Inventory Analytics - 5 Metrics All Businesses Should Track
Introduction to Inventory Data Analytics
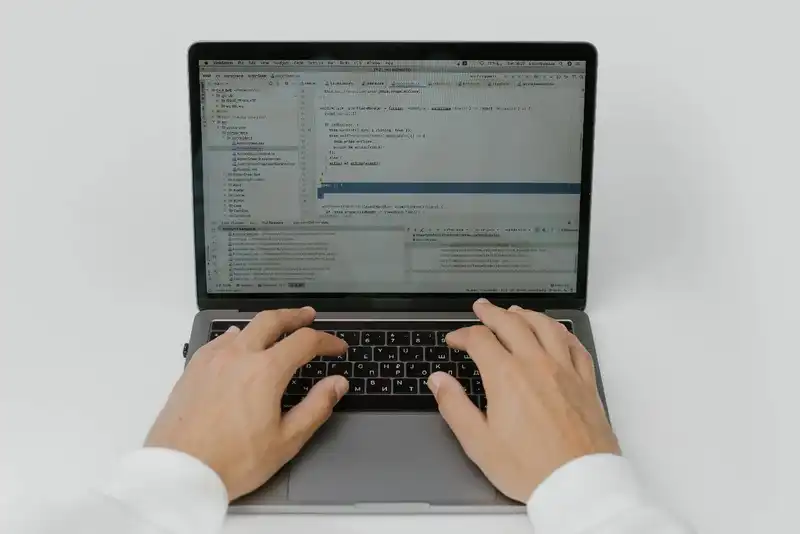
Retail businesses have the added burden of monitoring and managing inventory as it travels through the supply chain. This calls for a sophisticated tracking system that records and reports critical stock data.
With inventory analytics, companies gain insight into their inventory activity that defines crucial strengths and weaknesses. This enables businesses to improve their inventory control, productivity, efficiency, and profitability.
Why Businesses Need Inventory Analytics
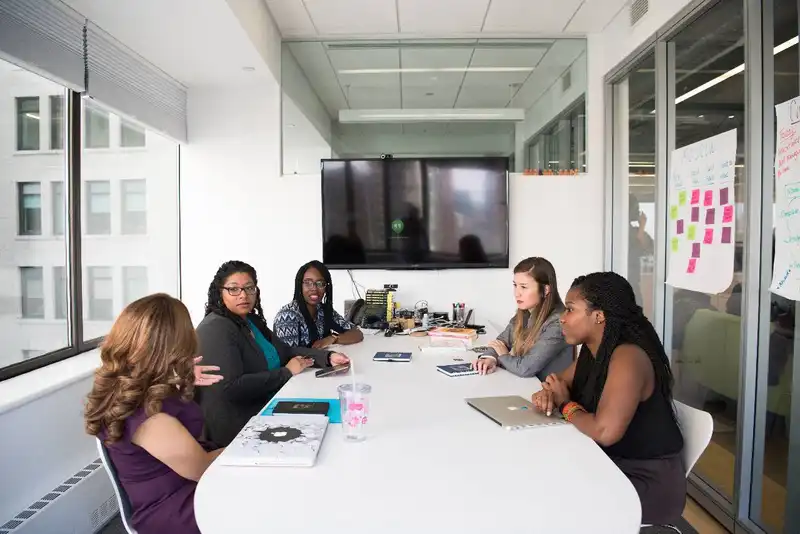
Inventory management can be a hassle if businesses do not have the right tools to monitor product activity. As supply chains expand, this task becomes even more challenging, as companies need to orchestrate manufacturing, distribution, and retail.
Inventory analytics provides critical insights into product management, so businesses can practice cost reduction and improve operations. However, studies show that only 34.7% of supply chains take advantage of inventory analytics simply because many companies remain unaware of its existence.
Without effective inventory analytics, companies can't efficiently track products as they work their way through the supply chain. This can result in discrepancies, unhealthy stock levels, and backorder.
On the other hand, inventory analytics utilizes modern software so companies can enhance their control. These solutions use machine learning to collect relevant real-time and historical data from existing systems to update inventory reports and metrics.
When coupled with demand forecasting software, predictive analytics can even project future sales and safety stock needs for inventory optimization. This ensures the businesses can satisfy fluctuating customer demand and maintain healthy inventory levels by anticipating emerging trends.
With analytics data, businesses can also improve business intelligence with sophisticated data science to improve product handling.
Inventory Analytics Metrics
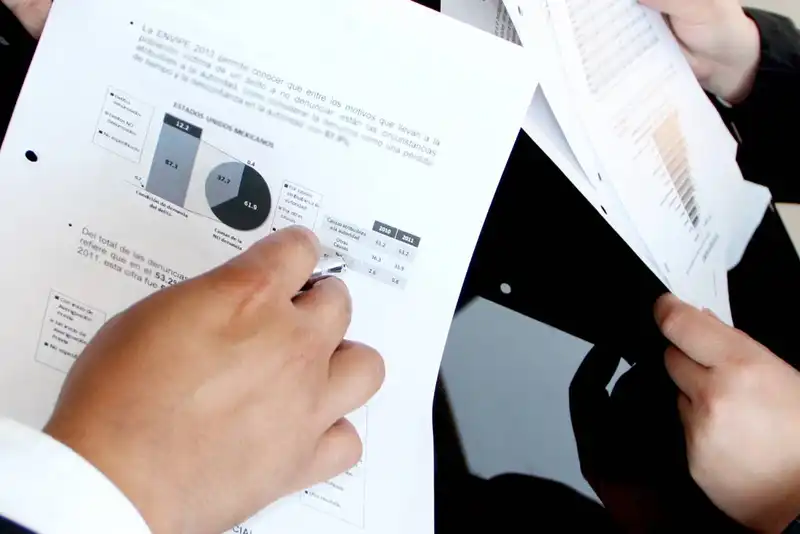
Distribution is a critical part of every inventory process and includes multiple systems that businesses must monitor to ensure they aren't incurring unnecessary costs. These systems can lag as a result of human error and poor management techniques.
Therefore, companies should track their performance and continuously improve their strategies. By tracking various key performance indicators (KPIs), distributors can clearly define their strengths and weaknesses.
Inventory Carrying Cost
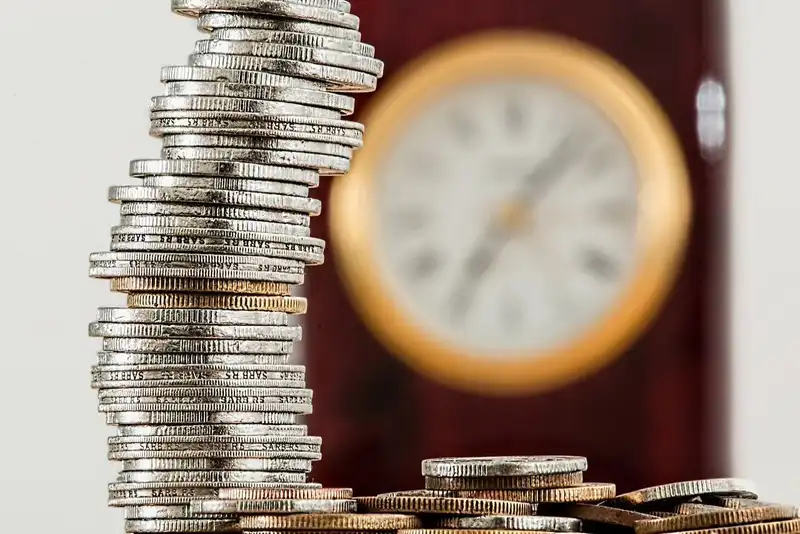
The inventory carrying cost measures how much money businesses must supplement to procure, store, and carry products. This means that carrying cost covers not only the retail price of the stock but also their
- Storage rent
- Insurance
- Warehouse utilities
- Taxes
- Depreciation
- Software tools
- Scanners
- Machinery
Unfortunately, many businesses are unaware of how much they invest in inventory, making it challenging to measure profitability. Therefore, distribution companies should designate a project manager to review the books and identify every expense related to inventory.
Once costs are defined, businesses typically calculate the total inventory carrying cost annually and convert the metric into a percentage. Usually, companies want their inventory carrying cost to stay below 25%.
Inventory Shrinkage
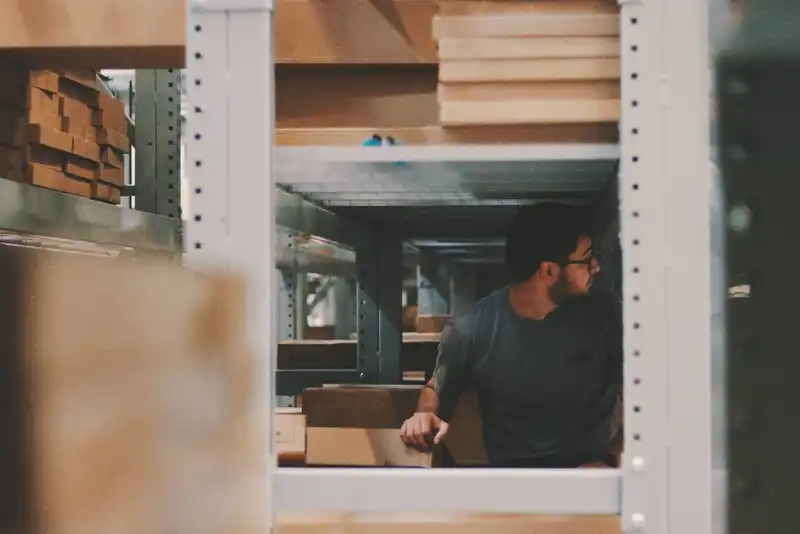
Inventory shrinkage is a metric centered around the difference between physical and recorded stock amounts. This type of inventory discrepancy can be the result of-
- Employee theft
- External theft
- Vendor fraud
- Human error
- Damage
Companies should view inventory shrinkage as a dollar amount, sales percentage, and inventory percentage to determine precisely how the discrepancies are impacting profits. Of course, distributers want inventory shrinkage rates to be as low as possible, but businesses should really focus on steadily decreasing disparities over time.
By monitoring trends, companies can detect emerging threats and evaluate inventory risks.
Average Cost per Unit
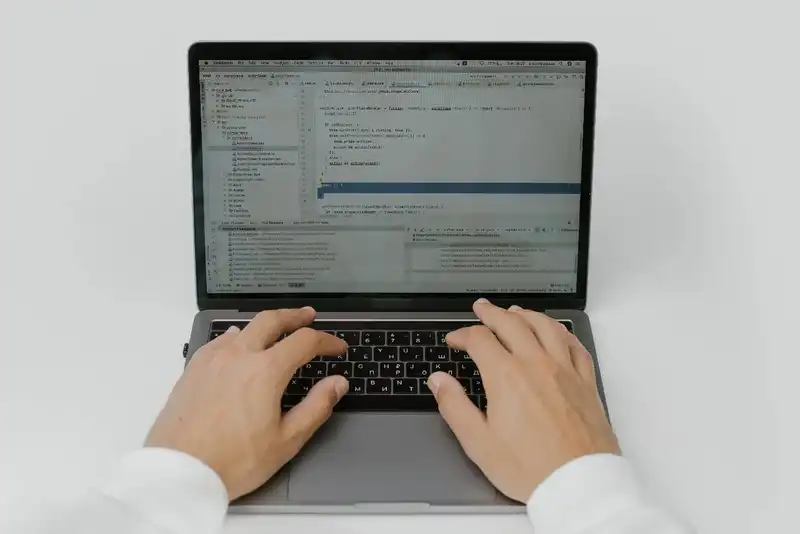
The average cost per unit is the total cost of production divided by the number of products manufactured. In other words, this quantity measures how much it costs to produce one unit, including the expense of-
- Direct materials
- Rent
- Machinery
- Utilities
- Labor
- Transportation
If any one of these expenses increases, then the overall cost of a product increases as a result. However, costs may also increase as a result of expensive inventory entering the system or a clerical error.
Average Number of Units Picked
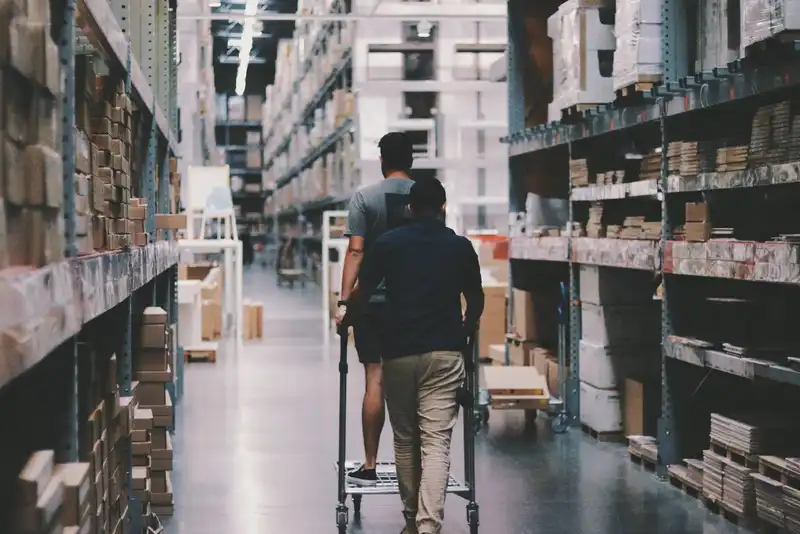
The average number of units picked refers to how many times a product is gathered during the order fulfillment process per day, week, and accounting cycle. This number directly relates to a distributor's productivity and enables them to optimize their warehouse layout. For example, if a business finds a product is gaining popularity, they can rearrange their storage to move the inventory closer to the order fulfillment center.
This can significantly reduce travel time, improving productivity, operational efficiency, and resource allocation. Companies should also consider tracking the number of units picked per hour, as some products may fluctuate according to the time of day. Inventory is also subject to seasonality which impacts storage techniques and organization.
Average Number of Units Put Away
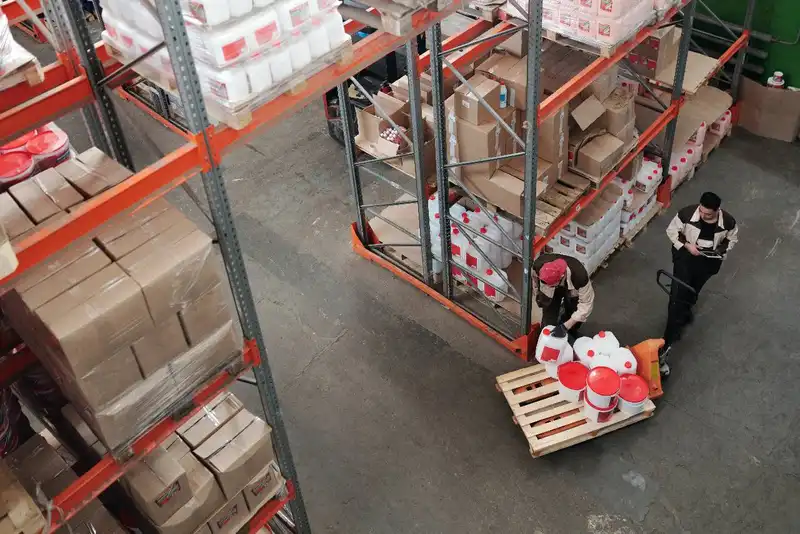
The average number of units put away is a metric that is especially important for the receiving team that handles incoming inventory. Much like the number of units picked, this KPI can be measured to fit any time limit, such as hourly, daily, weekly, and monthly. By monitoring the average number of units put away, distributors can assess customer demand and streamline their receiving and stocking processes.
Businesses should review and assess the value of inventory analytics to determine how it can impact their overall supply chain management.