9 Types of Inventory All Businesses Should Monitor
Understanding the different inventory types enables businesses to maintain healthy stock levels to promote workflow throughout the supply chain. With effective inventory control methods, companies can ensure there are sufficient supplies at each phase to continue operations and meet customer demand. This also allows organizations to focus on other important processes, such as logistical needs.
Logistics management is another essential process that regulates the activity of materials within the supply chain, from inventory storage to final deliveries. With established management systems, businesses can differentiate inventories and efficiently monitor stock usage.
Different Types of Inventory
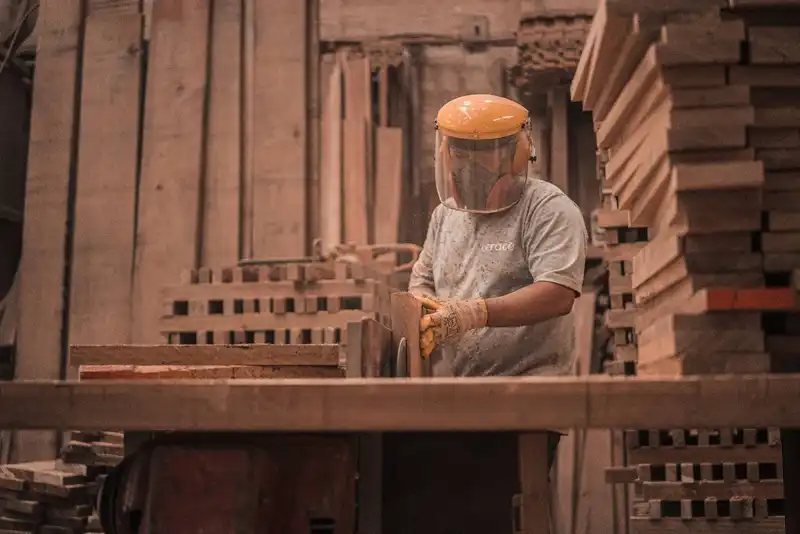
Companies within the supply chain will generally handle multiple inventory types, with the exception of retailers that only receive the finished products. For example, textile companies convert raw materials into fabrics, which are later assembled into articles of clothing. Therefore, businesses should understand how monitoring each type of inventory affects sequential processes.
1. Raw Materials
Raw materials are the initial supplies used by manufacturers to produce components or finished products. This type of inventory may be extracted from natural sources or purchased from suppliers. Even if the supplier classifies the stock as a finished product within its organization, it is considered as raw material once it reaches the production company.
In other words, supplies used to build larger parts are known as raw materials. These produced parts are considered components, as they become part of a subassembly to create the final product.
Typical raw materials include grains, minerals, natural gases, chemicals, wood, paper, metals, and food items. However, components such as nuts, bolts, and wheels may also be considered as raw materials if they are used to assemble a larger product.
2. Work-In-Process
Work-in-process (WIP) inventory is composed of raw materials and components waiting or in the middle of being processed. This includes all materials, from shipped supplies to completed products awaiting final inspection before order fulfillment. Components are also WIP inventory as they fall between raw materials and finished goods.
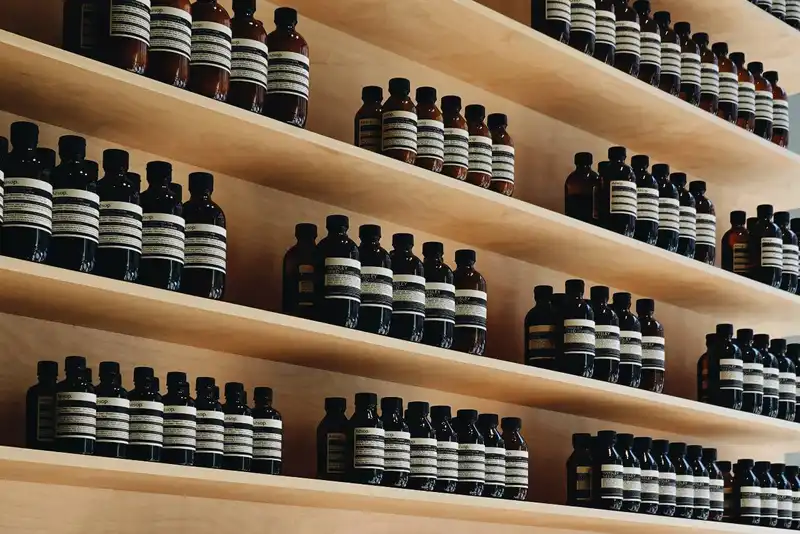
3. Finished Products
Finished products are completed goods that are used to fulfill customer orders. This type of inventory has passed through the production phase and undergoes inspections before distribution. After quality assurance, finished products are sent off to retailers, fulfillment centers, or straight to the consumer.
Finished products can be further classified into subcategories, such as transit, buffer, anticipation, decoupling, cycle, and MRO inventory.
4. Transit Inventory
Also known as pipeline stock, transit inventory is the finished product that is transported from one location to another. This does not include items moving between supply chain phases within the same building, but rather goods shipped to external businesses
Merchandise shipped by freight carriers and trucks may take days or weeks to reach their destination. Therefore, logistics management must consider transit times when determining how much stock to ship, as longer delivery estimates may require larger orders.
5. Buffer Inventory
Also known as safety stock, buffer inventory is the excess products that companies produce and store on-hand for unpredictable events. This may include shipment delays, supplier stockouts, or quality assurance failures.
Typically, organizations with plenty of buffer inventory have excellent customer service. With healthy safety stock levels, businesses can avoid backorders, customer complaints, and operational disruptions. This ensures that companies can maintain customer retention, satisfaction, and revenue.
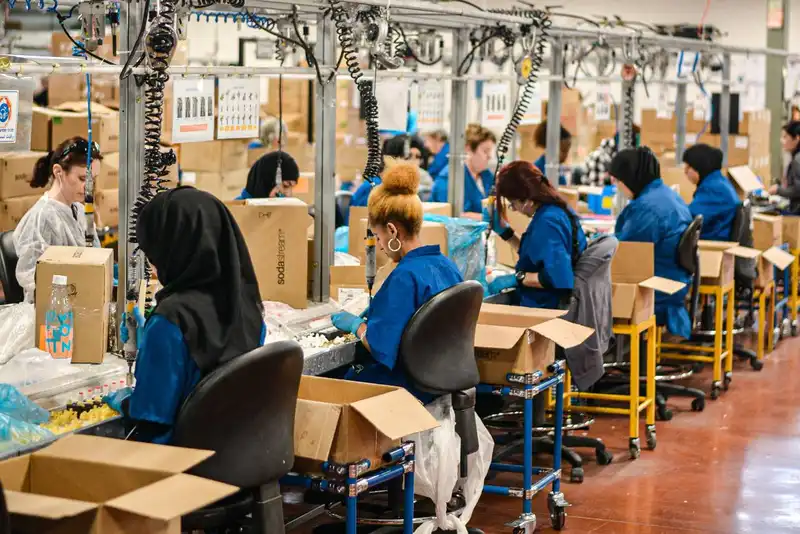
6. Anticipation Inventory
Similar to buffer inventory, some businesses store extra products to anticipate future events. However, this stock is kept for possible changes in demand or price.
Many retailers build up their anticipation inventory months before peak seasons, such as Halloween, Christmas, or back-to-school shopping. On the other hand, manufacturers begin storing extra stock while the demand is low to keep workflow steady. This prevents employee downtime and stockouts during busy seasons.
7. Decoupling Inventory
While assembly lines have co-dependent phases that require completion before moving to the next process, very rarely do machines operate at the same pace. This results in fast processing rates from one step and lagging production in another.
Yet, when looking at an assembly line, it may seem like all operations are performing at the same speed, maintaining a smooth workflow. This is because decoupling inventory between phases provides the necessary components to continue the operations.
This stock acts as a link between processes to prevent inefficiencies and manufacturing disruptions. With healthy decoupling inventory levels, management does not have to worry about manually regulating the sequential system to keep production on schedule.
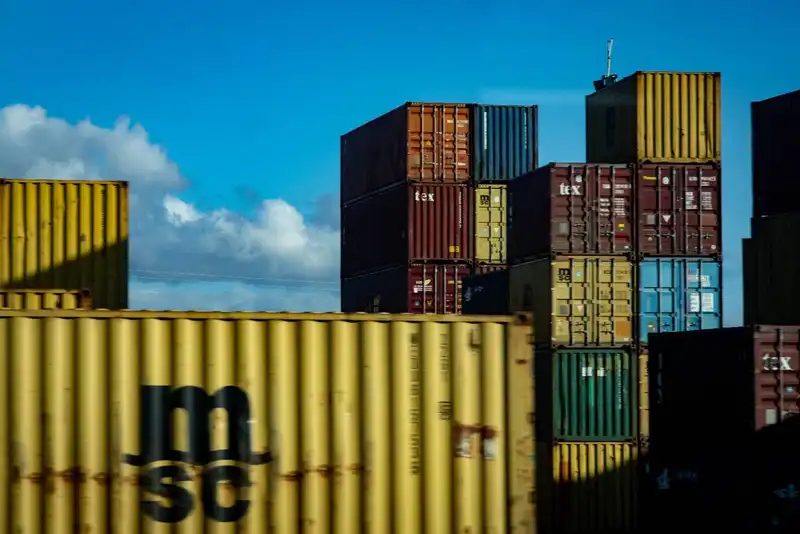
8. Cycle Inventory
Cycle inventory, also known as lot-size inventory, refers to excess products strategically purchased in batches to balance inventory costs, rather than ordering supplies on an order-by-order basis. Businesses aim to find their economic order quantity (EOQ), or ideal inventory orders, to reduce stock expenses, such as holding and ordering costs.
While buying in bulk may reduce ordering costs, the holding costs associated with storing the products may increase. On the other hand, purchasing smaller batches may drive shipment costs but minimize storage expenses. The purpose of EOQ is to maintain healthy stock levels while minimizing total inventory costs.
9. MRO Goods
Maintenance, repair, and operating (MRO) goods are supplies used to streamline manufacturing processes by maintaining productivity levels. While these materials are essential for different production phases, they are not a part of the finished goods. MRO examples include lubricants, coolants, oils, personal protective equipment, tools, and office supplies.
Companies that create or carry physical merchandise require an inventory system that monitors product quantities. An inventory management system ensures that businesses can maintain healthy stock levels to sustain their production schedules. Without proper inventory control, production, order fulfillment, and other supply chain operations can experience delays and discrepancies.