MRO Inventory Management - 5 Best Practices
There is a specific type of non-lucrative inventory that businesses have to maintain in order to produce finished merchandise.
Maintenance, repair, and operation (MRO) inventory is used to keep equipment and operations optimized at all times. Without MRO supplies, machines can experience increased technical difficulties, malfunctions, and breakdowns.
What is MRO Inventory?
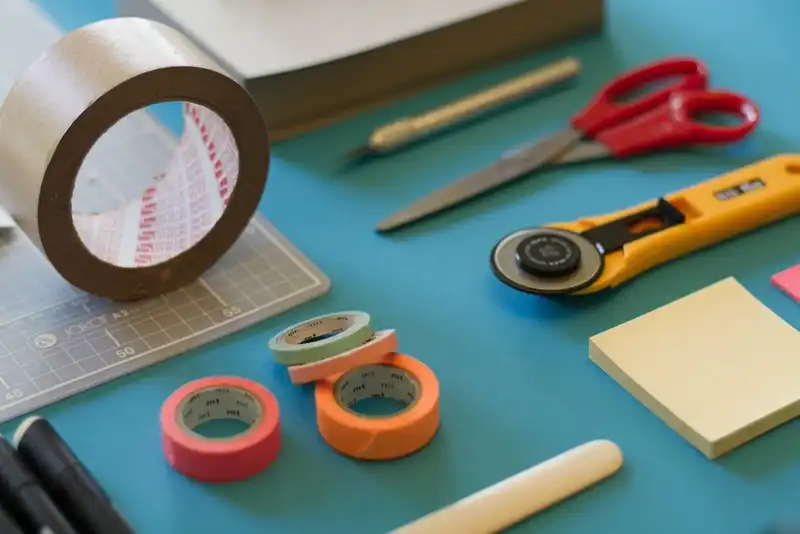
MRO inventory consists of supplies used during the manufacturing process but is not part of the finalized product. Typically, this inventory is controlled by the organization's maintenance department. Common MRO items include-
- Personal protective equipment (PPE)
- Computers
- Maintenance supplies
- Industrial equipment
- Office supplies
- Cleaning supplies
While businesses do not generate a profit from MRO inventory, it is necessary to produce goods and services. This inventory requires routine replenishment and, therefore, its own budget to maintain healthy stock levels.
Without MRO supplies, companies can't perform maintenance, repairs, or diagnostics on internal operations. MRO inventory prevents equipment malfunctions so businesses can maintain a smooth workflow.
The Importance of MRO Inventory
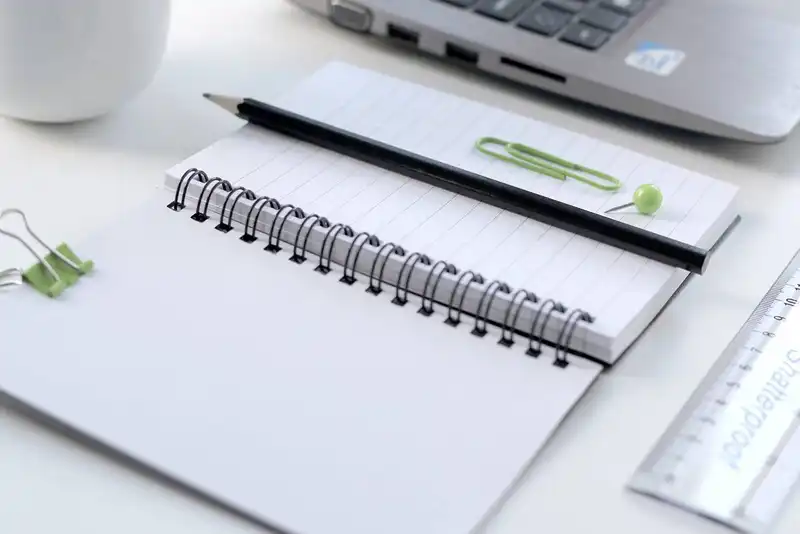
The importance of MRO inventory becomes obvious when discussing the various direct and indirect expenses that companies would have to supplement if they didn't maintain these materials-
Product Stoppages
MRO materials keep production lines operating so businesses can continue producing goods. If these supplies run out, all manufacturing must stop, meaning all employees must standby. Meanwhile, the company must pay their waiting employees, as well as expedited shipping to get MRO inventory as soon as possible.
Even once the materials arrive, it may take days or weeks for technicians to fix machinery, resulting in another heft expense. All the while, the business is losing potential sales from the downtime, significantly impacting their bottom line.
Therefore, organizations should actively monitor their MRO levels to ensure there is always enough to support current operations.
Overstocking
On the other end of the spectrum, keeping too much inventory on-hand will lead to inflated storage costs. However, many businesses make this mistake as an effort to prevent stockouts.
In reality, storing too many products can clutter maintenance rooms, making it hard to navigate and locate certain materials. When supplies can't be found, managers may have to order more, knowing they already have some on-hand.
To avoid this, companies should keep an organized storage room with accurate records of what products are on-site to avoid overordering.
Decreased Productivity

Aside from stockout events, poor MRO inventory management can affect daily operations. Studies show that technicians spend up to 25% of their time finding parts. Although this may only extend downtime by minutes, any recurrence will significantly decrease productivity.
Maintenance workers can prevent this by keeping their own separate inventory log that outlines where tools and materials are for easy retrieval.
5 Best MRO Inventory Management Practices
Companies can prevent problems stemmed from poor MRO inventory management by considering the best control practices-
Establish MRO Management KPIs
Organizations can efficiently monitor their MRO inventory by establishing measurable benchmarks or key performance indicators (KPIs). KPIs quantify various performance elements so managers can determine when they need to intervene.
While companies can establish as many KPIs as they deem necessary, all businesses should monitor-
- Supplier performance
- MRO inventory turnover rates
- MRO spend percentage of the procurement budget
- Ratio of rush orders to replenishment orders
- Stockout frequency
- Total stockouts
- Inventory lifecycle
Train Staff on MRO Sourcing and Supply Chain Management
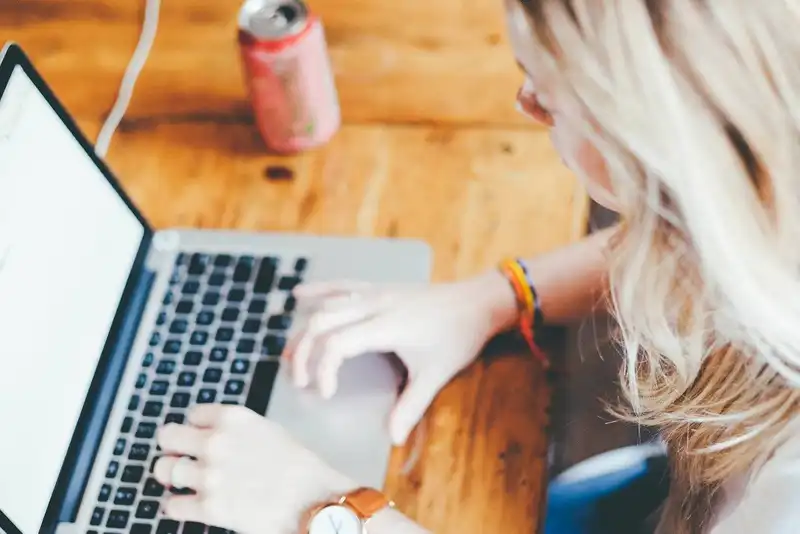
An MRO management system is only as effective as the employees that run it. Therefore, companies must prioritize training staff on how to source MRO materials and manage the supply chain.
Training should cover how to procure stock and interact with employees from different departments. This establishes a healthy, harmonious work environment where workers understand their roles. As issues arise or more training is needed, supervisors can hold special workshops.
Locate MRO Inventory Centrally
Departments that operate independently tend to duplicate purchase orders, resulting in excess stock and procurement costs. By keeping inventory records in a centralized location, companies can improve their MRO inventory control and efficiency.
Implement Management Systems
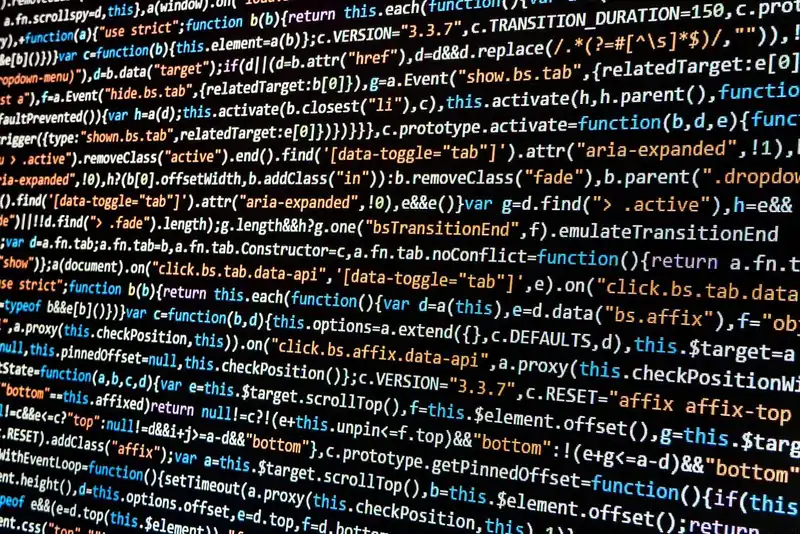
Businesses can optimize their internal communication and data exchange by implementing inventory management and ordering systems. These solutions automate standard stock tasks, such as cycle counts and procurement, ensuring organizations maintain minimum products on-site.
The software also establishes a centralized interface, where employees throughout the company can access inventory data. Advanced ordering solutions even connect businesses to their vendors for easy procurement. This functionality extends visibility into the supply chain and enables managers to supervise suppliers' performance.
Consider Utilizing Vendor-Managed Stock Services
Some businesses do not have enough employees to dedicate to stock management and procurement, while others prefer leaving it in the hands of firms that specialize in that department. Either way, organizations can use third-party services to enhance their MRO supply management.
By leaving this process to businesses with expertise, companies may experience heightened productivity and operational efficiency.