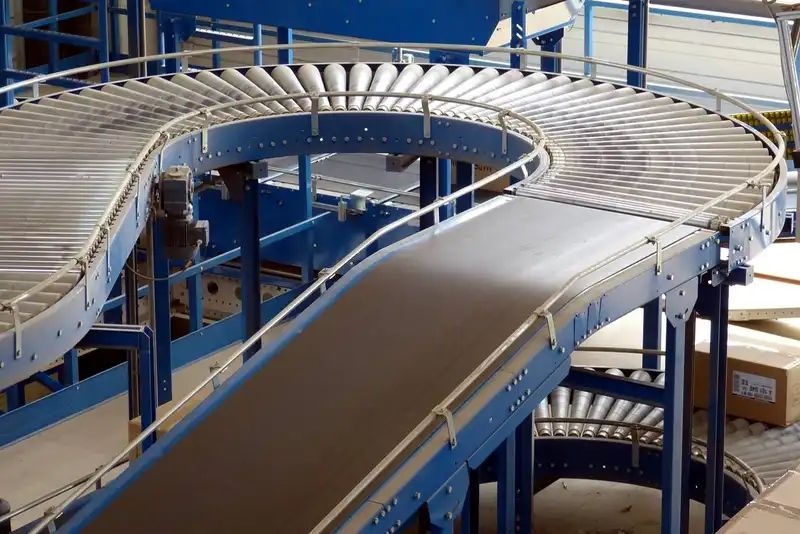
The different approaches to supply chain optimization typically fall under these broad levels-
Strategic Planning
Processes that fall under this category are focused on defining the overall approach towards supply chain optimization. This is also where goals for inventory management, manufacturing, transportation, and distribution are set and aligned with the ideal technology.
A strategic supply chain plan should include demand forecasting to efficiently allocate the proper resources across the supply chain network.
Tactical Planning
While tactical plans tend to focus on short-term goals, they should also cover at least a year's worth of activities to support the supply chain's long-term strategy.
A tactical plan will generally cover capital requirements (e.g., warehouse facility and space), specific skills for staff, and timing for each step of the supply chain.
Operational Planning
This level addresses the granular processes and activities that are necessary for the supply chain to function efficiently.
The operational plan illustrates how to allocate resources and measure supply chain performance to create a system of reviewing and improving the supply chain's efficiency. Depending on the supply chain activity, operational planning can focus on daily, weekly, or monthly activities.
Contingency Planning
This level plans for worst-case scenarios and disruptions, such as calamities, labor issues, accidents, and major problems with suppliers.
This allows the organization to figure out in advance what its response will be to different disruptive events. Contingency planning also looks at how to minimize the impact of disruption and resume normal operations in as little time as possible.
Supply Chain Optimization Best Practices
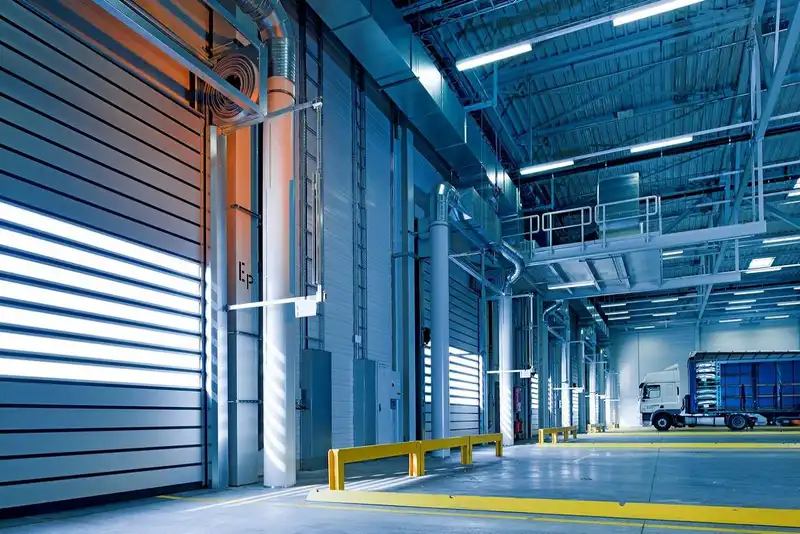
To effectively optimize their supply chains, decision-makers across all points of the supply chain network must spend a significant amount of time on planning and process management.
Below are the 10 best practices typically used by manufacturers to improve the efficiency of their supply chains.
1. Create a Supply Chain Council
Creating an internal group of leaders makes it easier to create a clear and cohesive optimization strategy. Involving decision-makers from other departments also ensures that the supply chain strategy aligns with the organization's short-term and long-term business goals.
For example, if a manufacturer's goal is to reduce inventory holding costs, it makes sense for procurement teams not to purchase a container of material that ends up being stored for 12 months.
In other words, a council of supply chain leaders from different management levels and departments prevents data silos and improves cross-functional communication.
2. Establish a Supply Chain Structure
An efficient supply chain is anchored on a structure that's tailored to the company's specific needs. Ideally, each step of the supply chain network should be staffed sufficiently to bring the most benefit to the organization.
However, there are no hard and fast rules for creating or implementing a supply chain structure. For example, many organizations use a centralized strategy implemented by managers from different business units. This approach offers the benefit of integrating strategic planning and implementation, resulting in more efficient processes.
When it comes to staffing, managers should also think of the strategic impact of having people with strong interpersonal skills, such as relationship management and communication, both within and outside of the company.
3. Leverage Technology to Streamline Processes
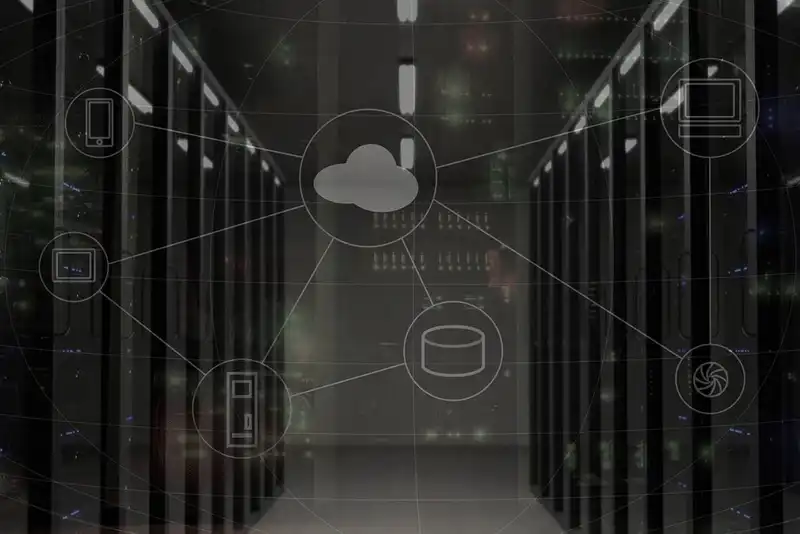
Research shows that around 79% of enterprises cite manual processes as the driving factor behind their lack of supply chain visibility. This problem, along with poor coordination between supply chain processes, can be fixed with supply chain management software with automation features.
These platforms eliminate the need for people to work on routine and repetitive tasks that not only require significant amounts of time but are also prone to human error.
However, despite its ability to optimize processes, technology should not be the guiding force of a supply chain's structure. Instead, managers should review processes that are performing below standards and then figure out how technology can make things better.
4. Manage Relationships with Suppliers
The health of a company's relationships with its suppliers is a crucial key performance indicator (KPI) of its supply chain network. It's not enough to find suppliers that offer the best supplies at the best value. The organization's relationships with these suppliers should also be maintained and cultivated to ensure they provide high-quality raw materials at the fastest turnaround times possible.
The best supplier relationships are characterized by healthy, two-way communication between the organization and the supplier. Supply chain managers can set goals and milestones to ensure these relationships continually improve over time.
5. Measure Total Cost of Ownership
When it comes to procurement, managers should focus on the total cost of ownership (TCO) of goods and services, rather than the usual practice of choosing suppliers based on price.
This approach makes sense considering the fact that the upfront cost of a product or service is equivalent to around 25% to 40% of its TCO. The rest consists of warehousing, operating, and transportation costs among many others.
Simply put, supply chain managers need to have more foresight when choosing suppliers. This is also another reason to maintain good relationships with vendors, who know how to use and extend the lifespan of their offerings.
6. Collaborate with Suppliers
By going beyond purchasing goods and services from suppliers, companies can unlock opportunities to generate more value from their supplier network.
For example, a procurement team for an advertising agency can solicit feedback from a supplier providing a lead generation platform. This simple step allows the agency to obtain suggestions on how to effectively integrate the platform into the company's existing lead generation systems and processes.
Collaborative supplier relationships can lead to streamlined operations, lower costs, and more agile processes.
7. Take Control of Contract Management
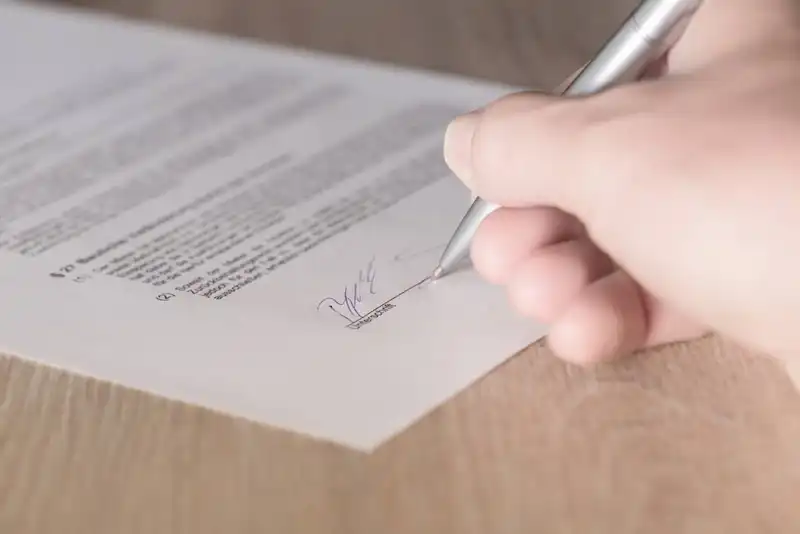
Moving contract management to the supply chain makes it easier to control the total cost of suppliers' goods and services. While savings are negotiated during procurement, they are rarely fully realized. This is often caused by a lack of communication or failure to follow-through on compliance.
By moving contract management to the supply chain, managers can keep a closer eye on contract compliance and leverage spend where there are opportunities to reduce costs and mitigate risk.
8. Optimize Inventory
Best-in-class organizations have the appropriate amount of inventory at all times. The goal is to maintain sufficient stock quantities to satisfy customer demand without carrying too much unsold inventory.
Optimizing inventory quantities is particularly important as holding and storing inventory can account for as much as 60% of the cost of an item. Conversely, not having enough product in stock can easily damage a company's reputation, as consumers are more than willing to take their business elsewhere when needed.
The key to optimizing supply chain inventory is forecasting and demand planning, which combine predictions of future consumer activity with historical data.
9. Review Supply Chain Operations Regularly
Creating a system of reviewing supply chain procedures and policies ensures their efficiency, compliance, and currency throughout the entire network. Remember, optimization is an ongoing process.
To prevent bottlenecks and reduce the risk of fraud and theft, a company's supply chain council and team members should continually measure the supply chain's performance.
10. Create Sustainable Practices
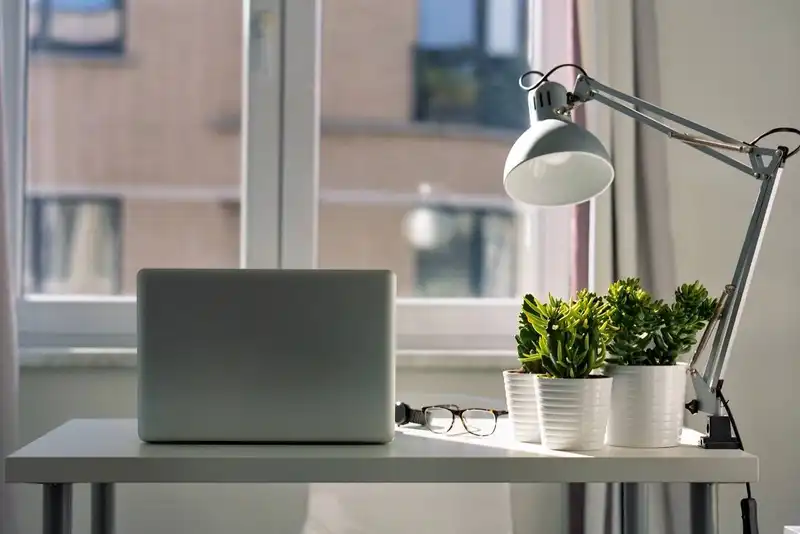
Best-in-class organizations go beyond reducing costs and driving as much value from suppliers. In a time of global climate protests, pressure from consumers, and government intervention, companies have actively taken steps to reduce their carbon footprint.
Fortunately, the typical supply chain has plenty of room for improvement when it comes to sustainability. The company's supply chain council can create a measurable framework of procedures and policies designed to reduce wastage and carbon emissions throughout the supply chain network.
For example, the company can choose suppliers that use transportation modes and fuels that are better for the environment.
While no two supply chains are alike, following these best practices can help companies take control of their supply chain operations, improve profitability, and transition to more sustainable processes.