5 Common Causes of Inventory Discrepancy to Watch Out For
Although every company is bound to experience an inventory discrepancy somewhere in their supply chain, they can reduce the threat of in-house error through proper management.
By taking the right preventative and corrective actions, businesses can improve their inventory accuracy, operational efficiency, and responsiveness.
5 Common Causes of Inventory Discrepancy
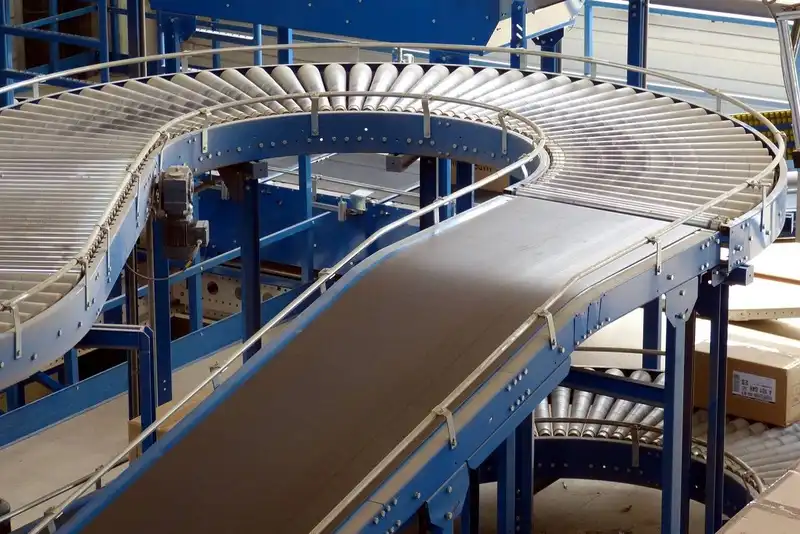
In order to improve data accuracy, businesses need to understand the common causes of inventory discrepancy. Otherwise, companies must rely on guesswork to reconcile stock rather than pinpointing and preventing the issue.
Shrinkage
Studies show that shrinkage cost businesses around the world $128 billion in 2014 alone, $42 billion of which took place in the US. Shrinkage comes in many forms, including-
- Shoplifting
- Administrative errors
- Employee fraud
- Supplier fraud
- Lost items
Typically, shrinkage accounts for approximately 1.3% of all retail sales. This not only impacts net income and profits but must also-
- Financial reports
- Stock levels
- Inventory management
- Inventory expenses
Resolving discrepancies can be time-consuming and require additional resources and labor, eating even more into profits.
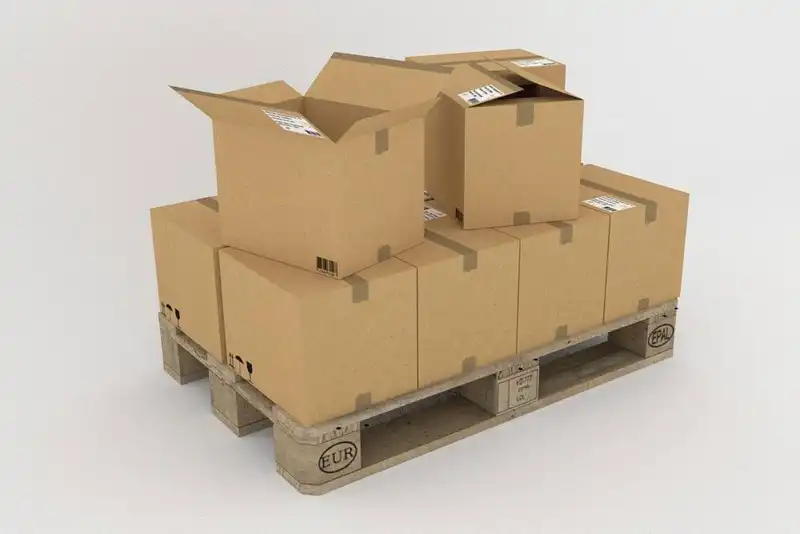
While there are several solutions to inventory discrepancies, businesses should start by implementing preventative measures. Firstly, owners should be careful whom they assign to manage inventory. Stock managers must be trusted employees that remain in good standing and are adequately trained.
Owners should openly discuss the types of fraud with workers to ensure them the appropriate safety measures are taken to secure stock and keep employees accountable. This will deter rogue workers from attempting to steal items.
However, employees are not the only threat to inventory, as vendor fraud accounts for 5% of inventory shrinkage. Therefore, warehouse workers should cross-examine their purchase orders, shipping lists, and invoices, as well as perform quality checks once units arrive to ensure all products are present.
Once employees verify that they receive the correct amount of inventory and products are in good shape, they can then enter the quantities into the management system.
Incorrect Location
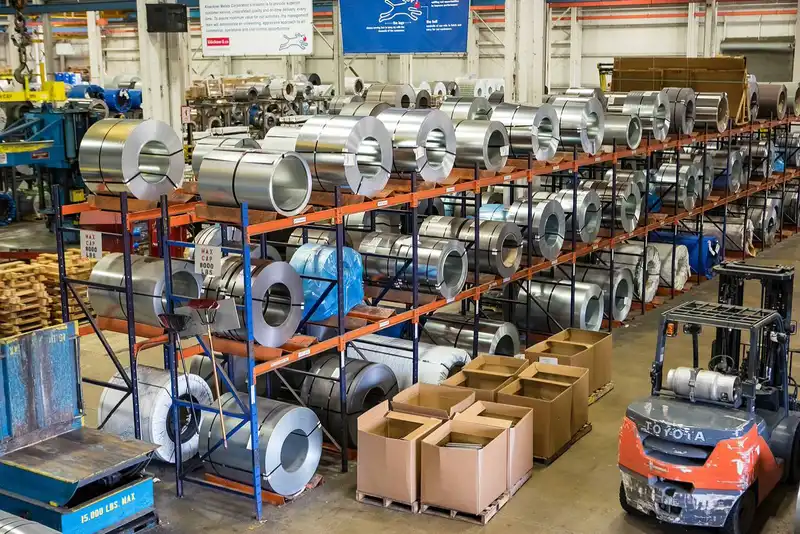
Companies with a large supply chain or multiple warehouse locations often struggle with misplacing products. Shipments may be delivered at the wrong site, requiring item transfers, which can quickly add up.
There are two primary types of misplaced inventory-
- Sometimes products are simply misplaced because employees immediately enter the units into the system upon arrival but send them to an incorrect location.
- Customers can also misplace items along their shopping journey. Instead of returning a product to its proper place after deciding they no longer want it, shoppers often place items on the closest shelf. This requires employees to hunt down inventory throughout their facilities manually.
While not all inventory discrepancies can be prevented, businesses can actively improve their control by ensuring products are stored in their correct locations.
Human Error
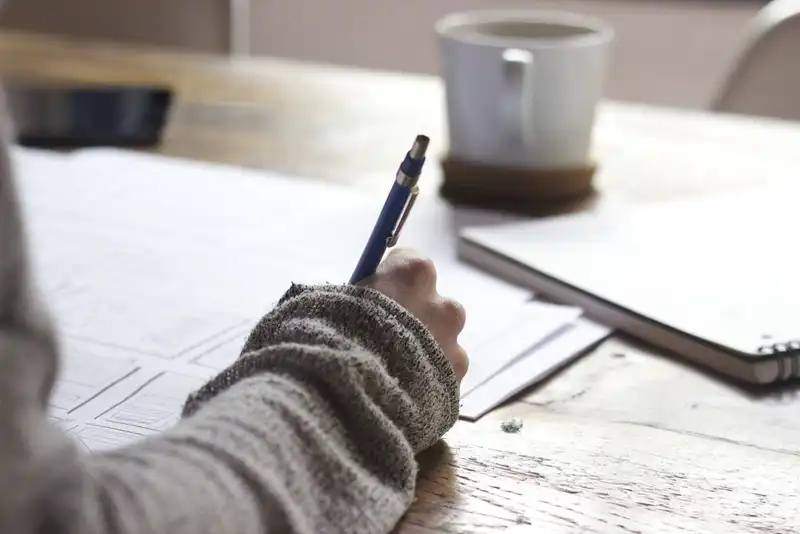
It is critical to understand that one human error is not an independent event, it impacts every sequential operation. For example, miscounting an inbound shipment will significantly affect order fulfillment, picking, and stock ordering. Businesses with excessive human errors are more prone to experience stockouts, backorders, and inflated inventory expenses.
Although many things can lead to inventory discrepancies, human error often create the most significant problems. Therefore, businesses should invest the appropriate time and resources to train employees on how to receive, count, and manage products. Proper training can minimize the risk of discrepancies down the line.
However, human errors may occur up the channel of the supply chain from suppliers, distributors, and other third parties. Businesses are most vulnerable to these mistakes while they are accepting inbound shipments. To decrease the negative effects or prior errors, managers should double-check deliveries to confirm quantities are correct.
Inadequate Return Policy
Customer returns are complicated services, as businesses need a system that records the item's return and reassignment, so records account for more inventory. Companies must assign disposition codes to returning merchandise so they can be assessed and reentered into the system.
Many organizations neglect this process and experience inventory inaccuracies as a result.
Employees should understand how to perform returns and input them into the management systems to alert their warehouses. With adequate training, customers do not have to wait long while the worker completes the transaction. However, speedy service should not come at the cost of accurate performance.
Poor Inventory Management
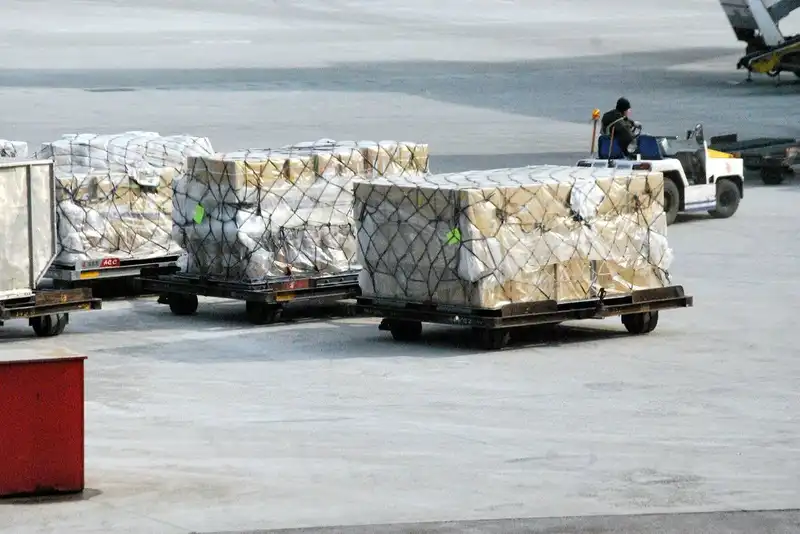
Companies with manual inventory control methods experience far more inventory errors and discrepancies than those with automation tools. Modern inventory management systems use machine-learning software to maintain healthy stock levels. These solutions also generate detailed analytics on-
- Turnover rates
- Profit margins
- Stock quantities
- Product returns and exchanges
- Sales trends
By understanding the performance of each product line, organizations can anticipate fluctuating demand patterns to improve sales and order fulfillment.
Software automation also eliminates the need for human intervention, minimizing errors and resources needed to perform standard tasks, such as cycle counts.