How to Use the Inventory Carrying Cost Formula
Not only should businesses have a full overview of how many resources they are allocating on physical inventory products, but they should also understand how much they are spending to store and handle these goods.
Using the inventory carrying cost formula will help owners gain insight into their sum of expenses, effectively ensuring that they have the necessary information to create budgets and make profitable business decisions.
What is Inventory Carrying Cost?
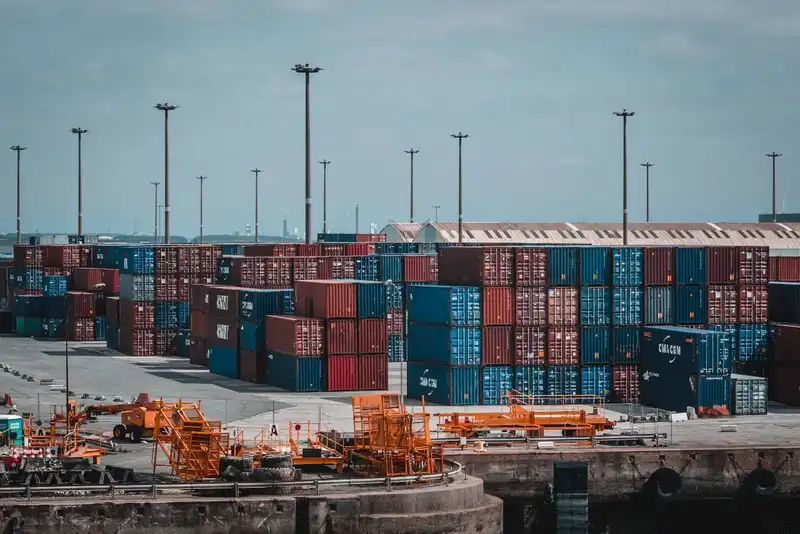
Inventory carrying costs, also known as holding costs, is the amount of money that a company spends on carrying stock products and maintaining them. These costs encompass warehouse rent, utilities for the facility, employee salaries, insurance, and inventory loss.
Typically, carrying costs amount to 15-30% of a business's inventory value. By calculating these expenses, management will be informed about how long they can carry their stock before its profitability decreases.
There are 4 key components of carrying costs.
- Capital Cost - The percentage of total inventory value, which includes the total amount invested in merchandise and any added interest. For instance, if a brand's capital cost is 30% and its inventory is worth $9,000, the capital cost is $2,700.
- Inventory Service Cost - These are expenses associated with insurances, taxes, and IT hardware.
- Inventory Risk Cost - Holding inventory can come with various risks, such as theft, misplacement, value depletion, and administrative errors. Loss of potential sales due to stock-outs, which is when products become out of stock, is also an inventory risk.
- Storage Space Cost - This entails rent for the warehouse space, transportation, and utilities, such as heating and lighting.
How to Calculate the Inventory Carrying Cost
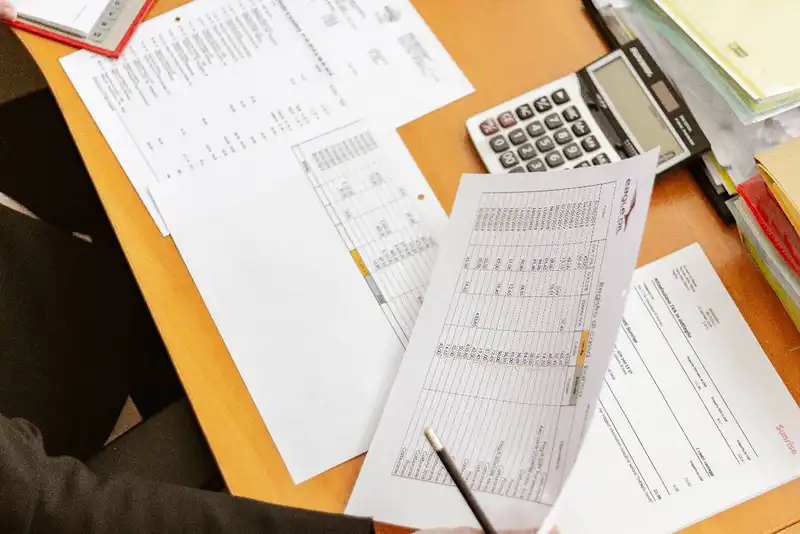
By understanding the 4 types of expenses that contribute to carrying costs, management can effectively calculate how much of their capital goes into holding inventory. Finding the carrying cost will also boost visibility into how much profit is being made with current goods.
Usually expressed as a percentage, the carrying cost can be calculated by dividing the inventory holding sum by the total value of the inventory, and then multiplying the result by 100.
- Carrying Cost (%) = ( Inventory Holding Sum / Total Value of Inventory ) x 100
To properly use the formula, management can follow these steps.
1. Determine Inventory Cost Components
Management teams should begin by calculating the different values for their company's inventory cost components.
For example, a bookstore may discover that its capital costs from purchasing inventory are $12,000 and that they spend $5,000 for service costs.
Additionally, the store finds that its inventory service costs from using management software and hardware amount to $5,000, and its inventory risk costs total to $3,000.
2. Calculate the Inventory Holding Sum
To find the inventory holding sum, the 4 inventory cost components must be added together.
The bookstore, for instance, would then have an inventory holding sum of $25,000.
3. Plug Into the Formula
After finding the inventory holding sum, the value should be divided by the inventory's total value, and then multiplied by 100 to find the carrying cost.
For example, if the bookstore had $100,000 worth of books and merchandise in their shop and warehouse, its carrying cost would be 25%. In detail, the calculations would be-
- Carrying Cost (%) = ( Inventory Holding Sum / Total Value of Inventory ) x 100
- Carrying Cost = ($25,000 / $100,000 ) x 100
- Carrying Cost = 0.25 x 100
- Carrying Cost = 25%
How Inventory Management Solutions Can Lower Carrying Costs
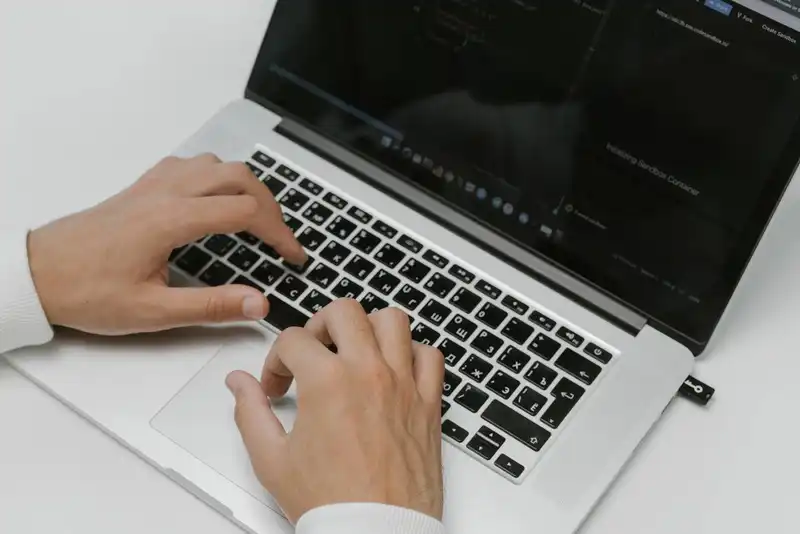
Calculating inventory carrying costs can help businesses track their spending and accurately quantify their profits. This ensures that their bottom line is protected and that operations run productively.
In the case that carrying costs are high, executives can lower these expenses with inventory management solutions that have order optimization capabilities. This type of software can streamline stock control processes and help businesses be cost-efficient.
Other benefits of inventory management systems include the following.
Only Pay for Necessary Features
Inventory management software providers oftentimes allow businesses to pay for features that align with their specific needs, such as extra storage space. In addition to decreasing inventory service costs, some of the solution's capabilities can also reduce labor expenses.
For example, the software simplifies stock counts with the implementation of bar code scanners. This means the company will not need a lot of employees to perform inventory counts.
Optimize Ordering Processes
The latest stock management systems have ordering capabilities that can increase order accuracy and suggest purchase quantities based on data about sales and inventory levels.
This helps ensure that the business maintains advantageous stock levels at all times and prevents instances of over-ordering, which would have resulted in surplus products and increased carrying costs.
Gain Valuable Insights
Inventory control solutions can be easily integrated with the company's point-of-sale (POS) systems, enabling important metrics to be collected and transformed into data reports. The software can provide valuable data concerning the speed of product movement, seasonality, and popular items.
These insights can be used for demand forecasting and for preparing the inventory to meet customers' needs.