How to Use the Reorder Point Formula to Optimize Inventory
Intro to Reorder Point Formula
For a business to run seamlessly and profitably, executives have to answer various questions about their inventory, such as how many raw materials or finished goods they need to purchase from their suppliers and when they should place these orders.
Business teams can accurately address these key concerns by using the reorder point formula. The reorder point helps when determining a company's inventory threshold and ensures that any delays to customer service are minimized.
What is the Reorder Point Formula?
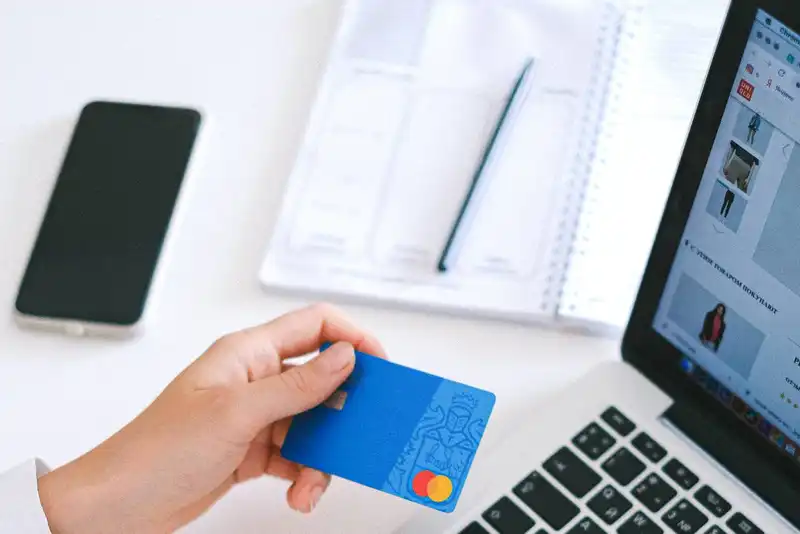
A reorder point is the minimum amount of inventory a business should have on hand. Essentially, it is a metric that informs executives of the best time to process another supplier order.
Organizations will typically have reorder points for each product in their inventory, from consumables to finished items. This enhances stock management and prevents production bottlenecks and interruptions to the supply chain.
Reorder points are also helpful for growing businesses that have large volumes of products because it enables managers to have better control over maintaining optimal stock levels.
How to Use the Reorder Point Formula
Business teams can calculate each of their inventory product's reorder points by utilizing the formula
- Reorder Point (ROP) = Demand During Lead Time + Safety Stock
To effectively use the reorder point formula, it is important to accurately calculate demand and safety stock.
Demand During Lead Time
Lead time refers to how long it takes from when an order is placed to when the product is finally received. This is typically quantified by the number of days. Businesses that have manufacturers or suppliers from different countries will usually experience longer lead times, compared to having domestic partners.
When calculating demand during lead time, the lead time for a product must be multiplied by the average number of products sold daily.
- Demand During Lead Time = Lead Time x Average Daily Sales
For example, if an upscale restaurant in New York has a lead time of 4 days to receive shipments of steak from Wisconsin and their average daily sales of steak is 20, their lead time demand is 80.
Safety Stock
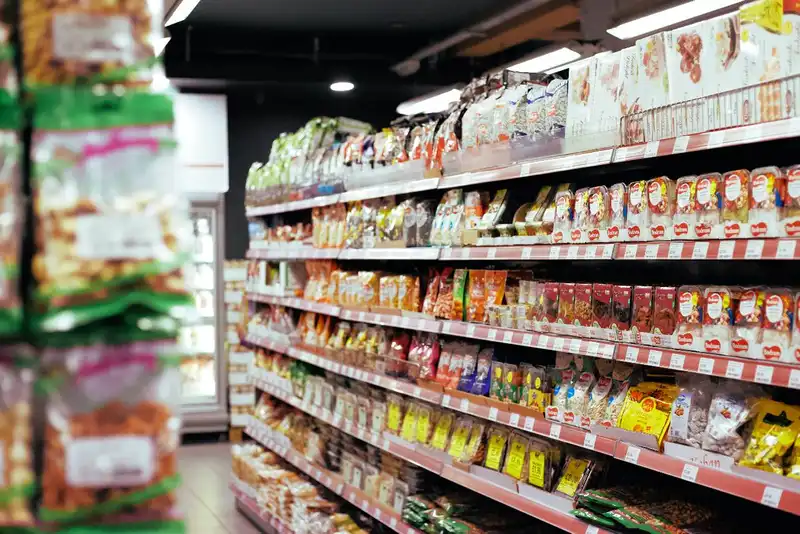
Safety stock is the additional quantities of goods that businesses keep on hand in case of a sudden increase in demand. It is also important to be prepared with safety stock because unexpected disruptions with supplier delivery schedules and transportation can cause delayed shipments.
With safety stock, operations will not be affected by these interruptions and brands can continue serving their customers.
To find the ideal safety stock level to have in the warehouse, executives need to multiply the maximum daily orders to their maximum lead time. And then multiple the average daily orders to the average lead time. Afterward, the two results must be subtracted to find the safety stock level.
Therefore, if the restaurant's daily maximum steak orders are 30 and the maximum lead time is 6 days, while the average daily sales are 20 steaks and average lead time is 4 days, the safety stock level is 100 steaks.
Plug Into the ROP Formula
After calculating the lead time demand and safety stock, the two values can be inputted into the reorder point formula.
Thus, according to the formula, the reorder point calculation for the restaurant in New York would be -
- Reorder Point (ROP) = Demand During Lead Time + Safety Stock
- ROP = 80 + 100
- ROP = 180 steaks
Importance of the Reorder Point Formula
Establishing reorder points ensure that customers' demands are always satisfied. Other benefits of a reorder point include the following.
Cut Down Expenses
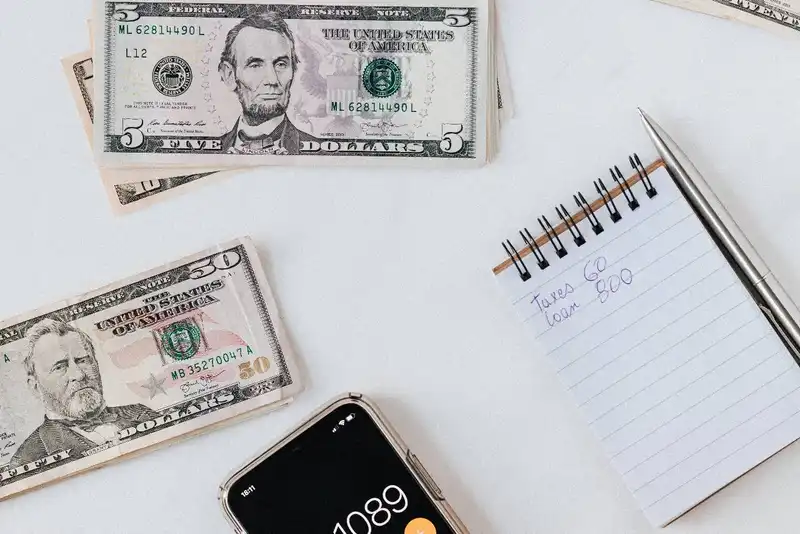
Over-ordering stock and having a surplus amount of products can be an inefficient use of resources, especially if consumers are not purchasing these items. Not only would these goods take up valuable warehouse space, but they will also incur carrying costs.
With reorder points, managers can make informed supplier purchases and ensure they are keeping opportune levels of stock at all times.
Reduce Stock-Outs
Having too little inventory can also negatively impact a business's bottom line because it increases the risk of stock-outs and lost sales.
Reorder points help companies make timely supplier orders and guarantees that the brand has enough goods to continue selling to customers while the new order is being processed and delivered. This enables the business to provide excellent service and to uphold a dependable reputation among consumers.
Improved Demand Forecasting
When calculating reorder points, business teams must also consistently monitor and assess demand trends and customer behaviors. Doing so helps executives have better visibility into their forecasting abilities and can improve projection accuracy.
The Relationship Between Reorder Point Formula and Safety Stock
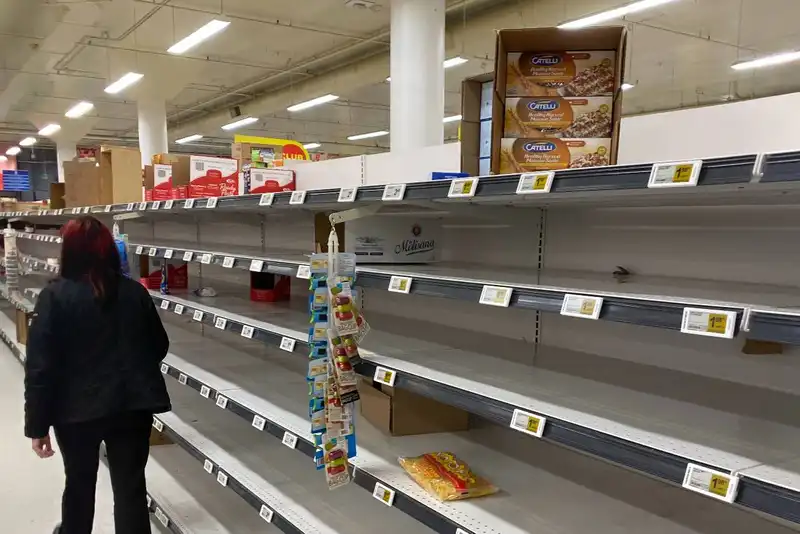
Understanding both reorder points and safety stock can help businesses hone in on their inventory management and optimization.
These two components also help prevent stock-outs, in which reorder points ensure replenishment orders are placed and safety stock guarantees that there are extra products in the storeroom.
Safety stock, also known as buffer stock, is considered a business's last line of defense in regards to averting stock-outs. On the other hand, a reorder level is the second-to-last defense technique.
Depending on calculations, safety stock can affect a business's bottom line if its levels are too high. To lower safety stock levels and ensure that excess products will not be left unsold in the warehouse, managers can utilize the following tips.
- Use Automation
- Enhance the Supply Chain
The Relationship Between Reorder Point Formula and Safety Stock
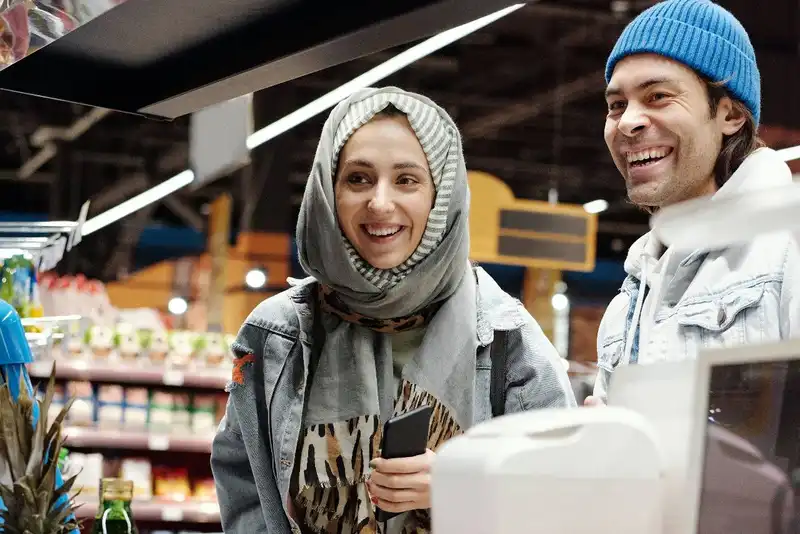
- Decrease Lead Times
In the case that the supplier is unable to provide their products quicker, business owners should search for another vendor who can.
- Be Proactive With Shifting Demands
- Assess All Inventory Products
Strategies for Reorder Point Formula Planning
When developing plans for reorder points, organizations should consider optimizing various components in their inventory and supply chain management.
Businesses can adopt these strategic approaches to their reordering points.
1. Understand That Reorder Points Are Not Static
Consumer demand trends and market conditions are turbulent and can change unexpectedly during a given period. Therefore, when business teams establish reorder points, they must regularly review them to ensure they are up-to-date.
Typically, organizations will assess their reorder points every quarter to make sure that it reflects current demands. Any adjustments, such as lowering or increasing the metrics, should be done promptly.
2. Implement New Inventory Technology
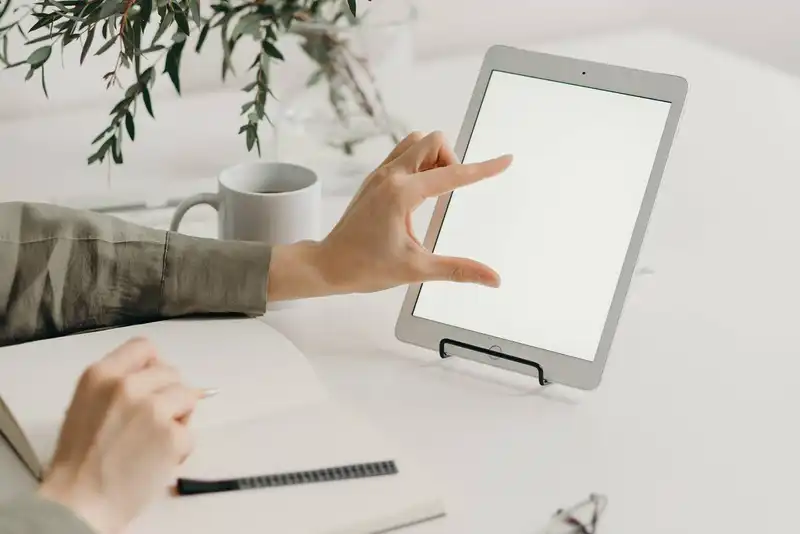
Modern inventory management software has advanced capabilities that can streamline stock control tasks. It has features that automate purchase orders and can also provide real-time data reports regarding profits, inventory levels, and sales.
This can create a positive impact on a business's bottom line because it promotes informed buying decisions, inventory maintenance, and demand fulfillment.
3. Assess Product and Business Performance
In order for a reorder point strategy to be efficient, executives must reevaluate their products' performances, as well as their marketing and advertising progress.
Since trends fluctuate, it will be helpful to understand whether their reorder point strategies are working as intended and if adjustments need to be made.
It is also recommended that teams assess their target demographics and see if their promotional campaigns are adequate in garnering attention for a product.
4. Strengthen the Supply Chain
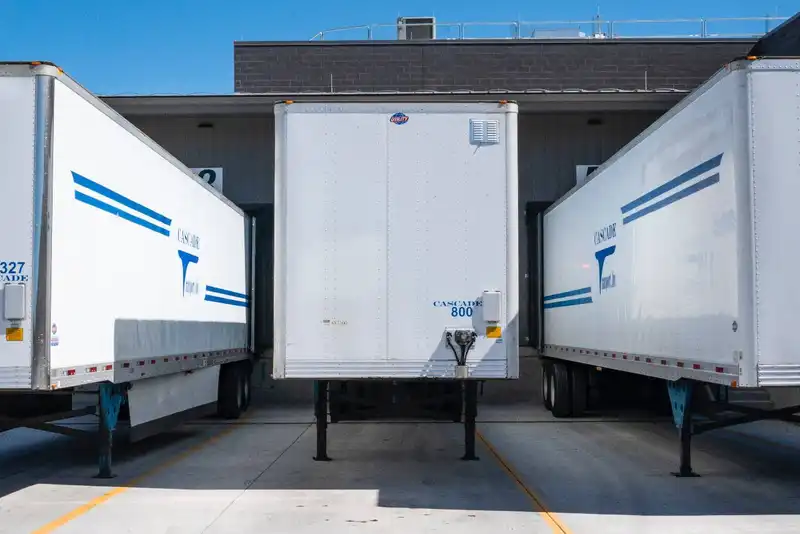
Business operations will run seamlessly, as long as all partners, third-party suppliers, and distributors are proactive and reliable.
When suppliers have inconsistent schedules or often have issues with adhering to established contracts, the company will be unable to efficiently meet customers' needs. If a business owner is experiencing an undependable supplier, they should find new resources to strengthen their supply chain.
Regularly examining supplier performance and performing audits will ensure that any problems or discrepancies are addressed quickly.
If possible, companies should look into working with local suppliers because it allows managers to have more face-to-face interactions. Having a list of alternative suppliers will also be useful, in case current vendors are unable to supply goods.
5. Go Beyond the Reorder Point
While reorder points are crucial for recognizing when to replenish inventory, management should take into account different key factors as well.
For example, understanding the company's economic order quantity will provide visibility into how much inventory the business needs to order while minimizing costs associated with holding inventory and shortages.
How Zip Ordering Simplifies Reorder Point Formula
Zip Ordering is an inventory management tool that simplifies the ordering processes. This digital tool helps businesses streamline time-consuming and laborious tasks associated with maintaining stock and managing suppliers.
Some of the key functions of Zip Ordering are-
Inventory Management
Zip Ordering optimizes inventory management by allowing business users to track their stock, set budgets, and assess orders from different suppliers. It also has real-time order management capabilities, in which executives can see their current orders that are in transit and access all order invoices.
A critical feature of this software is its suggested ordering and low inventory alerts because it helps make sure that stock is kept at optimal levels at all times.
Demand Forecasting
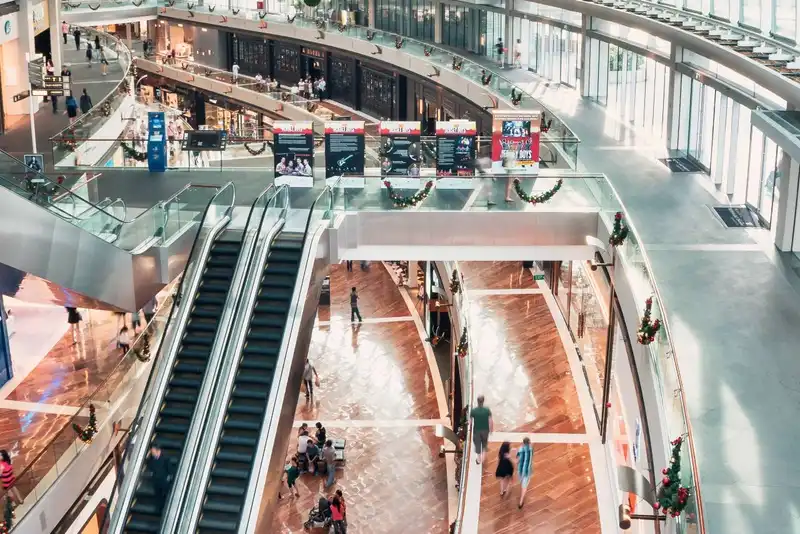
The Zip Ordering platform collects data regarding historical orders, sales, and inventory levels, giving executives access to key information and trends to accurately forecast demand.
Intuitive Reports
Along with data about orders and sales, Zip Ordering provides insightful and easy-to-read reports concerning spending and supplier pricing. These statements can help management teams monitor their financial budgets, ensure ordering accuracy, and maximize profits.
In Conclusion - Reorder Point Formula
A key aspect of maintaining inventory and meeting customer's expectations is establishing the reorder point for all stock products. With accurate calculations and the right tools, businesses can guarantee a streamlined operation and supply chain.