4 Steps to Calculate Safety Stock Inventory Levels
Consumer demands consistently fluctuate, effectively impacting the products that retailers stock and carry on store shelves. To ensure that a company is prepared and has enough products to satisfy customer needs, management must have safety stock available.
By maintaining the right levels of safety stock, businesses will enhance their cash flow and prevent disruptions in customer service.
What is Safety Stock?
Safety stock is an additional amount of products a company has in inventory to prevent the risk of stock-outs.
Having safety stock enables the brand to fulfill orders in case the actual consumer demand exceeds the levels managers had forecasted. Manufacturers will also keep safety stock of raw materials so that production will not be delayed, ensuring that the supply chain is operating seamlessly.
Carrying safety stock is important because it helps businesses keep up with demand trends. It also assists companies that work with suppliers with inconsistent lead times or are unable to deliver extra units at a certain period. With safety stock, retailers can still provide to their customers despite having late deliveries.
While having additional quantities of inventory in the warehouse can increase holding costs, these expenses will typically be less than the costs associated with pausing production or stock-outs.
4 Steps for Calculating Safety Stock
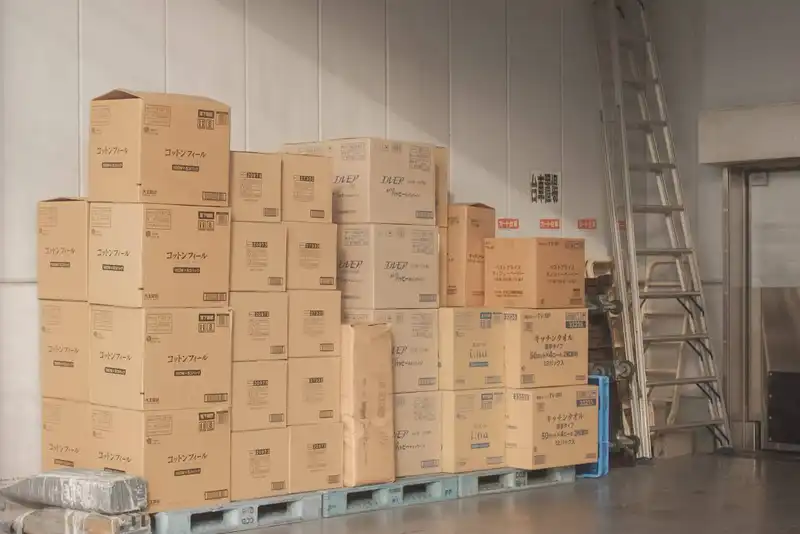
Organizations can effectively calculate how much safety stock they need to maintain by following 4 key steps.
1. Calculate Lead Time
Lead time refers to the amount of time between when a process is started and when it is finished. Factors that typically affect a retailer's lead time is purchase approval, vendor communications, suppliers' delivery schedules, and shelving products.
To calculate lead time, managers need to identify the expected lead time of a product, the actual time it takes to replenish an order, and the difference between the expected and actual times.
For example, if a parcel of inventory is expected to arrive in 6 days but the actual time was 11 days, the variance would be 5. However, if the actual time were 4 days, the variance would be negative 2. The negative number indicates that the delivery came earlier than expected.
Once this information is calculated, managers can find the standard deviation by adding all their variances in the sample and then dividing the sum by the number of samples they are calculating. Lastly, the quotient needs to be added to the average expected time. The final number is the standard deviation for the lead time.
2. Calculate Demand
To calculate average demand it is important to look at how long it takes until a product needs to be reordered. If an item is typically replenished once a month, managers should then find their sales volume from a specified month.
The total sales volume should then be divided by the number of buying days, which for this example would be 30 days. The quotient from this calculation is the demand average.
3. Identify Service Level
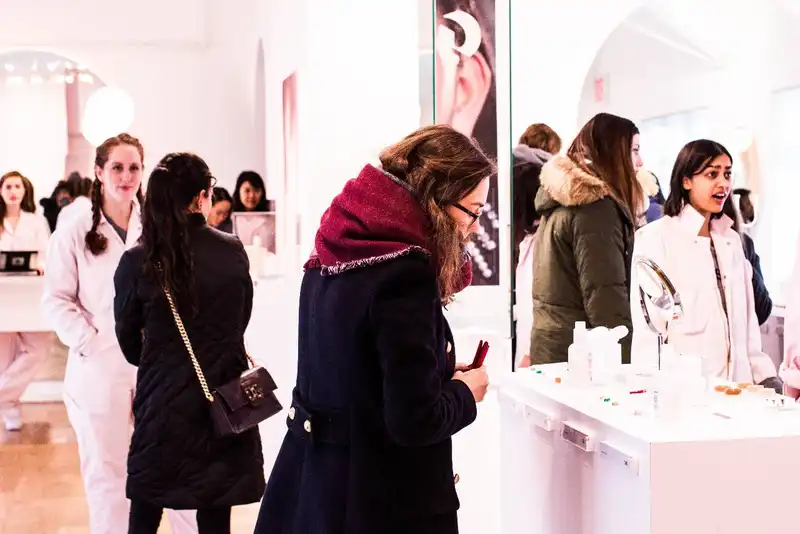
Service level is a percentage that measures the probability that a company can provide products to customers and not experience a stock out or lost sales. A business that has a high service level will need more safety stock on hand.
Most retailers will try to maintain a service level that is between 90% and 95%. It is recommended that management use a normal distribution chart to establish their service level.
4. Calculate Safety Stock
Once the lead time, demand average, and service level is identified, managers can multiply all 3 of the values to find the safety stock.
For example, if a business's lead time is 8 days, the average demand is 85 parcels, and the service level is 1.28, the safety stock is 870.4 parcels. Therefore, management should purchase 870 parcels of safety stock to meet demand.
The number of safety stock can also be used as a reorder point, which means once a store's main inventory reaches this level, they should replenish before a potential stock-out occurs.
Safety Stock Formulas
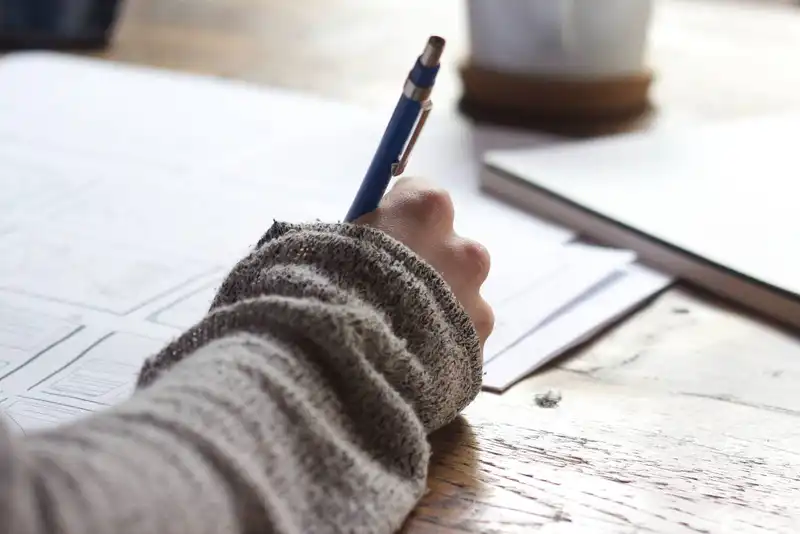
There are various methods of calculating safety stock depending on the type of business and its industry. Organizations should find the best formula that most aligns with their operations.
1. Safety Stock Formula
This is the traditional approach to identifying safety stock. To use this formula, managers need to multiply the number of inventory they sell in a day by the number of days worth of stock the company wants to carry.
2. Average Max Formula
This formula is the most common and is recommended for businesses that do not have a long lead time. This method enables managers to find the average maximum unit of a product they need to carry in a given period.
To find the max average, the maximum sale and maximum lead time need to be multiplied. Then, the average sale and average lead time need to be multiplied. Finally, the two products from these calculations are then subtracted. The final number is how much managers should buy as safety stock.
3. Normal Distribution with Demand Uncertainty
This formula is helpful when demand regularly fluctuates while lead time is consistent. The safety stock can be calculated by multiplying the standard deviation of the demand by the root average delay.
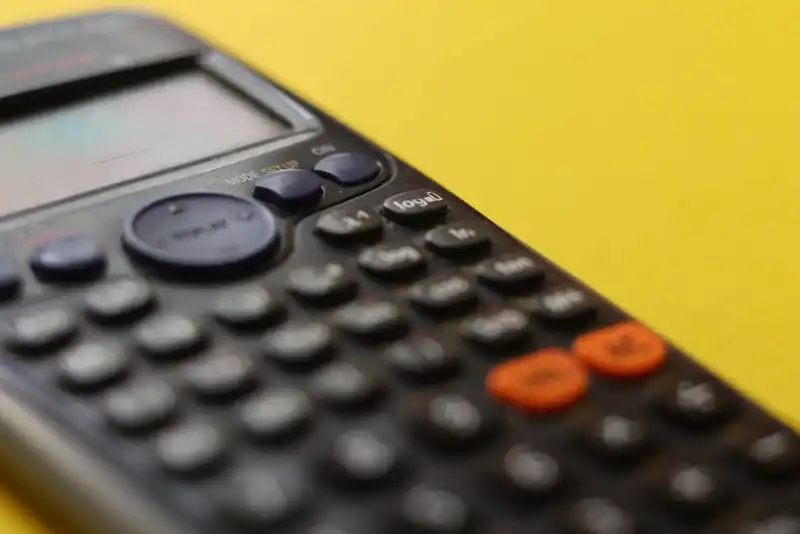
4. Normal Distribution with Lead Time Uncertainty
When lead time is inconsistent, businesses can calculate their safety stock level by multiplying their desired service level to average sales to lead time deviation.
5. Normal Distribution with Demand Uncertainty and Independent Lead Time
In the case that a business is uncertain about its demand and lead time, the safety stock can be found by using this formula-
- Z * sqrt((Average LT*(Demand Standard Deviation) squared + (Average Sales * Lead Time Standard Deviation) squared)
6. Normal Distribution with Demand Uncertainty and Dependent Lead Time
When demand and lead times impact each other, managers can use the formula-
- Z * Demand Standard Deviation * Sqrt (Average LT) + Z * Average Sales * Lead Time Standard Deviation
Being prepared with safety stock is critical because it ensures consumer demands are fulfilled at the most opportune time. By carefully calculating the right safety stock levels, companies can increase sales and maintain profitability.