Complete Guide to Logistics Management - Definition, Process and More
Introduction to Logistics Management
The supply chain consists of several levels designed to produce and distribute goods, from retrieving raw materials to producing finalized products. As supplies move through operations, the need for product supervision and transportation emerges. These phases rely on detailed planning from the logistics management department to keep processes on schedule.
Without successful logistics, the workflow can be hindered by delayed shipments, incorrect storage units, and increased product returns. On the other hand, when the material movement is properly mapped throughout the supply chain, businesses can improve their warehouse efficiency.
Therefore, companies can benefit from investing their time and effort into ensuring their logistics management can appropriately coordinate all transportation needs.
What is Logistics Management?
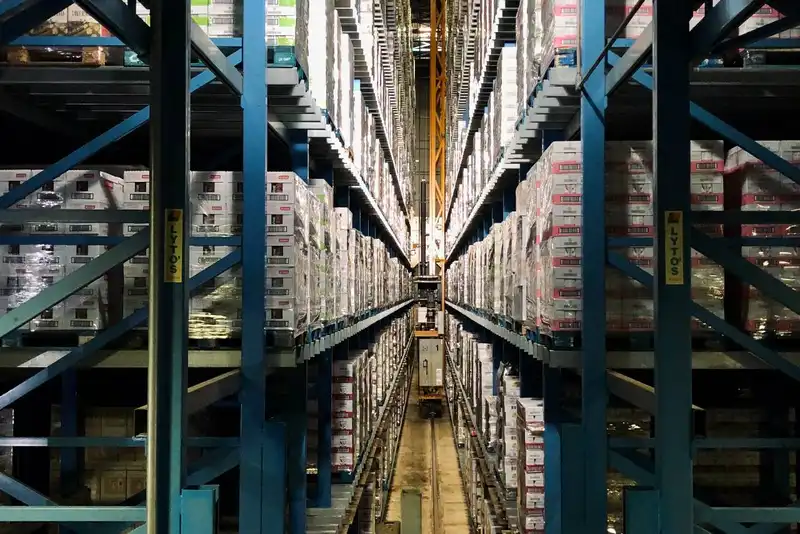
Logistics management is a process within the supply chain that focuses on the planning of transporting and storing goods before the final sale. The plan ensures that products promptly arrive at their destination and are kept appropriately. Successful logistics management can reduce carrying costs and improve customer satisfaction.
Logistics management begins when raw materials are shipped and ends when the finished product is delivered to the customer. Due to the duration of this process, managers need to implement strategic planning to efficiently facilitate the various steps. There are several elements to successful logistics management, including-
- Choosing vendors that offer transportation facilities
- Finding the fastest transportation routes
- Searching for the best delivery method
- Utilizing software to automate standard processes
Logistics managers must consider each element to avoid accumulative issues. For example, poor transportation management can delay deliveries, resulting in unsatisfied clients. Inadequate planning can also create additional expenses due to uneducated decision-making. Therefore, companies should focus on learning the different logistics management types and how to properly oversee these processes.
Types of Logistics Management
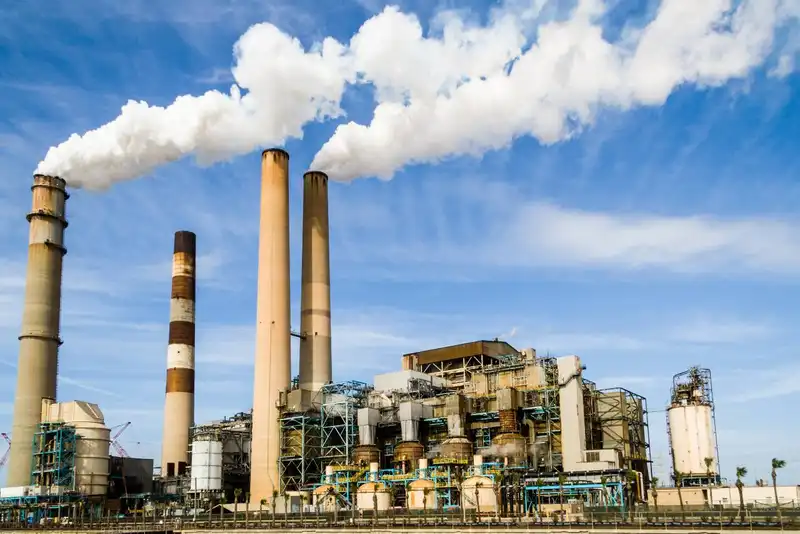
There are four essential types of logistics management that focus on different phases of the supply chain-
1. Supply Management
Supply management entails planning, ordering, and receiving raw materials or products that are needed by a specific deadline. This requires logistics managers to find the best form of transportation and storage for the specific item.
For example, perishable foods may need to be transported in refrigerated vehicles and stored in temperature-sensitive units until they are shipped to stores. Managers also need to consider the order size to ensure the mode of transportation can handle the supply volume.
2. Distribution Management
Once the goods are transported safely to storage or distribution centers, managers need to determine their final destination, such as retail or grocery stores. This process takes time, as it involves loading, transporting, and unloading items.
When the goods arrive at their final destination, employees must count and report stock usage. Distribution management is crucial as it monitors the activity of products as they move from warehouses to stores.
3. Production Management
Production management oversees the phases of merging raw materials and components into the final product. This process includes finding and retrieving the necessary materials to build the item. Managers need to correlate material arrival times with the production schedule to avoid stalling operations or storing early shipments.
4. Reverse Logistics and Product Returns
There may be excess materials that need to be reclaimed after production. This also applies to customer returns, as long as the product is unused. Therefore, logistics managers need to schedule pickups to retrieve extra supplies and products to reenter into inventory.
Goals of Logistics Management
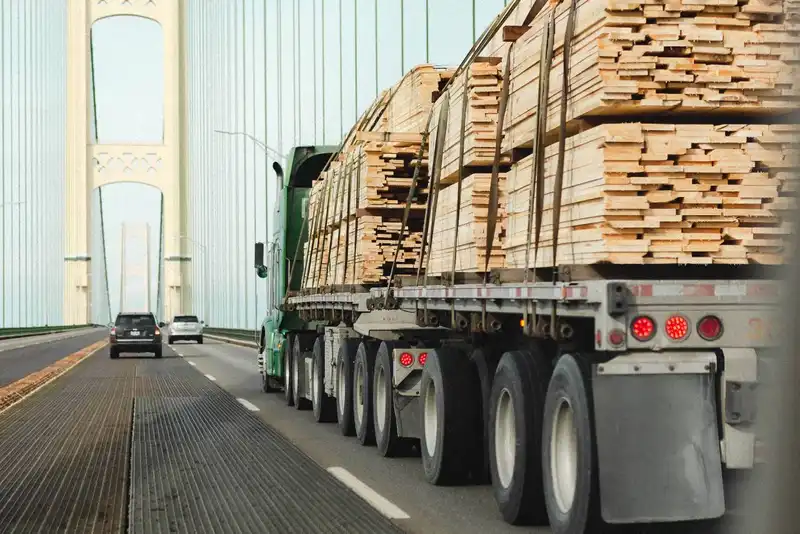
Without benchmarks, supply chains would run inefficiently and face the risk of falling behind the competition. By setting clear objectives, logistics management can minimize the impact of risks, such as missing deadlines, by optimizing workflow to work towards goals. Logistics managers should focus on six critical goals-
- Increase Efficiency
Managers can also improve logistics efficiency by finding vendors who perform quality inspections to reduce errors prior to shipping. By catching product mistakes before they reach customers, companies can avoid recollecting returned items.
- Decrease Response Time
With stock ordering software, companies can limit the inventory they have on-site to anticipate emerging demands. This enables businesses to operate reactively to each order rather than stockpiling large volumes of materials.
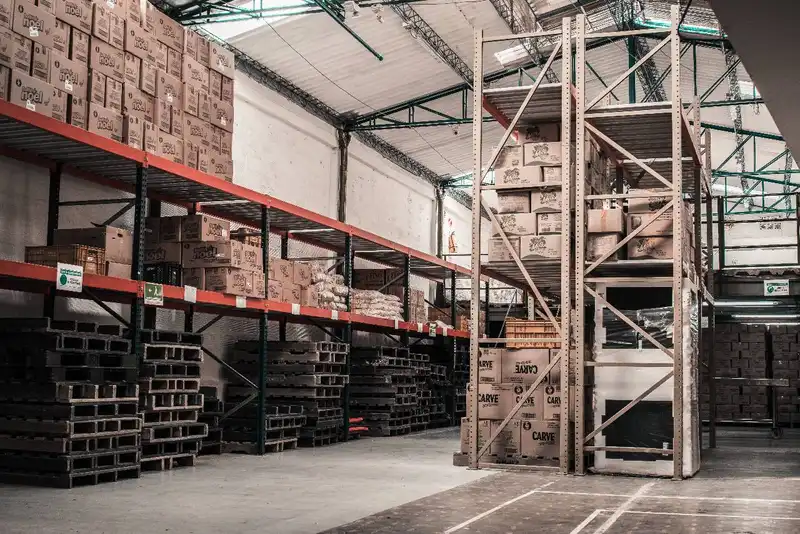
- Reduce Unexpected Events
Businesses used to counteract these events by maintaining healthy levels of safety stock or investing in the most expensive transportation option. However, companies now have access to advanced software that enhances logistics control. New solutions monitor operations and improve response time to malfunctions, minimizing the impact of unexpected events.
- Optimize Inventory Levels
Logistic managers should aim to minimize stock deployment to levels that both meet customer demand and reduce logistics costs. By calculating minimum stock levels for each item, companies can maintain healthy inventory turnover rates and availability.
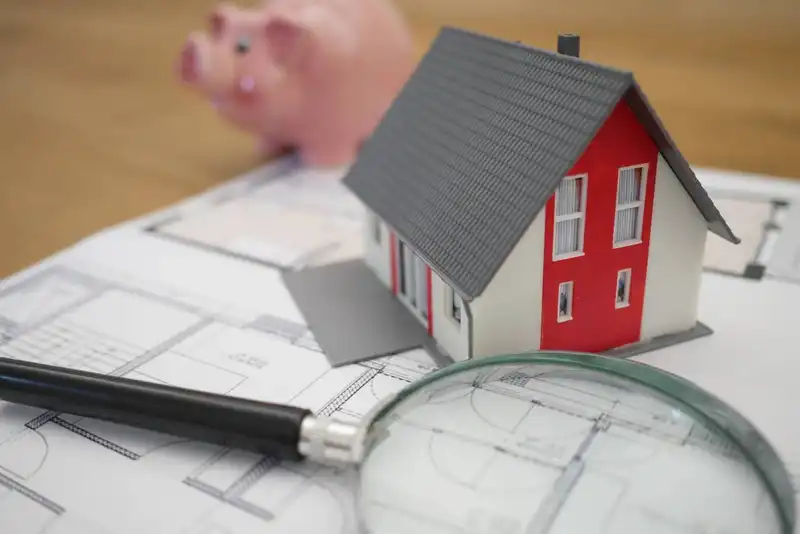
- Reduce Logistic Expenses
Generally, logistics companies that offer quick shipments for small orders come at a high cost. Therefore, the larger the order and longer the distance, the lower the shipping cost per unit. With the help of ordering software, businesses can group small shipments of similar products to reduce logistic expenses.
- Improve Quality
Logistic expenses are non-refundable, and if a product fails, the whole logistics process is repeated to retrieve the goods. Improving production quality ensures customers receive high-grade items, minimizing returns, and additional logistics expenses.
8 Logistics Management Processes
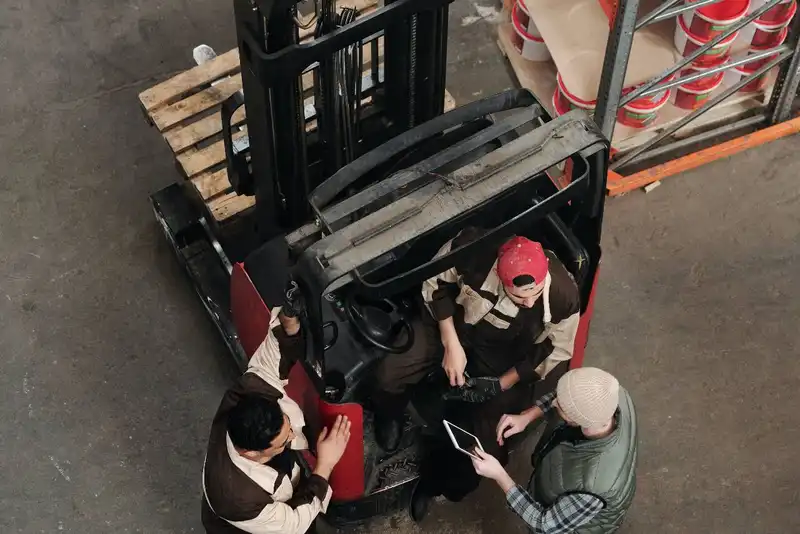
Through detailed logistics management at each supply chain level, businesses can pinpoint and eliminate inefficiencies that drain profits. Logistics managers can begin by focusing on 8 management processes-
1. Facility Inspection
Depending on the industry, managing a logistics facility can be challenging. Employees may face several workplace hazards, from dangerous chemicals to large shipping trucks. Without properly managing the activity within a facility, companies can face risks of non-compliance, inefficient operations, and an unsafe work environment.
By inspecting the facility monthly, managers can confirm operations abide by all safety regulations, and the facility remains fully stocked to streamline workflow. Management should check for-
- Damages
- Cleanliness
- Obstructions
- Proper Lighting
- Appropriate Safety Measures (fire extinguishers, ventilation, fire blankets)
- Reception Supplies
- Bathroom Supplies
- Equipment Function
- Secure Loading Dock
- Proper Storage
2. Forklift Inspection
Forklifts are used frequently in warehouses to retrieve goods and load trucks; therefore they need to be inspected often. If a forklift goes an extended time without proper inspection, workers can experience a breakdown that stalls operations. Malfunctions also present surrounding workers with safety hazards.
Managers must document inspections for reference in the event of a breakdown. With a detailed report, workers can determine if a malfunction could have been avoided or occurred before. The employee who performed the inspection needs to sign the report to assure supervisors that a thorough review was conducted.
When inspecting a forklift, the employee needs to check-
- Damages/Leaks
- Tires
- Guards
- Fluid Levels
- Seat Belt
- Motor
- Lights
- Functions
- Forklift Condition
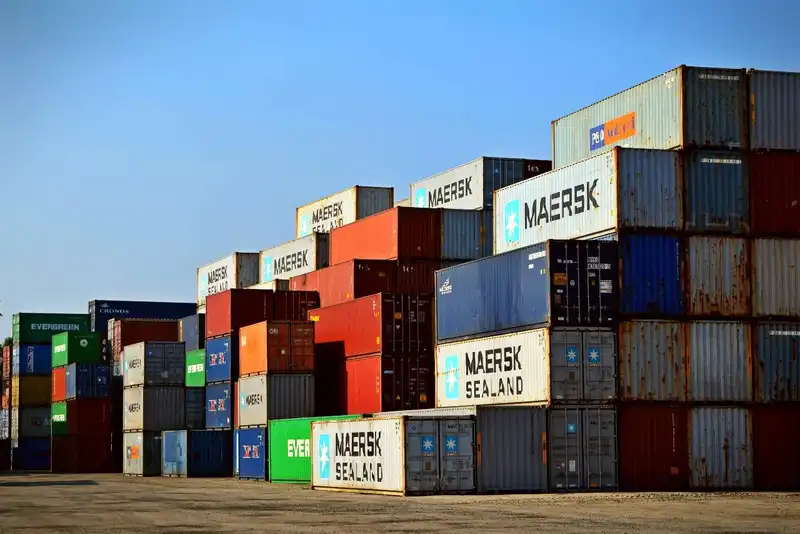
3. Inventory Management
Without an adequate inventory system in place, companies cannot control stock levels, storage, or human error. Improper inventory management can cost businesses unnecessary expenses from reconciling damages due to poor storage or high warehouse costs from overstocking.
Instead of relying on guesswork, companies should check their inventory management process to promote ordering and storing efficiency. Managers should consider several elements when placing and receiving an inventory order, including-
- Company Budget
- Current Stock Levels
- Order List
- Purchase Order Approval
- Tracking Details
- Arrival Time
- Return Damaged Goods
- Update Stock Records
4. ISO Container Inspection
It is crucial for companies to carefully and thoroughly check and track their shipping containers to ensure safe delivery. Businesses should inspect and document the condition of their containers by checking-
- Identification Number
- Doors
- Exterior Walls
- Roof
- Inside Walls (make sure it is empty)
- Floor
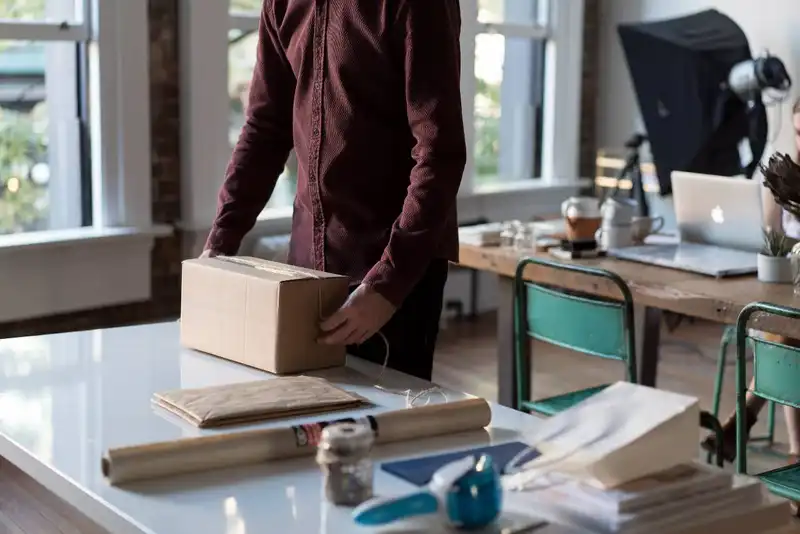
5. Order Fulfillment
Once a customer orders a product, logistics managers are responsible for orchestrating shipments to ensure fast and safe delivery. While this may be simple for minimal orders, fulfillment can become challenging when order volumes increase. Instead of a sole supervisor, large companies need to implement a comprehensive system to efficiently fulfill requests.
With a detailed and standardized fulfillment system, management can ensure that each order is processed accurately and efficiently. To successfully prepare and deliver orders, management needs to-
- Record Order Details
- Receive Payment
- Check Stock
- Request Items from Inventory
- Record Stock After Fulfillment
- Check Items for Quality
- Print Packing Lists
- Package Items Securely
- Weigh/Measure Package
- Schedule Delivery
- Forward Tracking Information to the Customer
6. Order Processing
For businesses with more straightforward transactions that don't call for an extended order fulfillment system, order processing can be used instead. While these operations essentially perform the same functions, order processing focuses more on customer feedback.
This is an excellent alternative to ensure that consumers are happy with their purchases. Unlike order fulfillment, this process only requires one supervisor rather than multiple employees.
To successfully complete customer transactions, managers should-
- Note Client/Order Details
- Record Salesperson
- Check Stock
- Receive Payment
- Schedule Delivery
- Contact Warehouse
- Forward Tracking Information to the Customer
- Follow Up with Customer
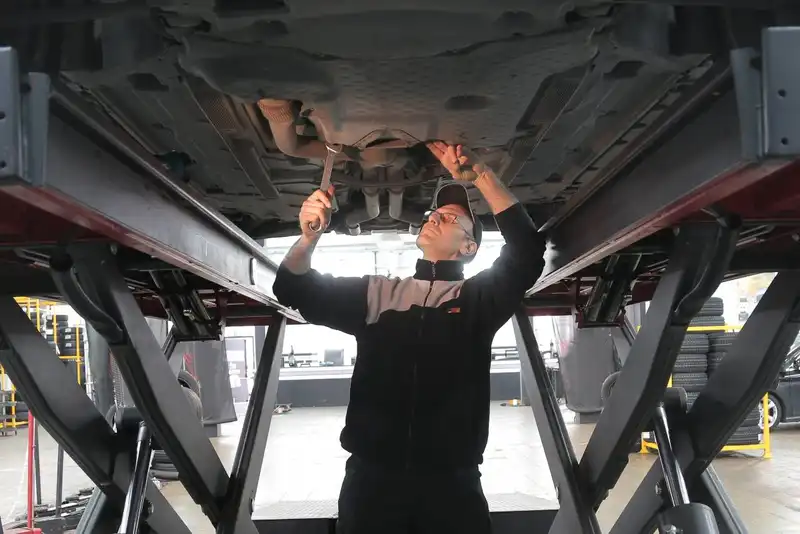
7. Vehicle Inspection
Regardless of the type of vehicle a business uses, they must perform annual inspections, even if they do not legally require routine checks. A broken-down car will not only disrupt shipment schedules but put employees at harm as well. With thorough annual inspections, businesses can save on long-term repair costs, keep operations on schedule, and get an overview of the fleet's condition.
During annual checks, employees should inspect-
- Brakes
- Bumpers
- Horn
- Seatbelts
- Air Conditioner
- Defrosters
- Windshield Wipers
- Lights
- Turn Signals
- Mirrors
- Tires
- Fluids
- Battery
- Windows
8. Warehouse Inspection
Performing a monthly warehouse check limits health and safety risks and maintains a hazard-free work environment. In addition to keeping employees safe, inspections ensure that workstations are abiding by company and state regulations. Therefore, if an incident occurs, the business can prove its compliance and avoid liability.
Management can ensure the warehouse meets regulations by checking for-
- Damages
- Cleanliness
- Obstructions
- Lighting
- Safety Measures
- Safe Storage
- Inspected Equipment
- Secure Stair Railings
- Clear Aisles
Tips for Successful Logistics Management
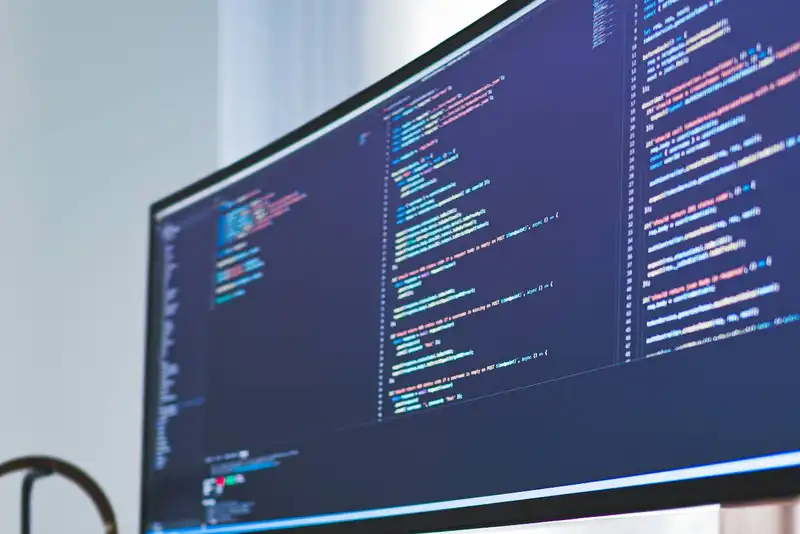
Successful logistics management requires extensive research and detailed planning. By outlining each phase, from production to distribution, companies can increase efficiency and profit margins. However, more extensive operations require intensive management practices.
The best practices for building successful logistics management plans include-
- Develop a Thorough Plan - The success of any operation relies on how well it was planned, and logistics management is no different. The more elements are addressed during the planning phase, the less the company has to rely on guesswork. Detailed outlines can mitigate risks and enhance workflow.
- Have a Backup Plan - Even the best plan has weaknesses, and businesses cannot avoid every threat. Therefore, having an alternate plan in place for unexpected events gives businesses flexibility and adaptability.
- Hire a Manager - Logistics requires an experienced manager that can handle the various supply chain facets. The manager should have excellent communication, multitasking, and people skills to work with all parties involved in the supply chain.
- Use Automation - By using modern software, such as ordering solutions, logistics managers can automate standard operations to streamline workflow. Software also enables easy shipment and inventory tracking.
- Learn from Mistakes - Companies need to understand that they will make mistakes at some point, but they must learn from them to avoid repetition. After a misstep, managers should evaluate why and how it happened to make the appropriate changes.
Logistics management is an essential process used to maintain control over the various supply chain functions. Successful management ensures that companies can meet order deadlines at a minimal cost to promote customer satisfaction and profits.