8 Warehouse Storage Ideas to Instantly Optimize Efficiency
Every supply chain phase requires successful logistics management to keep operations on schedule. However, without a proper warehouse organization system, managers cannot arrange efficient product retrievals, shipments, and order fulfillment.
Cluttered storage can make it challenging to locate products, which can consequently delay deliveries and decrease customer satisfaction. Therefore, organizations should prioritize organizing their warehouse storage to ensure a smooth workflow and streamline logistics.
8 Warehouse Organization Ideas
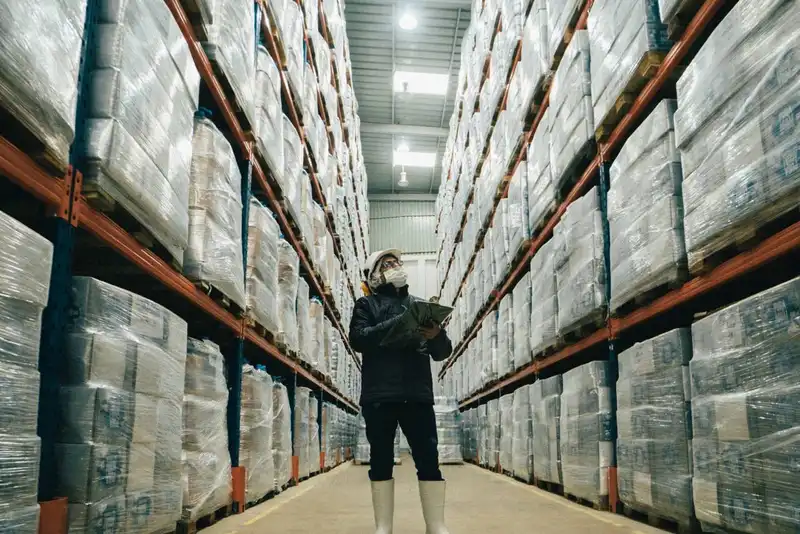
In addition to enhanced workflow, organizing warehouse storage enables companies to eliminate inefficiencies that cause unnecessary expenses. For example, by reorganizing stock, management can clear out obsolete inventory to make space for high-profit items.
By assessing the existing warehouse design and establishing a functional floor plan, companies can optimize floor space to enhance productivity. Businesses can start by considering 8 popular storage tactics.
1. Reevaluate the Warehouse Layout
An open warehouse floorplan is critical for ensuring a smooth workflow. Employees must be able to look up, find, and reach supplies easily. Workstations and communal areas also need to be free of obstructions to comply with safety regulations and streamline routine tasks.
The ideal warehouse layout will-
- Maximize floor space
- Reduce handling of goods
- Provide quick access to products
- Provide Storage Flexibility
- Create plenty of workspaces
- Offices
- Receiving Areas
- Storage Units
- Packing Stations
- Shipping Areas
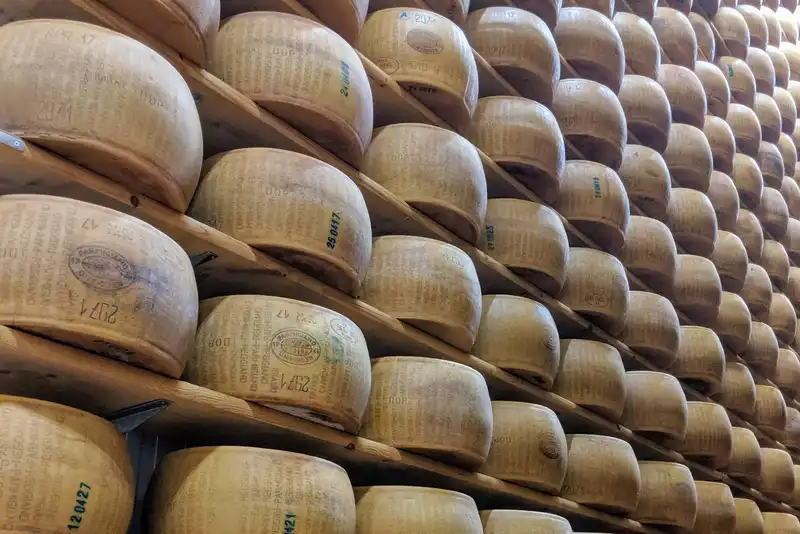
2. Utilize a Racking System
Storage racks and shelves are great tools to optimize vertical spaces and fit as much inventory into a warehouse as possible without cluttering aisleways. However, different industries call for different types and sizes of racks-
- Manufacturing companies require and prioritize space for equipment and production processes. Therefore, robust shelving for necessary supplies should surround workbenches, allowing aisles to accommodate forklifts and other machinery.
- Simple Production utilizes assembly lines to build products, requiring easy access to raw materials and components. This setup provides space around workbenches to implement additional shelving for the finished items.
- Distributors handle order fulfillment with a receive-and-ship business model that revolves around traditional inventory. Depending on the type of goods, distribution centers may need lightweight or robust shelving to store products, leaving aisles open for employees to stock and retrieve inventory.
3. Organize Inventory by Category
Once the proper storage containers and shelving are installed, management needs to determine the most efficient way to store the inventory. Raw materials and merchandise that are used frequently should be easily accessible to production and order fulfillment teams.
Many businesses use the ABC Analysis as an inventory management method to group stock into 3 categories-
- A - Most profitable or frequently used products that make up 80% of total stock activity, or 20% of total inventory.
- B - Items that account for 15% of inventory movement, or 30% of total stock.
- C - Least profitable products accounting for the remaining 5%, or 50% of total inventory.
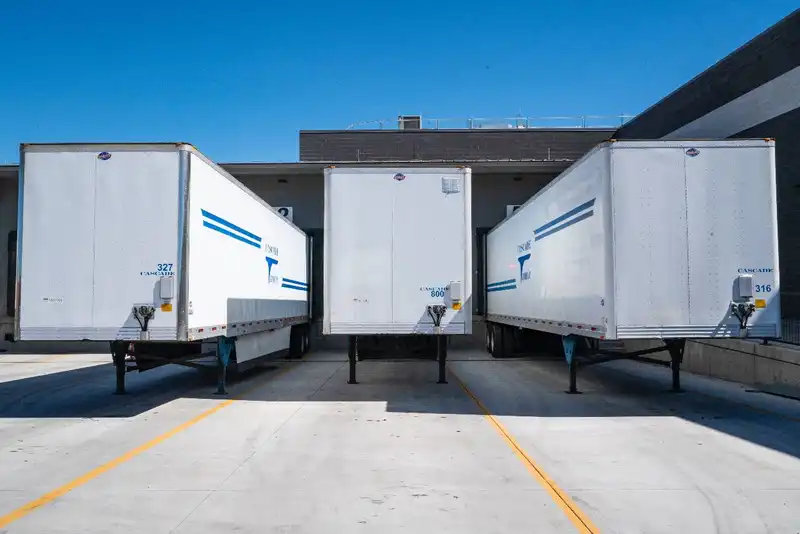
4. Label Everything
When shelves are fully stocked, every area needs to be labeled for transparency and safety. Aside from inventory, hazards, aisles, racks, and workstations should be labeled so workers can quickly grab supplies and stay aware of any risks.
For example, signs should alert forklift drivers of height and capacity restrictions to prevent accidents and break downs.
5. Streamline the Order Picking Process
Order picking is the most labor-intensive and error-prone job within the warehouse. If the warehouse is not organized and labeled to streamline this process, operations can be delayed, and employees could fulfill orders incorrectly.
Therefore, management needs to develop a layout that balances accuracy and speed within the picking process. Some best practices include-
- Place fulfillment areas and shelves near each other to reduce travel time.
- Store best-selling items closest to packing areas.
- Automate the picking process with barcode scanners and handheld devices.
Similar to order picking, receiving incoming shipments directly affects workflow and other warehouse operations. Staff should be able to quickly check and stock goods in the appropriate storage units without disrupting other processes. Without a successful receiving process, employees could mislabel or misplace products, confusing the order fulfillment system.
Companies can enhance the inventory acceptance process by-
- Allocating space for staff to receive and check stock.
- Using an inventory management system to monitor real-time stock levels.
- Automating the unloading process with conveyor belts and forklifts.
- Labeling products to enhance quality assurance.
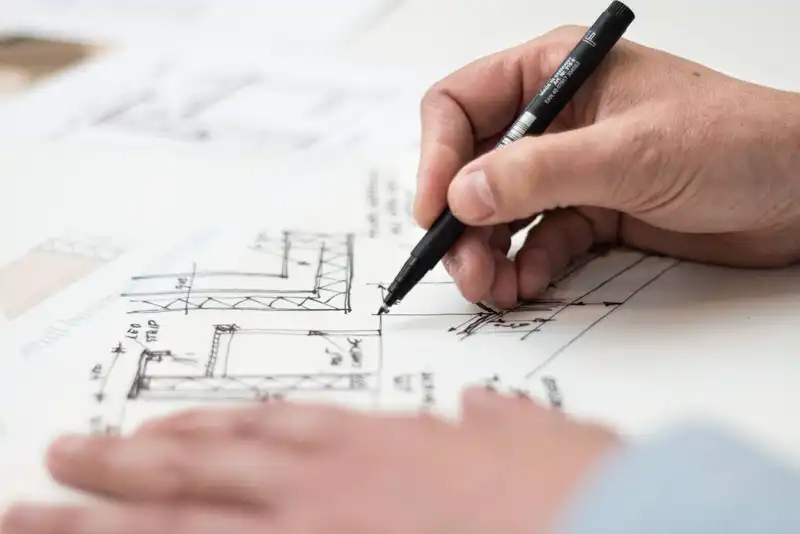
7. Conduct Routine Maintenance
To keep the warehouse clean and in working condition, management should implement a maintenance schedule. Staff can begin the workday with a morning meeting to address any issues regarding cleanliness, hazards, or discrepancies.
After work, designated employees should clean the work areas, remove obstructions, and return misplaced items. By performing these simple measures daily, companies can improve their productivity and safety.
8. Review the Warehouse Floor Plan
Businesses should periodically review the warehouse to ensure the layout still promotes operational efficiency. Management can conduct walkthroughs, ask staff for suggestions, and monitor key performance metrics (KPIs) to determine how to further enhance workflow.
With a successful warehouse management system, workers can easily navigate through the facility to find supplies and complete tasks. Organized workbenches and inventory promote accessibility and efficiency so companies can maintain target production levels.